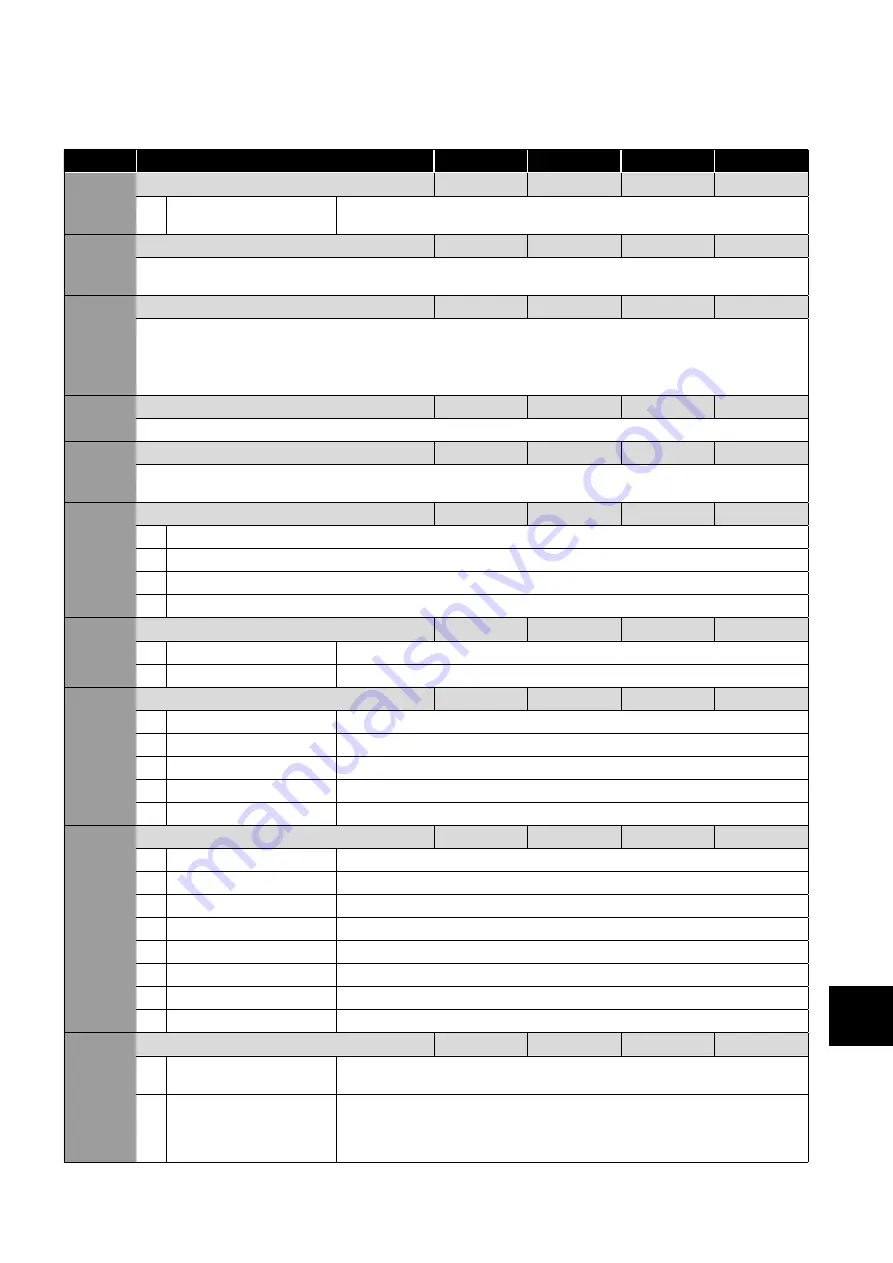
Version 1.10
| Optidrive ODP-2ETHEG-IN |
11
www.invertekdrives.com
Driv
e P
arameter Set
tings
5
5.2.2. Optidrive P2 / Optidrive Eco
The following parameters are used to configure the communication interface of the Optidrive E3. Refer to the drive user guide for
specific details of the functions of other parameters.
Par.
Description
Minimum
Maximum
Default
Units
P-12
Primary Command Source
0
9
0
-
4
Fieldbus Control
Control via Modbus RTU if no fieldbus interface option is present, otherwise control is from
the fieldbus option module interface.
P1-13
Digital Inputs Function Select
0
21
1
-
Defines the function of the digital inputs depending on the control mode setting in P1-12. See section 7.1. Environmental for more
information.
P1-14
Extended Menu Access Code
0
30000
0
-
Parameter Access Control. The following settings are applicable:
P1-14 = P2-40 = 101: Allows access to Extended Parameter Groups 0 – 5.
P1-14 = P6-30 = 201: Allows access to all parameter groups (Intended for experienced users only, usage is not described in this
User Guide).
P5-01
Drive Fieldbus Address
0
63
1
-
Sets the fieldbus address for the Optidrive.
P5-05
Communications Loss Timeout
0.0
5.0
2.0
Seconds
Sets the watchdog time period for the communications channel. If a valid telegram is not received by the Optidrive within this time
period, the drive will assume a loss of communications has occurred and react as selected below. Setting to zero disables the function.
P5-06
Communications Loss Action
0
3
0
-
0
Trip & Coast To Stop
1
Ramp to Stop Then Trip
2
Ramp to Stop Only (No Trip)
3
Run at Preset Speed 8
P5-07
Fieldbus Ramp Control
0
1
0
-
0
Disabled
Ramps are control from internal drive parameters P1-03 and P1-04.
1
Enabled
Ramps are controlled directly by the Fieldbus PDI4 Data Word.
P5-08
Fieldbus Process Data Output Word 4 Select
0
4
0
-
0
Output Torque
0 to 2000 = 0 to 200.0%.
1
Output Power
Output power in kW to two decimal places, e.g. 400 = 4.00kW.
2
Digital Input Status
Bit 0 indicates digital input 1 status, bit 1 indicates digital input 2 status etc.
3
Analog Input 2 Signal Level
0 to 1000 = 0 to 100.0%.
4
Drive Heatsink Temperature
0 to 100 = 0 to 100°C.
P5-12
Fieldbus Process Data Output Word 3 Select
0
7
0
-
0
Motor current
Output current to 1 decimal place, e.g. 100 = 10.0 Amps.
1
Power (x.xx kW)
Output power in kW to two decimal places, e.g. 400 = 4.00kW.
2
Digital input status
Bit 0 indicates digital input 1 status, bit 1 indicates digital input 2 status etc.
3
Analog Input 2 Signal Level
0 to 1000 = 0 to 100.0%.
4
Drive Heatsink Temperature
0 to 100 = 0 to 100°C.
5
User register 1
User Defined Register 1 Value.
6
User register 2
User Defined Register 1 Value.
7
P0-80 value
User Selected data value.
P5-13
Fieldbus Process Data Input Word 4 Select
0
1
0
-
0
Fieldbus Ramp Control
This option must be selected if the drive acceleration and deceleration ramps are to be
controlled from the fieldbus. P5-07 must also be set to 1 to enable this function.
1
User Register 4
The value received by the drive in PDI 4 is transferred to User Register 4. This option allows
the function of the process data word to be defined in Parameter Group 9. In this case, User
Register 4 should not be written to within any PLC function code, although the value can be
read.