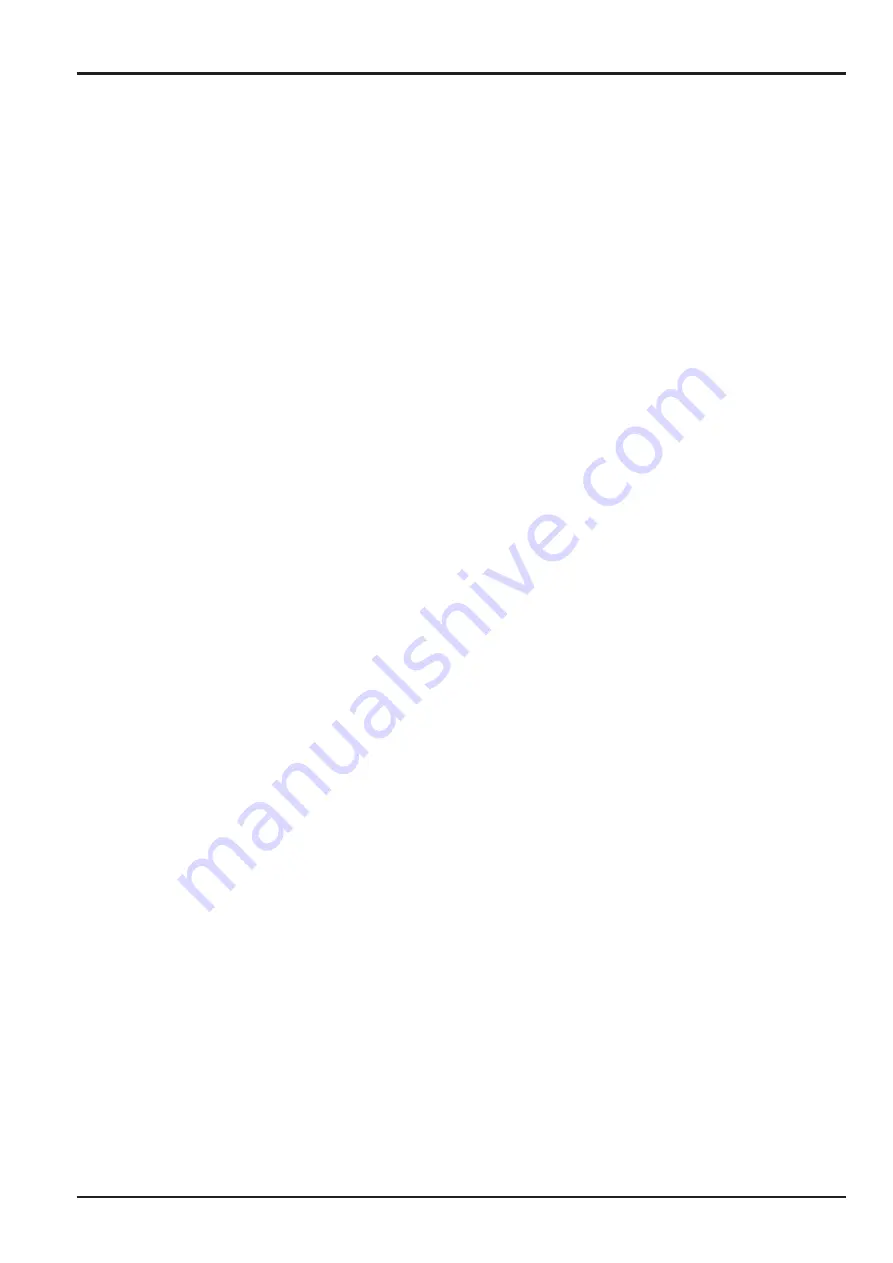
12 - 3
Operation (cont'd)
The high temperature, high pressure refrigerant is forced by
compressor action into the expansion valve
4
, which meters
the amount of refrigerant entering the evaporator. In the
expansion valve the refrigerant instantaneously expands to
become a low pressure, low temperature liquid.
The refrigerant is drawn through the evaporator coil
5
by the
suction of the compressor. The temperature of refrigerant is
now considerably below that of the air being drawn across
the evaporator coil by the blowers. Heat is transferred from
the ambient and recirculated air to the refrigerant, causing the
low pressure liquid to vaporise and become a low pressure
gas. Moisture in the air condenses on the evaporator coil and
is drained away via condensate.
Cool de-humidified air is emitted through air vents into the
cab.
The low temperature, low pressure, high heat content
refrigerant gas, is now drawn by suction back to the
compressor, where the cycle is completed.
Control
Control of the system is achieved by the cyclic action of the
compressor's electromagnetic clutch. When current is fed to
the field coil of the compressor's clutch, a magnetic field
develops between the field coil and the armature which pulls
the field coil, complete with clutch assembly, onto the
compressor's rotor. Since the clutch assembly is turned
constantly by the crankshaft pulley drive belt, the compressor
armature turns, starting the refrigeration cycle.
Current is fed to the field coil through three series switches
whose contacts are controlled by the following:
1
The manual switch
D
in the cab
2
The thermostat switch monitoring the evaporator
temperature
3
The high and low level pressure switch
Switch
D
will start the refrigeration cycle provided that the
ambient temperature in the cab is greater than 0°C and the
refrigerant pressure remains within the specified limits.
The thermostat has its sensor inserted in the evaporator coil.
It controls the refrigeration cycle by switching the compressor
clutch on and off to prevent freezing of the condensate on the
evaporator coil.
The pressure level switch is housed in a common assembly
located on the Receiver Drier. If the refrigerant pressure
exceeds the upper pressure limit specified or falls below the
lower limit, the contacts will open and the clutch will
disengage, closing down the refrigeration cycle.
Pressures Switch Settings
High Pressure Switch 28 bar (406 lbf/ in
2
)
Low Pressure Switch 2.1 bar (30.4 lbf/ in
2
)
Safety Procedures
The air conditioning system includes a pressurised closed
circuit containing a non-CFC, environmentally friendly
refrigerant, Type R-134a. Any service procedure which
breaks into the closed circuit and therefore requires
discharging of the system, must only be carried out by
service personnel with specialist knowledge of air
conditioning systems. The following guidelines should be
adhered to by all personnel servicing the air conditioning
system.
!
!
WARNING
The air conditioning system is a closed loop system and
contains pressurised refrigerant. No part of the system
should be disconnected until the system has been
discharged by a refrigeration engineer. or a suitable
trained person You can be severely frostbitten or injured
by escaping refrigerant
4-3-4-1/2
!
!
CAUTION
Do not operate the air conditioning system when there is
no refrigerant in the system, otherwise the compressor
will be damaged.
4-3-4-4
1
It is critical that the correct refrigerant (R-134a) is used
and that charging is done only by qualified personnel.
As a precaution, in case of accidental leakage,
discharging and charging of the vehicle refrigerant
system must be conducted in a well ventilated area.
2
Containers of refrigerant should be stored in a cool
environment away from direct sunlight.
!
!
WARNING
Do not carry out welding operations close to the air
conditioning refrigerant circuit. A poisonous gas is
produced when refrigerant comes into contact with
naked flames. Do not smoke or allow naked flames close
to the refrigerant circuit.
BF 1- 9
3
Do Not
perform welding operations close to refrigerant
hoses (maintain a distance of at least 0.5m from hoses).
4
Do Not
steam clean refrigerant system components.
5
When charging or discharging the refrigerant system
refrain from smoking. Naked flames must not be allowed
in the immediate vicinity. The refrigerant does not give
off a poisonous odour, however, when it comes into
contact with a naked flame, a poisonous gas is
produced.
6
When handling refrigerant, rubber gloves and goggles
should be worn. Operators should ensure that no
refrigerant comes into contact with the skin. Particular
care should be taken when connecting or disconnecting
charging hoses or pressure switches. When these
components are connected to the system, a short
release of refrigerant occurs. This results in a high
velocity, very cold gas being emitted from the
connection point.
Section B
Body & Framework
9803/6400
Section B
12 - 3
Issue 1
Air Conditioning
Содержание JS 200 Series
Страница 57: ...9 1 Section 3 Routine Maintenance 9803 6400 Section 3 9 1 Issue 2 Component Location Diagram...
Страница 67: ...2 1 Section B Body Framework 9803 6400 Section B 2 1 Issue 2 Undercarriage Dimensions JS200 JS220...
Страница 68: ...2 2 Section B Body Framework 9803 6400 Section B 2 2 Issue 2 Undercarriage Dimensions JS200LC JS220LC...
Страница 69: ...2 3 Section B Body Framework 9803 6400 Section B 2 3 Issue 2 Undercarriage Dimensions JS240 JS260...
Страница 70: ...2 4 Section B Body Framework 9803 6400 Section B 2 4 Issue 2 Undercarriage Dimensions JS240LC JS260LC...
Страница 113: ......
Страница 137: ...5 3 Section C Electrics 9803 6400 Section C 5 3 Issue 2 Pump Control FLOW CHART...
Страница 140: ...5 6 Section C Electrics 9803 6400 Section C 5 6 Issue 1 Pump Control Cushioned Boom Starting continued Flow Chart...
Страница 143: ...5 9 Section C Electrics 9803 6400 Section C 5 9 Issue 1 Pump Control Pressure Increasing System continued Flow Chart...
Страница 150: ...5 16 Section C Electrics 9803 6400 Section C 5 16 Issue 1 Pump Control Power Supply Cut Delay Flow Chart...
Страница 154: ...5 20 Section C Electrics 9803 6400 Section C 5 20 Issue 1 Pump Control Swing brake Swing lock continued Flow Chart...
Страница 155: ...5 21 Section C Electrics 9803 6400 Section C 5 21 Issue 1 Pump Control Lever Lock Circuit Diagram Time Chart...
Страница 157: ...5 22 Section C Electrics 9803 6400 Section C 5 22 Issue 1 Pump Control Lever Lock continued Flow Chart...
Страница 201: ...10 7 Section C Electrics 9803 6400 Section C 10 7 Issue 1 CAPs II Diagnostic system K C...
Страница 215: ...Section E Section E Hydraulics 9803 6400 Issue 2 3 2 3 2 Schematics...
Страница 217: ...Section E Section E 9803 6400 Issue 2 3 3 3 3 Hydraulics Schematics...
Страница 218: ...3 5 Section E Hydraulics 9803 6400 Section E 3 5 Issue 1 Schematics Shuttle Block JS200 JS240...
Страница 232: ...10 1 Section E Hydraulics 9803 6400 Section E 10 1 Issue 1 Hydraulic Pump JS200 JS240...
Страница 233: ...10 2 Section E Hydraulics 9803 6400 Section E 10 2 Issue 1 Hydraulic Pump JS200 JS240...
Страница 234: ...10 3 Section E Hydraulics 9803 6400 Section E 10 3 Issue 1 Hydraulic Pump JS200 JS240...
Страница 263: ...30 2 Section E Hydraulics 9803 6400 Section E 30 2 Issue 1 Control Valve JS200 JS240...
Страница 264: ...30 3 Section E Hydraulics 9803 6400 Section E 30 3 Issue 1 Control Valve JS200 JS240...
Страница 265: ...30 4 Section E Hydraulics 9803 6400 Section E 30 4 Issue 1 Control Valve JS200 JS240...
Страница 266: ...30 5 Section E Hydraulics 9803 6400 Section E 30 5 Issue 1 Control Valve JS200 JS240...
Страница 267: ...30 6 Section E Hydraulics 9803 6400 Section E 30 6 Issue 1 Control Valve JS200 JS240...
Страница 268: ...30 7 Section E Hydraulics 9803 6400 Section E 30 7 Issue 1 Control Valve JS200 JS240...
Страница 276: ...31 8 Section E Hydraulics 9803 6400 Section E 31 8 Issue 1 Control Valve JS200 JS240 Operation continued...
Страница 277: ...31 9 Section E Hydraulics 9803 6400 Section E 31 9 Issue 1 Control Valve JS200 JS240 Operation continued...
Страница 278: ...31 10 Section E Hydraulics 9803 6400 Section E 31 10 Issue 1 Control Valve JS200 JS240 Operation continued Travel Fig 4...
Страница 279: ...31 11 Section E Hydraulics 9803 6400 Section E 31 11 Issue 1 Control Valve JS200 JS240 Operation continued...
Страница 280: ...31 12 Section E Hydraulics 9803 6400 Section E 31 12 Issue 1 Control Valve JS200 JS240 Operation continued...
Страница 281: ...31 13 Section E Hydraulics 9803 6400 Section E 31 13 Issue 1 Control Valve JS200 JS240 Operation continued...
Страница 282: ...31 14 Section E Hydraulics 9803 6400 Section E 31 14 Issue 1 Control Valve JS200 JS240 Operation continued...
Страница 283: ...31 15 Section E Hydraulics 9803 6400 Section E 31 15 Issue 1 Control Valve JS200 JS240 Operation continued...
Страница 286: ...31 18 Section E Hydraulics 9803 6400 Section E 31 18 Issue 1 Control Valve JS200 JS240 Operation continued...
Страница 314: ...50 2 Section E Hydraulics 9803 6400 Section E 50 2 Issue 1 Solenoid Valve 8 spool JS200 JS240 Schmatics Technical Data...
Страница 327: ...51 12 Section E Hydraulics 9803 6400 Section E 51 12 Issue 1 Solenoid Valve 8 spool...
Страница 328: ...55 1 Schematic Section E Hydraulics 9803 6400 Section E 55 1 Issue 1 Shuttle Valve...
Страница 330: ...55 3 Schematic Section E Hydraulics 9803 6400 Section E 55 3 Issue 1 Cushion Valves...
Страница 363: ...75 10 Section E Hydraulics 9803 6400 Section E 75 10 Issue 1 Hydraulic Rams Ram Piston Head Nut JS00980...
Страница 442: ...2 2 Schematics specifications Section F Transmission 9803 6400 Section F 2 2 Issue 1 Motor Gearbox...
Страница 452: ...3 10 Section F Transmission 9803 6400 Section F 3 10 Issue 1 Motor Gearbox Fig 8 1 1st Speed Fixed Mode...
Страница 481: ...7 15 Section F Transmission 9803 6400 Section F 7 15 Issue 2 Motor...
Страница 482: ...7 16 Section F Transmission 9803 6400 Section F 7 16 Issue 1 Motor...
Страница 530: ...Contents Page No Routine Maintenance See Section 3 Technical Data 1 1 i Engine 9803 6400 i Issue 1 Section K Section K...