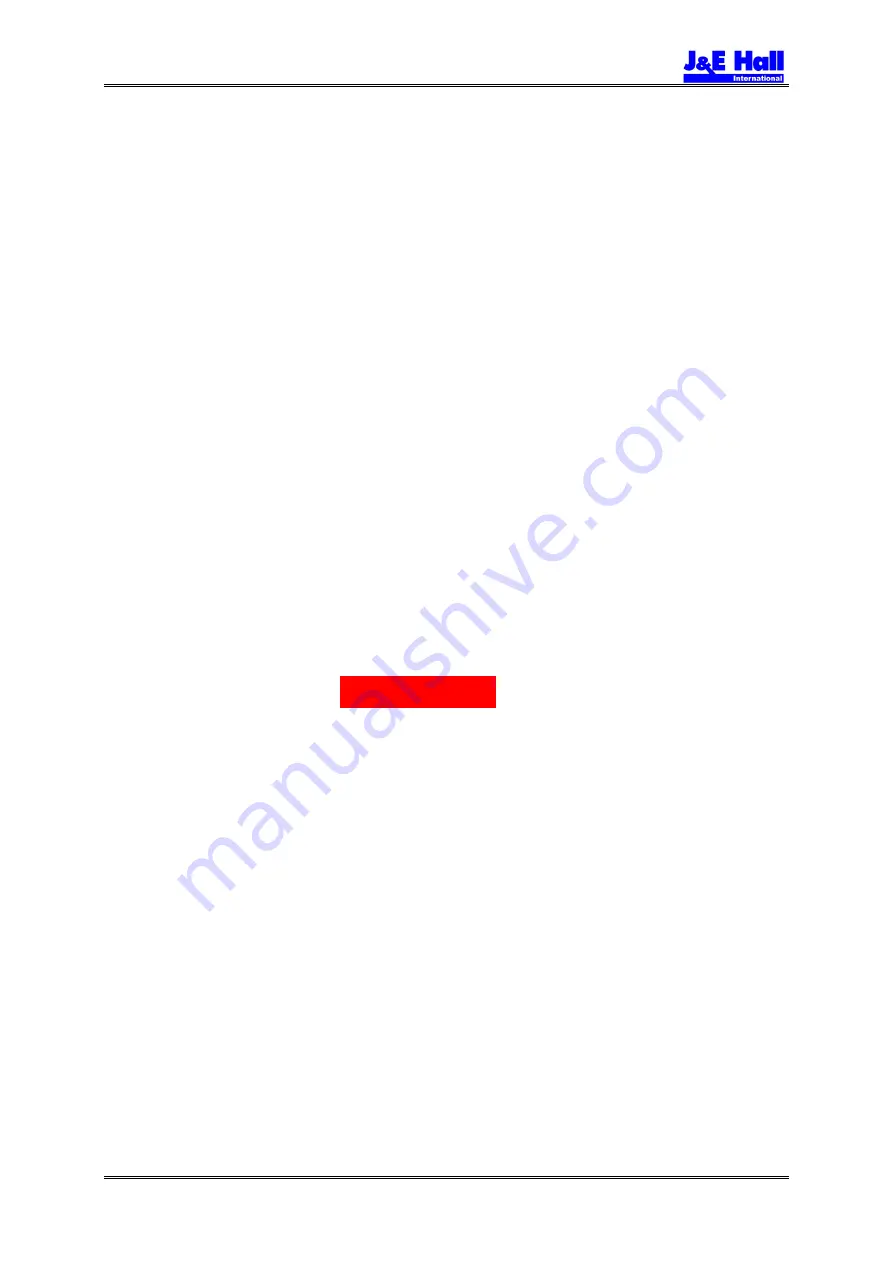
HSO 2024 to HSO 2035 Installation, Operation and Maintenance Manual
Issue 1.2 : 03/10
Publication 2-119
Page 45 of 94
(d)
Before running the compressor, the moving parts must receive
some initial lubrication.
•
Remove the blank plug(s) or flange(s) from the oil injection
connection(s), remove the blank plug from rear main bearing
oil connection. Inject oil to lubricate the mainshaft bearings,
main rotor flutes, star rotors and star rotor bearings.
•
Remove the blank plug from the gland housing and inject oil
to lubricate the gland seal assembly.
•
Remove the blank plugs from the capacity control cylinder
connections, these are positioned at the top of the casing
and are marked ‘Load’ and ‘Unload’. Use these connections
to fill the capacity control cylinder with oil.
It is important to be fairly generous with this initial lubrication, using
in all about 2 litres of oil. Use the same type and ISO grade of oil
as that used in the rest of the system.
(e)
Connect the oil injection lines, and the lube oil lines to the gland
and rear main bearings.
(f)
Connect the lines supplying oil from the capacity control solenoid
valves to the capacity control cylinder ‘Load’ and ‘Unload’
connections.
(g)
Connect the suction and discharge lines, and suction, discharge
and oil pressure gauge lines.
(h)
Rotate the mainshaft by hand to ensure that the motion-work turns
smoothly and evenly.
If the compressor proves very stiff to turn, turns unevenly, or
rotation is accompanied by any unusual noise, contact J & E Hall
International.
(i)
Connect the drive between the compressor and the prime mover.
If the drive coupling is supplied by J & E Hall International, refer to
publication 2-79 for drive installation and alignment details.
WARNING
The drive coupling MUST be protected by a suitable
FIXED coupling guard.
(j)
Make electrical wiring connections as described in 9.3.
(k)
Leak test and evacuate the system.
Leak testing and evacuation are described in the following
publications available from J & E Hall International:
•
Part D : Strength and Leak Testing.
•
Part E : Evacuation and Dehydration.
9.3.
Electrical Wiring Connections and Interlocks
The following electrical connections are required to the compressor:
•
Mains electrical supply to the compressor drive motor and
motor starter. Refer to the motor and starter manufacturer’s
instructions.
•
Electrical supply to the capacity control solenoid valves;
refer to Fig 3 and Fig 4.
If a 4-way solenoid valve is used; refer to publication 4-45 available
from J & E Hall International.
•
Electrical supply to the capacity control slide valve position
transducer; refer to 4.8. MSI Linear Variable Displacement
Transducer (MSI LVDT).
•
Electrical interlock to prevent the compressor starting unless
the slide valves are at minimum load; refer to 4.1.1.