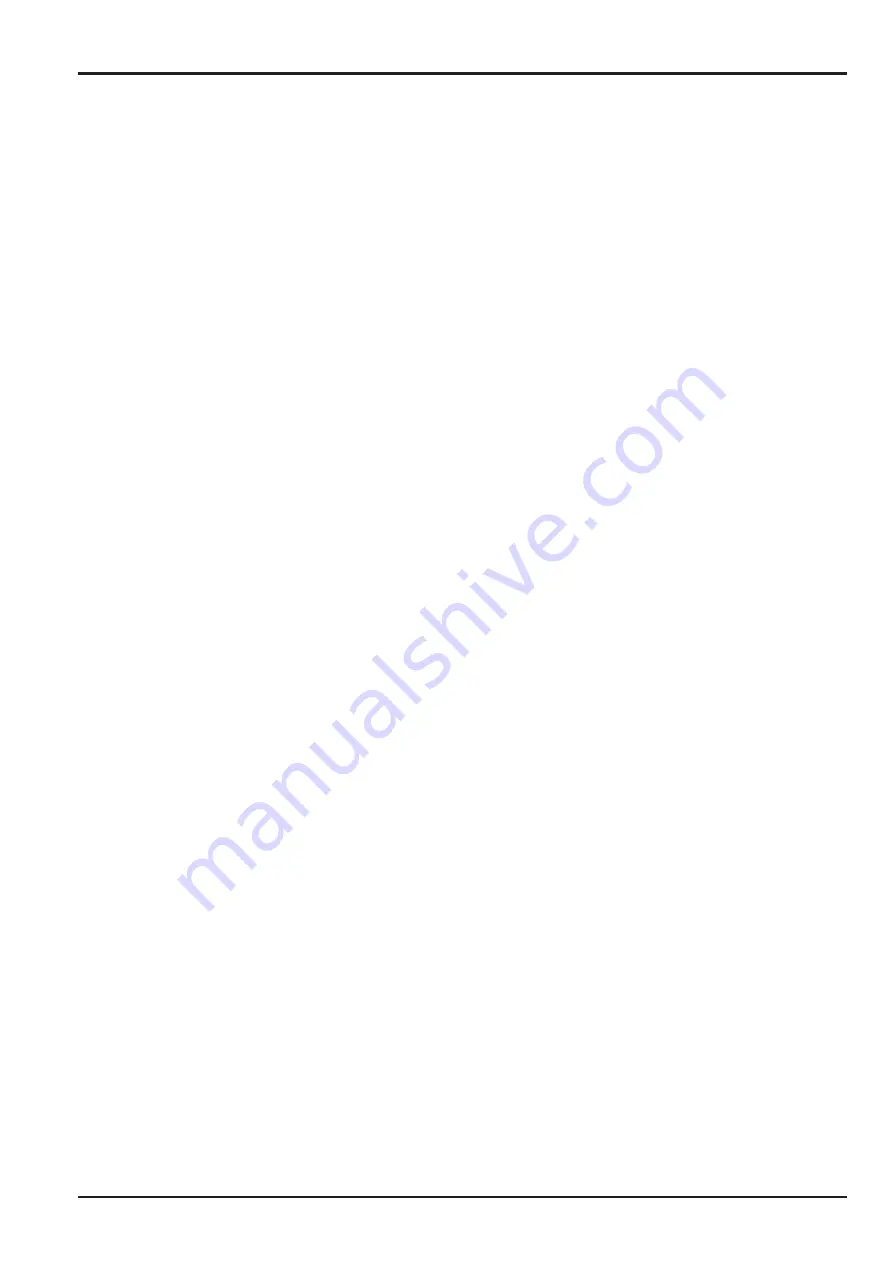
71 - 1
Section E
Hydraulics
9803/6400
Section E
71 - 1
Issue 1
Hydraulic Rams
Precautions during use JS200/JS240
1. Precautions when installing the ram on the machine
When installing and removing from the machine, suspend the ram safely.
Suspending the ram by the piping is not only dangerous, but can also cause damage to the cylinder.
Secure the rod with a band. It is very dangerous if the rod should fly out unexpectedly. Also, the rod can be damaged and
become unusable.
Welding after installing the ram may result in damage.
If electric welding is done even at a point away from the ram, there may be sparking inside the ram and it will become
necessary to replace the ram with a new one.
When painting the machine, mask the ram.
If paint adheres to the rod surface or to the wiper ring and the ram is worked, the wiper ring cannot function properly and foreign
matter from the outside and paint can easily enter the ram and cause damage to the seals, drastically shortening the life of the
ram.
Install the ram only when it is clean.
2. Caution During Use
Use only under designated conditions.
If hydraulic oil other than the designated oil is used, the seals quickly degenerate and become damaged. If the relief valve is
set at a value higher than specified, it may cause ram damage and is dangerous.
In high temperature environments (Approx. 90°C and above) or low temperature environments (Below -20°C), seals quickly
become damaged. Special seal materials are necessary so check to see if the ram that you are using is suitable or not.
The number one cause of ram oil leakage is due to rod damage. Be careful not to damage the rod.
Warm up sufficiently before beginning work.
In cold conditions the rod seals may be frozen so if the ram is operated at maximum pressure and maximum speed, the seals
will be damaged.
There is a large amount of air in a new ram or one which has been left for a long time, so the ram will not operate smoothly.
Also, if pressure is applied suddenly without bleeding the air, high temperature will be generated due to adiabatic compression
and the seals may burn.
Before beginning work, always move the ram at full stroke with no load and expel air from the cylinder.
When stopping or storing, do it at a safe and fixed position.
The installed ram cannot maintain the same position for a long period of time.
The oil inside the ram may leak and due to the temperature change in the hydraulic oil, the hydraulic oil volume changes. For
that reason, the ram expands and contracts, causing unexpected movement to the machine which is dangerous. Stop or store
the machine in a safe and fixed position.
3. Maintenance, Inspection Points.
Carry out daily maintenance and inspection.
The key point for correct long-term ram function is daily maintenance and inspection. Carry out maintenance and inspection so
that the ram functions fully at all times. Always remove any mud, water, dust or oil film adhering to the rod and keep it in normal
condition. However, when cleaning the wiper ring and seals, do not get them wet with water but wipe clean with a rag. If
leaving for more than one week, apply anti-rust oil to the rod surface.
Use genuine JCB parts when replacing parts.
If parts other than genuine JCB parts are used, the desired results may not be obtained. Use only genuine JCB parts.
Caution during disassembly and reassemble.
Disassembling the ram while it is still installed on the machine can be dangerous as unexpected movements of the machine can
occur. Remove the ram from the machine and then disassemble.
If reassembled with dirty hands, foreign matter can enter the ram causing a shorter life span and also the other hydraulic
equipment may be damaged. Reassemble in a clean state.
Follow the instructions in the diagrams regarding torque tightening for screwed parts. If the torque is too high or too low, it can
cause damage.
Содержание JS 200 Series
Страница 57: ...9 1 Section 3 Routine Maintenance 9803 6400 Section 3 9 1 Issue 2 Component Location Diagram...
Страница 67: ...2 1 Section B Body Framework 9803 6400 Section B 2 1 Issue 2 Undercarriage Dimensions JS200 JS220...
Страница 68: ...2 2 Section B Body Framework 9803 6400 Section B 2 2 Issue 2 Undercarriage Dimensions JS200LC JS220LC...
Страница 69: ...2 3 Section B Body Framework 9803 6400 Section B 2 3 Issue 2 Undercarriage Dimensions JS240 JS260...
Страница 70: ...2 4 Section B Body Framework 9803 6400 Section B 2 4 Issue 2 Undercarriage Dimensions JS240LC JS260LC...
Страница 113: ......
Страница 137: ...5 3 Section C Electrics 9803 6400 Section C 5 3 Issue 2 Pump Control FLOW CHART...
Страница 140: ...5 6 Section C Electrics 9803 6400 Section C 5 6 Issue 1 Pump Control Cushioned Boom Starting continued Flow Chart...
Страница 143: ...5 9 Section C Electrics 9803 6400 Section C 5 9 Issue 1 Pump Control Pressure Increasing System continued Flow Chart...
Страница 150: ...5 16 Section C Electrics 9803 6400 Section C 5 16 Issue 1 Pump Control Power Supply Cut Delay Flow Chart...
Страница 154: ...5 20 Section C Electrics 9803 6400 Section C 5 20 Issue 1 Pump Control Swing brake Swing lock continued Flow Chart...
Страница 155: ...5 21 Section C Electrics 9803 6400 Section C 5 21 Issue 1 Pump Control Lever Lock Circuit Diagram Time Chart...
Страница 157: ...5 22 Section C Electrics 9803 6400 Section C 5 22 Issue 1 Pump Control Lever Lock continued Flow Chart...
Страница 201: ...10 7 Section C Electrics 9803 6400 Section C 10 7 Issue 1 CAPs II Diagnostic system K C...
Страница 215: ...Section E Section E Hydraulics 9803 6400 Issue 2 3 2 3 2 Schematics...
Страница 217: ...Section E Section E 9803 6400 Issue 2 3 3 3 3 Hydraulics Schematics...
Страница 218: ...3 5 Section E Hydraulics 9803 6400 Section E 3 5 Issue 1 Schematics Shuttle Block JS200 JS240...
Страница 232: ...10 1 Section E Hydraulics 9803 6400 Section E 10 1 Issue 1 Hydraulic Pump JS200 JS240...
Страница 233: ...10 2 Section E Hydraulics 9803 6400 Section E 10 2 Issue 1 Hydraulic Pump JS200 JS240...
Страница 234: ...10 3 Section E Hydraulics 9803 6400 Section E 10 3 Issue 1 Hydraulic Pump JS200 JS240...
Страница 263: ...30 2 Section E Hydraulics 9803 6400 Section E 30 2 Issue 1 Control Valve JS200 JS240...
Страница 264: ...30 3 Section E Hydraulics 9803 6400 Section E 30 3 Issue 1 Control Valve JS200 JS240...
Страница 265: ...30 4 Section E Hydraulics 9803 6400 Section E 30 4 Issue 1 Control Valve JS200 JS240...
Страница 266: ...30 5 Section E Hydraulics 9803 6400 Section E 30 5 Issue 1 Control Valve JS200 JS240...
Страница 267: ...30 6 Section E Hydraulics 9803 6400 Section E 30 6 Issue 1 Control Valve JS200 JS240...
Страница 268: ...30 7 Section E Hydraulics 9803 6400 Section E 30 7 Issue 1 Control Valve JS200 JS240...
Страница 276: ...31 8 Section E Hydraulics 9803 6400 Section E 31 8 Issue 1 Control Valve JS200 JS240 Operation continued...
Страница 277: ...31 9 Section E Hydraulics 9803 6400 Section E 31 9 Issue 1 Control Valve JS200 JS240 Operation continued...
Страница 278: ...31 10 Section E Hydraulics 9803 6400 Section E 31 10 Issue 1 Control Valve JS200 JS240 Operation continued Travel Fig 4...
Страница 279: ...31 11 Section E Hydraulics 9803 6400 Section E 31 11 Issue 1 Control Valve JS200 JS240 Operation continued...
Страница 280: ...31 12 Section E Hydraulics 9803 6400 Section E 31 12 Issue 1 Control Valve JS200 JS240 Operation continued...
Страница 281: ...31 13 Section E Hydraulics 9803 6400 Section E 31 13 Issue 1 Control Valve JS200 JS240 Operation continued...
Страница 282: ...31 14 Section E Hydraulics 9803 6400 Section E 31 14 Issue 1 Control Valve JS200 JS240 Operation continued...
Страница 283: ...31 15 Section E Hydraulics 9803 6400 Section E 31 15 Issue 1 Control Valve JS200 JS240 Operation continued...
Страница 286: ...31 18 Section E Hydraulics 9803 6400 Section E 31 18 Issue 1 Control Valve JS200 JS240 Operation continued...
Страница 314: ...50 2 Section E Hydraulics 9803 6400 Section E 50 2 Issue 1 Solenoid Valve 8 spool JS200 JS240 Schmatics Technical Data...
Страница 327: ...51 12 Section E Hydraulics 9803 6400 Section E 51 12 Issue 1 Solenoid Valve 8 spool...
Страница 328: ...55 1 Schematic Section E Hydraulics 9803 6400 Section E 55 1 Issue 1 Shuttle Valve...
Страница 330: ...55 3 Schematic Section E Hydraulics 9803 6400 Section E 55 3 Issue 1 Cushion Valves...
Страница 363: ...75 10 Section E Hydraulics 9803 6400 Section E 75 10 Issue 1 Hydraulic Rams Ram Piston Head Nut JS00980...
Страница 442: ...2 2 Schematics specifications Section F Transmission 9803 6400 Section F 2 2 Issue 1 Motor Gearbox...
Страница 452: ...3 10 Section F Transmission 9803 6400 Section F 3 10 Issue 1 Motor Gearbox Fig 8 1 1st Speed Fixed Mode...
Страница 481: ...7 15 Section F Transmission 9803 6400 Section F 7 15 Issue 2 Motor...
Страница 482: ...7 16 Section F Transmission 9803 6400 Section F 7 16 Issue 1 Motor...
Страница 530: ...Contents Page No Routine Maintenance See Section 3 Technical Data 1 1 i Engine 9803 6400 i Issue 1 Section K Section K...