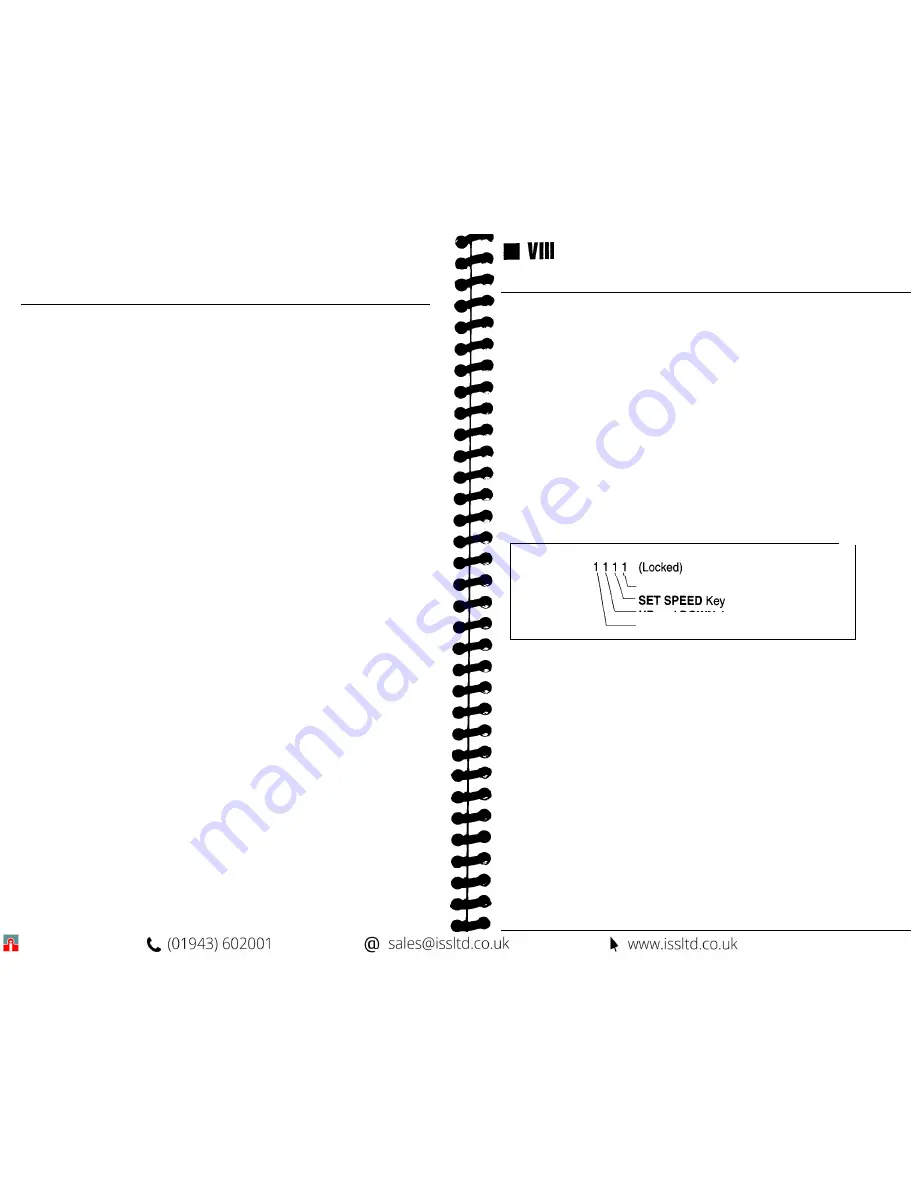
VII.
PROGRAMMING
l
JOG MODE
When the Jog function is initiated and held, the MicroSpeed 196 will accelerate to
the speed programmed in Variable 06. Variable 29 enables you to follow the accel/
decel times (Variables 07 and 08) or to bypass the ramp times.
Variable 06
-
Jog Speed in User Units
-
Enter the desired jog speed in user units,
then press ENTER.
Variable 29 - Jog Ramp Selection - This variable allows the operator to select the
following jog ramp profiles:
0000 = No Ramp Time
0001 = Ramp on Decel
0010 = Ramp on Accel
0011 = Ramp on Accel and Decel
PROGRAMMING
l
OPERATIONAL VARIABLES
Variable 07 - Acceleration Time
-
When the acceleration time is accessed, the alpha-
numeric display will read AcelTime. Enter the time in seconds desired for acceleration
from 0V (motor stop) to maximum output. The smallest unit of time is l/10 second.
Variable 06 - Deceleration Time
-
When the deceleration time is accessed, the alpha-
numeric display will read DcelTime. Enter the time in seconds for deceleration from
maximum output to 0V (motor stop). The smallest unit of time is l/10 second,
Variable 11 - Keypad Lockout
-
When Variable 11 is accessed, the alpha-numeric
display will read Key Lock. Each zero represents a different section of the keypad that
can be independently “locked.” The section of the keypad that is locked is determined by
placing a 1 (one) in the appropriate location. Any section or combination of sections can
be locked. (See chart below for lockout positions and descriptions.) After all program-
ming and tuning is complete, activate the lock out by installing a jumper on TB1-12 to
TBl-11.
Note: It is recommended that you “lock out” your variables, so that the MicroSpeed 196
cannot be inadvertently reprogrammed.
Positions: 0 0 0 0 (Unlocked)
VAR key and 2nd Func Key
Up and Down Arrows
Run, stop and jog Keys
DISPLAY:
Variable 21 - Display Selection -
This Variable allows the user to select the
information that will be displayed on the Numeric display. Mode 0000 is commonly used
in normal operation, while modes 0001 through 0007 are typically used during setup or
troubleshooting only. When Variable 21 is selected, the alphanumeric display will read
Display#.
To
select the numeric display mode during operation, enter a number from the
following list:
0000 =
Tachometer in User Units
0001
= Feedback Frequency in Hertz or Kilohertz
0002
= Lead Frequency in Hertz or Kilohertz (Follower)
0003
= Auxiliary Frequency in Hertz (Auxiliary Mode)
0004
= Follower Error in Number of Pulses
0005
= Total Output in DAC Bits (0 to 4094)
0006
= Output Error in DAC Bits (-999 to 4094)
0007
= Alarms (a “1” Indicates the Alarm Is Active)
1000
= Zero Speed
0100
= High Alarm
0010
= Low Alarm
0001
= Deviation Alarm
Содержание MicroSpeed 196
Страница 1: ...MSMAN32C MicroSpeed 196...
Страница 19: ......