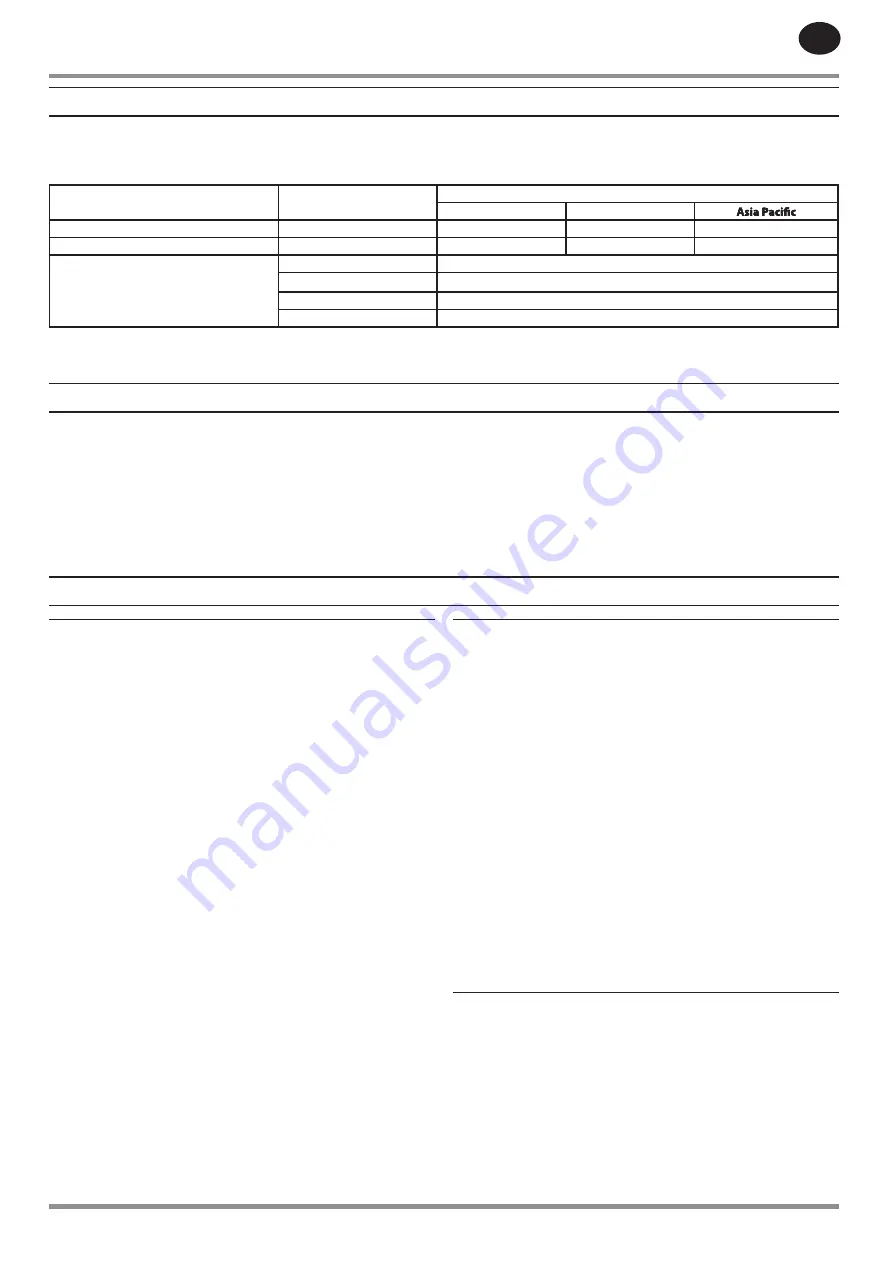
EN-
80446339
Rev B
EN
SAFETY
Locate, read, understand and follow all Danger, Warning, Caution, and
Operating Instructions on the product and in all Manuals. Failure to
comply with safety precautions described in the manuals supplied with
the product, this manual or any of the labels and tags attached to the
product may result in death, serious injury or property damage.
Check that all labels, tags and data (name) plates are in place and legible.
It is your responsibility to make this information available to others.
If you have any questions about safety or procedures not included in
•
•
•
•
this manual, ask your supervisor or contact any
Ingersoll Rand
office or
qualified
Ingersoll Rand
distributor.
RECEIPT / HANDLING
Receipt
Before signing the delivery receipt, inspect for damage and missing parts. If
damage or missing parts are apparent, make the appropriate notation on the
delivery receipt, then sign the receipt. Immediately contact the carrier for an
inspection.
All material shall be held in the receiving location for the carrier’s inspection.
Delivery receipts that have been signed without a notation of damage or
missing parts are considered to be delivered “clear.” Subsequent claims are
then considered to be concealed damage claims. Settle damage claims
directly with the transportation company.
If you discover damage after receiving the compressor (concealed damage),
the carrier shall be notified within 15 days of receipt and an inspection shall
be requested by telephone with confirmation in writing. On concealed
damage claims, the burden of establishing that the compressor was
damaged in transit reverts back to the claimant.
Read the compressor nameplate to verify it is the model ordered, and read
the motor nameplate to verify it is compatible with your electrical conditions.
Make sure electrical enclosures and components are appropriate for the
installation environment.
Unpacking and Handling
The compressor will normally be delivered with a polyethylene or other
cover. If a knife has to be used to remove this cover, ensure that the exterior
paintwork of the compressor is not damaged.
Incorporated within the base of the compressor are slots to enable a fork lift
truck to move the compressor. Ensure truck forks are fully engaged on both
sides. Alternatively a special lifting frame can be used to enable a crane or
hoist to move the compressor. Use only marked lifting points.
Once the packaging and pallet are discarded and the compressor is in its
final position, remove the yellow painted transit brackets from the resilient
mounts and store for future use or discard.
For Variable Speed Drive (VSD)
() brackets at the separator tank
(1) bracket from the air end discharge elbow.
(1) bracket from the air end support.
For Fixed Speed (FS)
() brackets at the separator tank
(1) bracket from the air end support.
(1) bracket from the motor mounting bracket.
Long Term Storage
If the product will not be commissioned within six months of receipt, it
should be prepared for long term storage. Please contact
Ingersoll Rand
for
details.
•
•
•
•
•
•
ABOUT THIS MANUAL
The purpose of this manual is to provide site planning, installation and operation guidelines for the compressor.
For supporting documentation refer to Table 1.
Table 1: Product Manuals
Publication
Publication
Publication
Publication
Product
Product
Product
Product
Product
Part/Document Number by Region
Part/Document Number by Region
Part/Document Number by Region
Part/Document Number by Region
Part/Document Number by Region
Part/Document Number by Region
Part/Document Number by Region
Americas
Americas
Americas
EMEA *
Product Safety Information Manual
Product Safety Information Manual
Product Safety Information Manual
Product Safety Information Manual
Product Safety Information Manual
Product Safety Information Manual
Product Safety Information Manual
Product Safety Information Manual
Product Safety Information Manual
Product Safety Information Manual
Product Safety Information Manual
Product Safety Information Manual
All
All
80446313
80446156
80446321
Product Maintenance Manual
Product Maintenance Manual
Product Maintenance Manual
Product Maintenance Manual
Product Maintenance Manual
Product Maintenance Manual
Product Maintenance Manual
All
All
80446354
80446248
80446362
Product Parts Information Manual
R55-75 kW
R37-45 kW
80446271
80448095
R132-160 kW Single-Stage
2-160 kW Single-Stage
2-160 kW Single-Stage
80446057
R90-160 kW Two-Stage
R90-160 kW Two-Stage
R90-160 kW Two-Stage
R90-160 kW Two-Stage
R90-160 kW Two-Stage
R90-160 kW Two-Stage
80446065
* Europe, Middle East and Africa
Product specification sheets and reference drawings are also available.
110812.16.23
Содержание R132
Страница 45: ...110812 16 23...
Страница 46: ...110812 16 23...
Страница 48: ...ingersollrandproducts com 2012 Ingersoll Rand plc 110812 16 23...