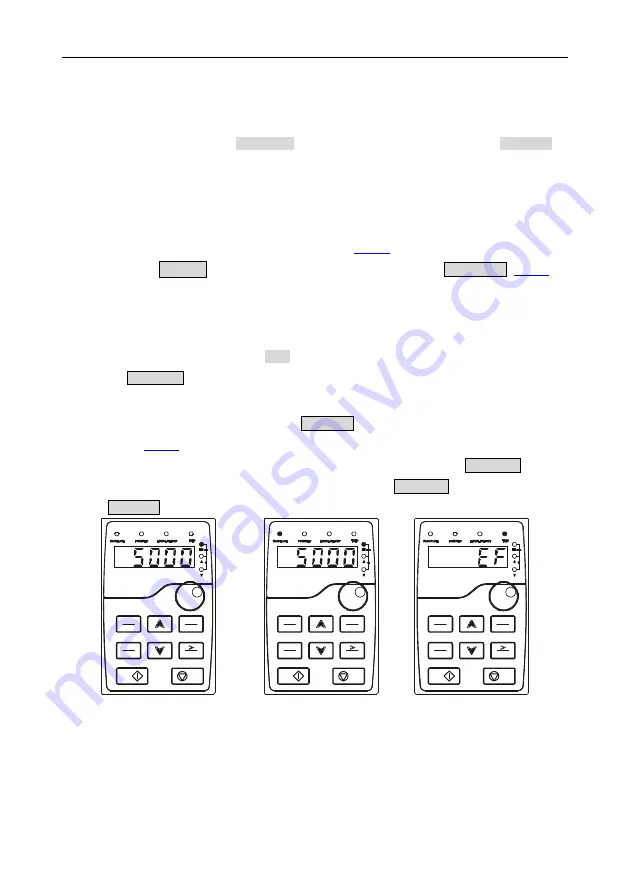
Goodrive300-LIFT series inverter
Keypad operation procedure
-31-
right to left.
5.3.2 Displayed state of running parameters
After receiving valid running commands, the inverter will enter the running state and the keypad will
display the running parameters. RUN/TUNE LED on the keypad is on, while the FWD/REV is
determined by the current running direction, as shown in Figure 5-2.
In the running state, there are 16 parameters that can be displayed. They are: running speed, set
speed, bus voltage, output voltage, output current, running frequency (Hz on), running rotation speed,
output power, output torque, input terminals state, output terminals state, AI1, AI2, torque
compensation, magnetic pole position, and linear speed.
determines whether to display the
parameters by bit.
》
/SHIFT can shift the parameters form left to right, while QUICK/JOG (
=2)
can shift the parameters from right to left.
5.3.3 Displayed state of fault
If the inverter detects the fault signal, it will enter the fault alarm displaying state. The keypad will
display the fault code by blinking. The TRIP LED on the keypad is on, and the fault reset can be
operated by STOP/RST on the keypad, control terminals or communication commands.
5.3.4 Displayed state of function codes editing
In the state of stopping, running or fault, press PRG/ESC to enter into the editing state (if there is a
password, see
).The editing state is displayed on two classes of menu, and the order is:
function code group/function code number→function code parameter, press
DATA/ENT into the
displayed state of function parameter. On this state, you can press DATA/ENT to save the parameters
or press PRG/ESC to exit.
PRG
ESC
DATA
ENT
SHIFT
RUN
STOP
RST
QUICK
JOG
PRG
ESC
DATA
ENT
SHIFT
RUN
STOP
RST
QUICK
JOG
PRG
ESC
DATA
ENT
SHIFT
RUN
STOP
RST
QUICK
JOG
Parameter displayed in the
stop state
Parameter displayed in the
running state
Faulty state displayed
Figure 5-2 Displayed state
5.4
Keypad operation
Operate the inverter via operation panel. See the detailed structure description of function codes in
the brief diagram of function codes.