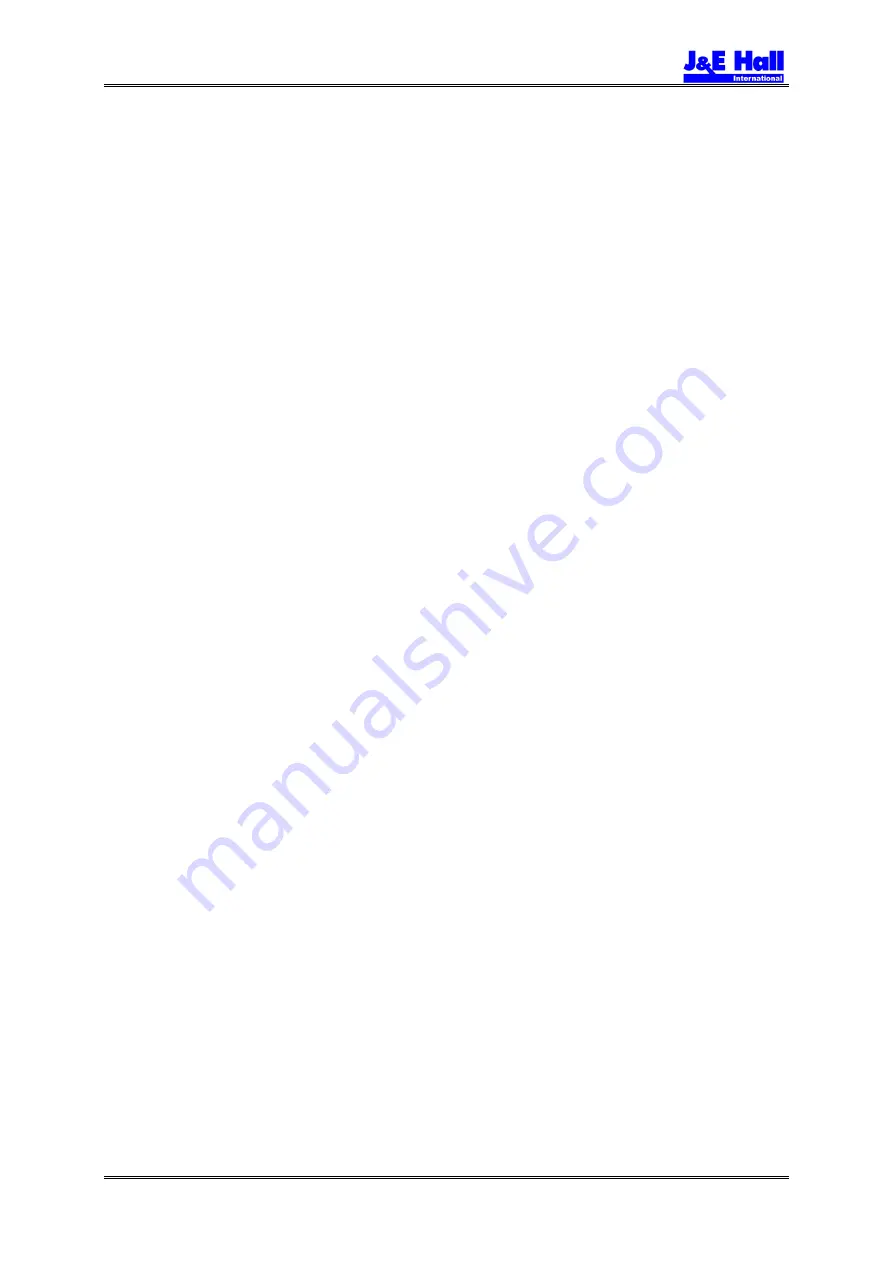
HSO 2024 to HSO 2035 Installation, Operation and Maintenance Manual
Issue 1.2 : 03/10
Publication 2-119
Page 47 of 94
(i)
Check that stop valves isolating pressure gauges, cut-outs or other
pressure controls are fully open. These valves should be locked-
open using circlips or equivalent locking devices.
10.3.
Compressor Drive Motor
The following general checks are applicable. Also refer to the motor
manufacturer’s instructions.
(a)
Check the supply voltage and comply with the motor
manufacturer’s data (usually stated on the motor data plate), and
any difference in voltage does not exceed 3 % between any two
lines. Since an imbalance produces a dramatic rise in the
temperature of the motor windings, it is important that any
imbalance is kept to a minimum.
Check and record the control supply voltage, this should be within
5 % of the design voltage.
NOTE: never attempt to run the compressor drive motor
with an electrical supply voltage, frequency or phase
rotation other than as designated on the motor electrical
data plate.
(b)
The compressor drive motor must
NOT
be started unless it is
completely dry. If a moisture indicator is fitted this can be checked
to ensure the motor is dry.
If the motor is fitted with anti-condensation heater(s), these must
be energised at least 24 hours before running the motor for the first
time.
If there is any doubt whether the motor has been affected by
moisture, the value of the motor insulation resistance must be
checked. The motor should not be run if the insulation resistance
exceeds the minimum specified by the motor manufacturer, refer to
the manufacturer’s instructions.
NOTE: the practice of running a motor having low
insulation resistance on full voltage is not
recommended. Insulation breakdown may occur before
the windings dry out.
(c)
Check that the motor cooling air intakes are not obstructed,
permitting free air flow with no recirculation. This is particularly
important if the motor is of the closed circuit, air-cooled type.
10.4.
Checking Compressor Rotation
(a)
The HallScrew compressor is a positive displacement machine
designed to rotate in one direction only, this is anticlockwise when
looking on the drive end of the compressor main shaft.
To prevent incorrect compressor rotation, it is
ESSENTIAL
to
check the rotation of the compressor drive motor with the coupling
disconnected.
The various safety controls can also be tested while the motor is
running.
(b)
Isolate the electrical supply to prevent the compressor accidentally
starting.
Remove the coupling guard. Disconnect the drive coupling by
removing the membrane/spacer unit.
Refit the coupling guard so that the rotation of the motor can be
safely observed.
(c)
Switch on the drive motor and check the direction of rotation.
When looking on the end of the motor drive shaft the shaft should
turn in a clockwise direction.