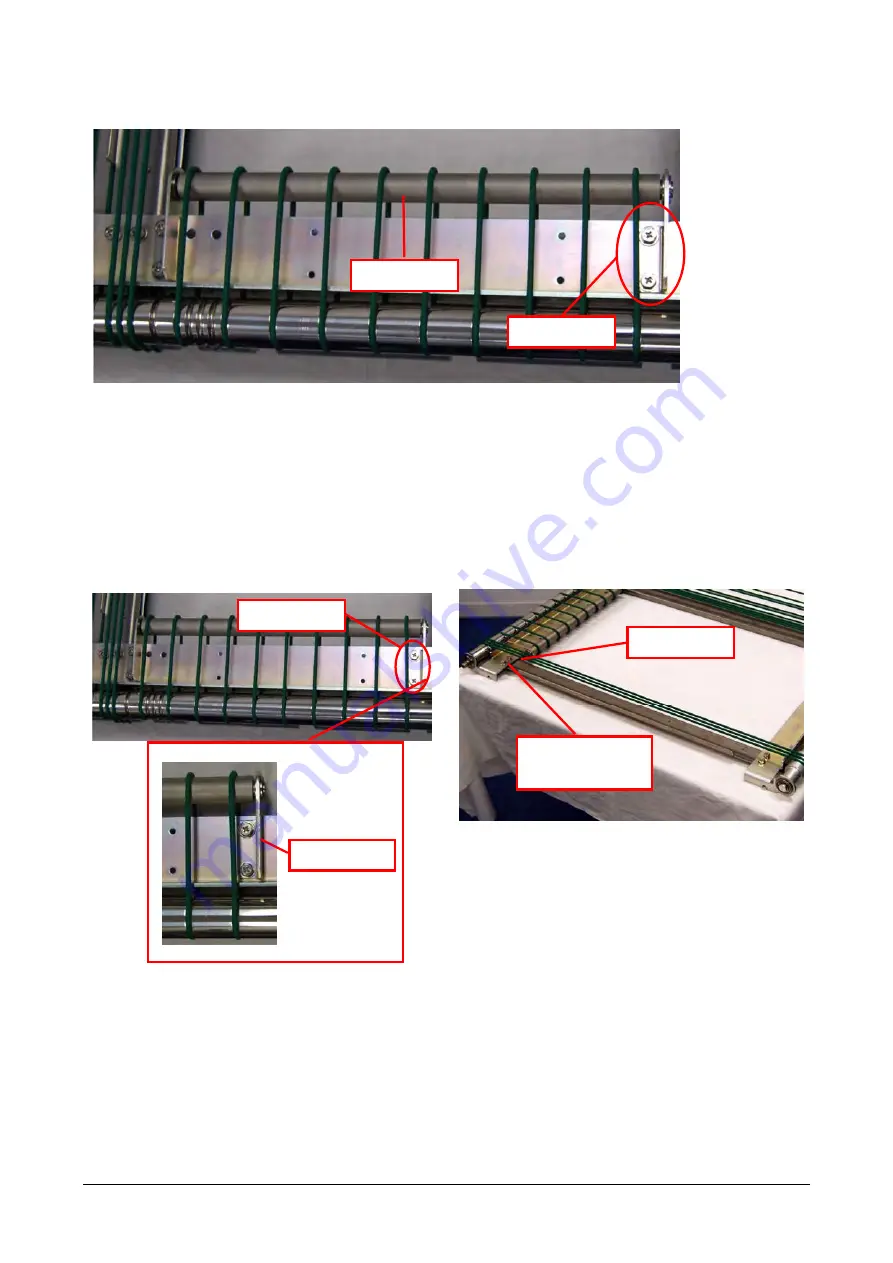
Chapter 3 Adjustment Mode
5
)
Remove screws (2) to remove one side of the roller of the short round belts.
6
)
Replace the short round belts.
Roller
Screws (2)
●
Assembly after replacing the short belts
Assembly procedure follows in the reverse direction of the procedure for dividing the unit into two. If
assembly is conducted with the unit lying flat, the film conveying unit may be deformed into a parallelogram
shape.
To prevent this from happening, follow the procedure described below.
1
)
Tighten the screws (2) on the removed side of
the roller.
Adjust the mounting position according to the
marker (line).
2
)
Temporarily tighten the screws (2) of the
removed rail.
Adjust the mounting position according to the
marker.
Marker (line)
Screws (2)
Screws (2), to be
temporarily
tightened
Marker
3-24
Содержание WM-NANO
Страница 6: ...Introduction 6 ...
Страница 10: ...Chapter 1 Overview 1 2 Part Names 1 2 1 Appearance 1 4 ...
Страница 11: ...Chapter 1 Overview 1 5 ...
Страница 64: ...Chapter 3 Adjustment Mode 10 Remove the cover by turning it from the bottom 3 11 ...