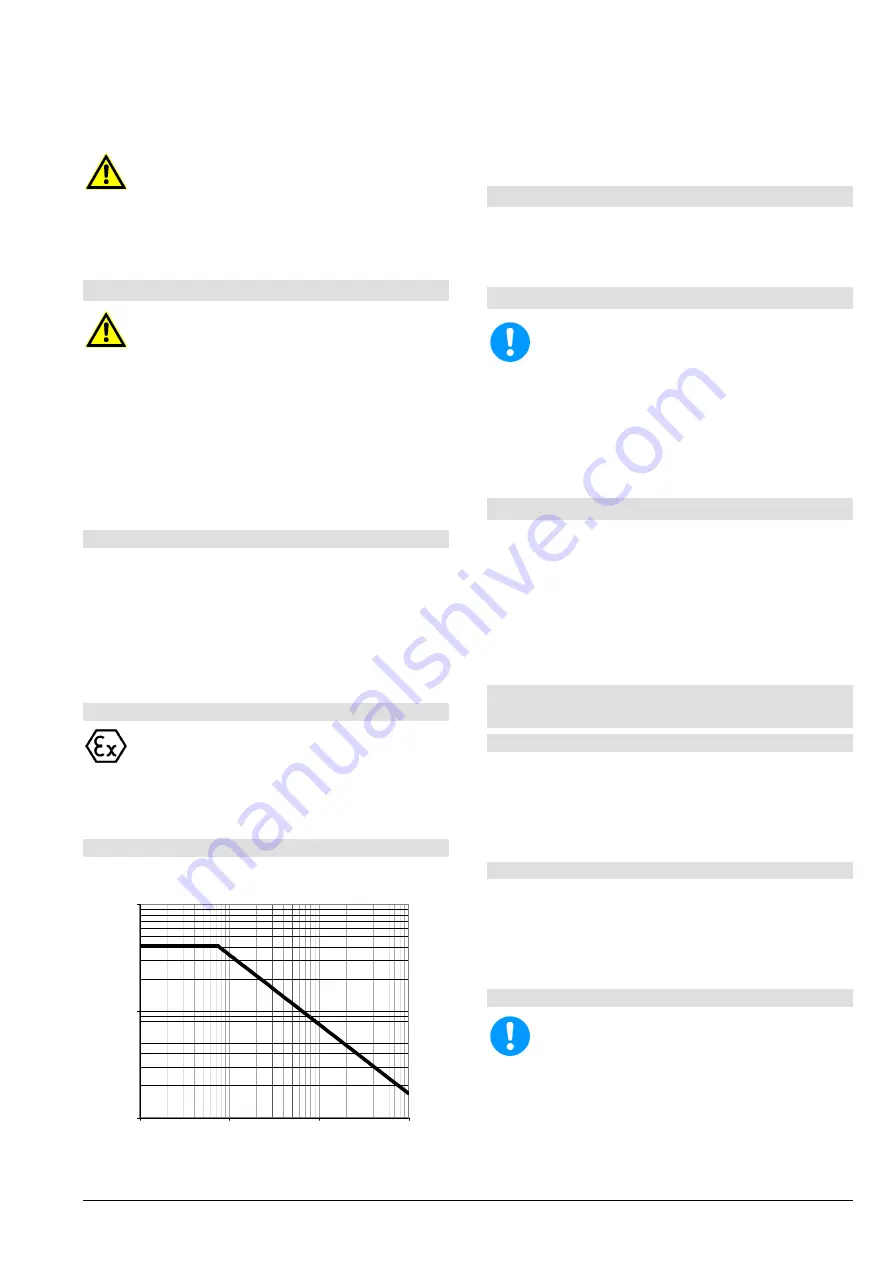
Installation, Operating and Maintenance Instruction
Model L, LN
LN 100-ger/fr/eng
Page 53
Revision 03
Artikel No. 771073301
Issue
01/2010
The pump should only be automatically restarted if it
has been made sure that the pump has remained
filled whilst stand by.
Be particularly careful not to touch hot machine
parts and when working in the unprotected shaft
seal area. Remember that automatically
controlled systems may switch themselves on
suddenly at any time. Suitable warning signs
should be affixed.
6.4 Limits of Operation
The operating limits of the pump / unit regarding
pressure, temperature, performance and speed
are shown in the data sheet and / or order
confirmation and must be observed under any
circumstances!
Do not exceed the output given on the motor
name plate.
Avoid
sudden
changes
in
temperature
(temperature shocks).
The pump and motor should run evenly and
without vibrations; check at least once a week.
6.4.1 Flow min. / max.
If no other data are given in the curves or data sheets,
the following is valid:
Q
min
= 0,1 x Q
BEP
for for short time operation
Q
min
= 0,3 x Q
BEP
for continuous operation
Q
max
= 1,2 x Q
BEP
for continuous operation *)
Q
BEP
= Flow in efficiency optimum
*) on condition that NPSH
facility
> (NPSH
pump
+ 0,5 m)
6.4.2 Abrasive Media
On pumping liquids with abrasive components
an increased wears at hydraulic and shaft
sealing must be expected. The intervals of
inspection should be reduced compared to the
usual times.
6.4.3 Permitted number of starts
The permitted number of starts of the pump must not
be exceeded, see diagram 6.
1,0
10,0
100,0
1
10
100
1000
Motor power [kW]
m
ax
. p
er
m
. s
ta
rt
s/
h
Diagram 6
With electric motors, the permitted number of starts is
given in the attached motor operating instructions.
If two different figures are given, the lower figure is
valid.
6.5 Grease lubrication
The pump is equipped with bearings greased for
lifetime. Regreasing of the bearings is neither possible
nor necessary.
6.6 Monitoring
Regular monitoring and maintenance will extend
the life of your pump or pump system
.
Pumps which are exposed to corrosive chemicals or
to wear through abrasion must be inspected
periodically for corrosion or wear and tear. The first
inspection should be carried out after six months. All
further inspection intervals should be determined on
the basis of the state of the pump.
6.7 Shutting down
Close the valve in discharge pipe right before
(max. 10 seconds) switching off the motor. This is
not necessary if there is a spring-loaded check
valve.
Switch off motor (make sure it runs down quietly).
Close the valve on suction side.
If there is any risk of freezing, empty pump,
cooling areas and pipes completely.
6.8 Storage / longer periods of non-
operation
6.8.1 Storage of new pumps
If the putting into operation shall happen a longer
period after the delivery, we recommend the following
measures for the storage of the pump:
Store pump at a dry place.
Rotate pump by hand at least once a month.
6.8.2 Measures for longer putting out of operation
Pump remains installed and in ready for operation:
Test runs of 5 min. duration must be made in
regular intervals. The span between the test runs
is depending on the plant. However, it should be
made once a week, at least.
6.8.3 Longer periods of non-operation
After long stationary periods, packing may have
hardened; these must be replaced before start-
up.
When starting up, follow the instructions for
starting up for the first time (see chapter 6)!
a) Filled pumps
Switch stand-by pumps on and immediately off
again once a week. Possibly use as main pump.
Replace bearings after 4 years.
Содержание L Series
Страница 69: ......