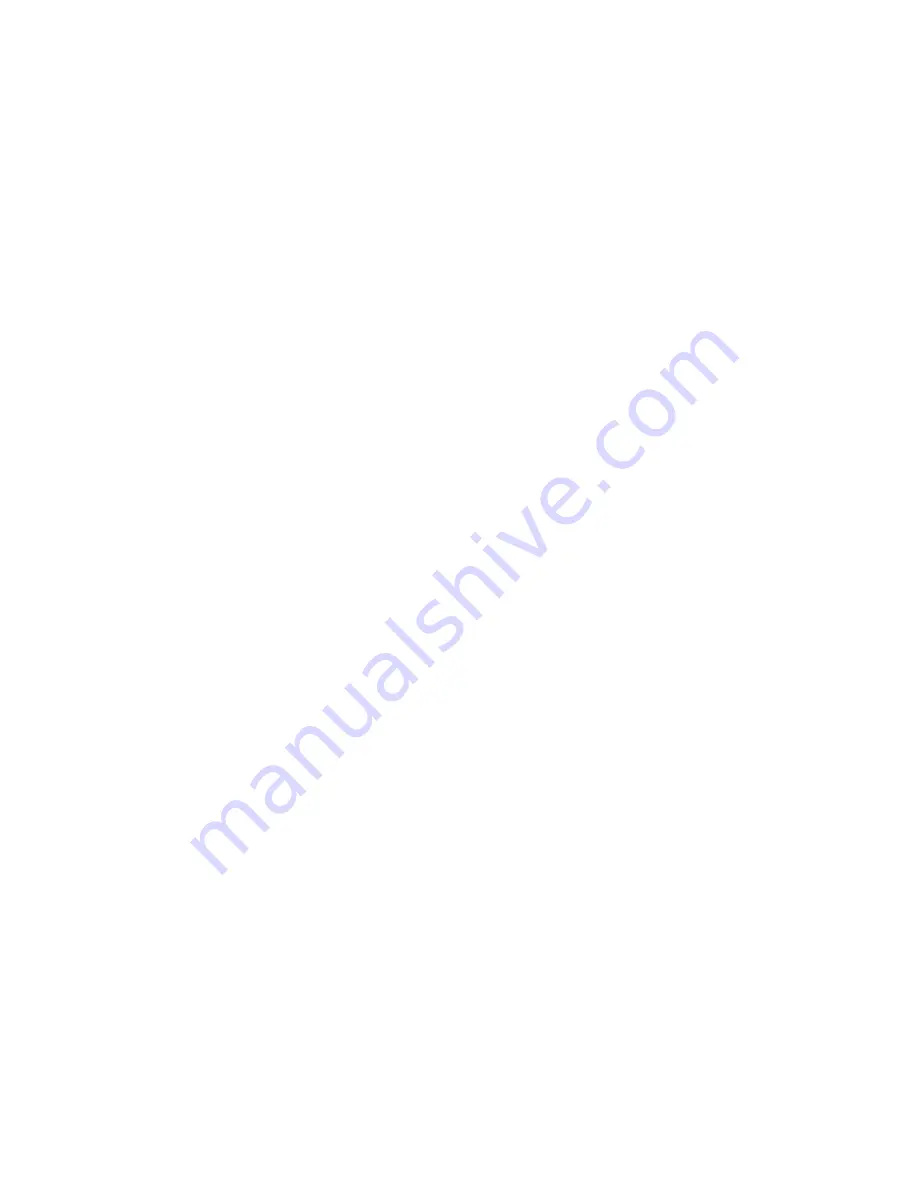
3
Note: When testing the insulating resistance with Mega-Ohm-Meter (use DC 500V
Mega-Ohm-Meter), disconnect the main circuit from the inverter. Connect all the terminals of the
main circuit in short circuit, and then test the insulation between the main circuit and the
earth/control loop.
3. Storage of inverter
After buying the inverter, the user must pay attention to the following points for temporary/long-term
storage of inverter:
1) It is recommended to store the inverter in its original packing box. The storage temperature shall
be between -20ºC and +60ºC, with the humidity not more than 95%RH.
2) Long-term storage will cause deterioration of electrolytic capacitor. Therefore, inverters long time
not in service must be powered once within 2 years for 5 hours; and the input voltage must be
boosted gradually with voltage regulator to the rated value.