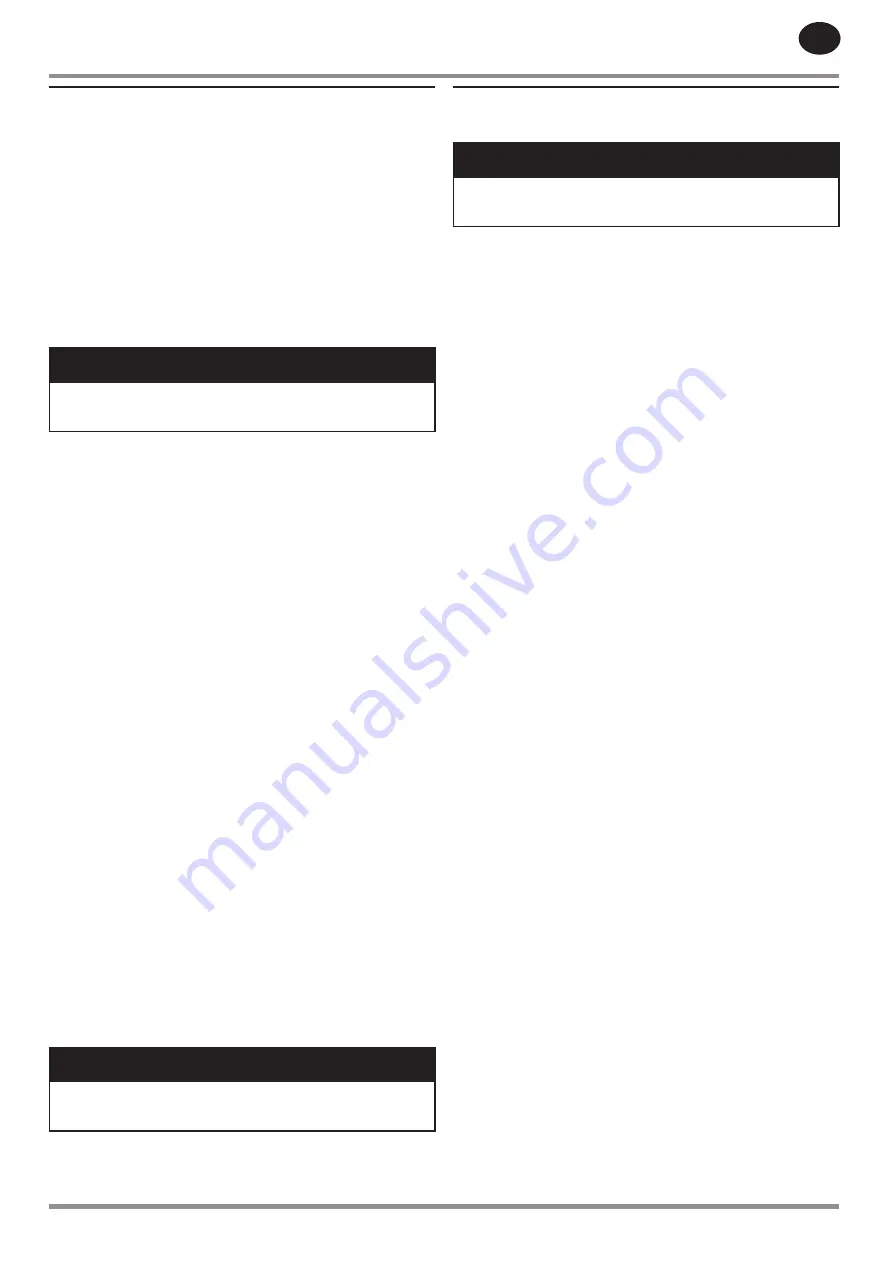
EN-5
80446339
Rev B
EN
Electrical
A qualified electrician shall perform all electrical installations and service.
The compressor shall be properly grounded / earthed in compliance with all
applicable standards and regulations (local, state, country, federal, etc.).
Installation of this compressor shall be in compliance with all applicable
standards and regulations (local, state, country, federal, etc.).
The compressor shall have its own isolator situated adjacent to it. The fuse
protecting the circuit and the compressor shall be selected in accordance
with recognized code requirements on the basis of the data provided in the
specification sheet.
Feeder cables shall be sized to ensure that the circuit is balanced and not
overloaded by other electrical equipment. The length of wiring from a
suitable electrical feed point is critical as voltage drops may impair the
performance of the compressor.
NOTICE
For VSD, cable sizes may vary considerably so the line reactor is
equipped with copper bus connections . These connections can accept
bolts between 6 mm and 12 mm .
Feeder cable connections to incoming terminals L1-L2-L shall be tight and
clean.
The applied voltage shall be compatible with the compressor data plate
ratings.
The control circuit transformer has different voltage tappings. Ensure that
these are set for the specific applied voltage prior to starting.
Remove the blind plate to cut a hole for incoming power connection. If it
is necessary to make a hole in the control box in a different location, care
should be taken to not allow metal shavings to enter the starter and other
electrical components within the box. If another hole is used, the original
hole shall be blocked off.
The feeder cable shall be suitably glanded in to the starter box to maintain
proper ingress protection. Fixed speed starter boxes are rated for NEMA 4
/IP65, and variable speed drive starter boxes are rated for NEMA12/IP54.
For variable speed drive starter boxes, the feeder cable shall be glanded to
ensure that dirty air does not by-pass the filters.
On completion of electrical installation, check that the blower or fan motor
rotation is correct.
Variable speed drive compressors are designed for use, where the electricity
supply is separated from nearby residential and commercial areas. If the
compressor is to be used in a light industrial, residential or commercial
environment where the local supply network is shared, further radio
frequency (RF) screening measures may be required. Consult your local
distributor/supplier for details of the optional RF filter.
Variable speed drive compressors have an anti-condensation heater
and thermostat in the electrical box. This circuit can be connected to
an independent electrical supply of either 110 V or 20 V single phase,
dependent on the country of installation. The supply shall be suitably fused
and an independent isolator installed adjacent to the compressor. Verify that
the thermostat is adjusted to 29˚ C (85˚ F). This shall be done in accordance
with recognized codes. It is good practice, and sometimes mandatory,
to display suitable signs warning that the compressor has two separate
electrical supplies which both shall be isolated before any work is attempted.
For Variable speed drive compressors, the heater circuit can also be supplied
from the 110 V tapping of the control transformer and connected as shown
on the schematic wiring diagram furnished separately from this manual.
NOTICE
Main and fan motor insulation shall be tested by a qualified electrician
prior to initial start-up or following an extended shutdown period in
cold and damp conditions .
Watercooled
Cooling Water Piping
NOTICE
Water piping to and from the compressor package shall be at least
as large as the package connection size . Do not undersize the water
piping .
Isolation valves with side drains should be installed on both the inlet and
outlet lines. To maintain cooler cleanliness and reliability, it is important to
install a strainer of 2 mm mesh size on the inlet line. Strainers are available
from
Ingersoll Rand
.
For sea water applications (sea water option only) a zinc anode is not
recommended as it will deteriorate the copper oxide film on the 70/0
copper-nickel alloy tubes in contact with sea water. To minimize galvanic
corrosion and provide the greatest corrosion protection to the coolers, it
is strongly recommended that a section of iron pipe (>00 mm length) be
connected as close as possible to the air compressor package water inlet
connection. The iron pipe will act as the sacrificial anode for the copper-
nickel tubes and therefore shall be considered a regular maintenance and
replacement item. For this reason, the section of iron pipe should be installed
so that it can be easily replaced (e.g. with a union joint.).
The air compressor has a normally closed solenoid valve that is fitted to
the water outlet side within the package. The valve is wired into the air
compressor control circuit and closes when the compressor stops.
Carefully inspect the water system before installing the air compressor
package. Ensure that the piping is free of scale and deposits that may
restrict water flow to the air compressor package. If water cleanliness is poor,
filtration installed on the water inlet pipe line is recommended.
Proper operation of the compressor requires that the cooling water flow
be provided at a maximum supply temperature of 46° C (115° F). See the
compressor engineering data sheets for cooling water flow rates.
Water temperature and pressure gauges should be installed in the water
piping for use in any fault finding of the water system. Water pressure should
ideally be between and 5 bar (4.5 and 72.5 psi) but shall not be above 10
bar (145 psi).
Water cleanliness is also extremely important. Cleaning of coolers as a result
of fouling is a customer responsibility. Therefore, it is highly recommended
that proper water quality shall meet the requirements listed in WATER
QUALITY RECOMMENDATIONS later in this section.
Venting the water system
Air should be vented from the water side of the system to avoid poor
performance and water hammer. Since the air compressor uses different
type heat exchangers depending on your selection of “fresh water cooled”
or “harsh water cooled” system, the venting procedure is different. Be sure to
use the correct procedure below.
Fresh water coolers (brazed plate heat exchangers):
1. Disconnect the water stop valve in the water outlet line of the
compressor.
2. Open the inlet water valve(s) to allow the water to flow to the
compressor.
. Allow all the air to escape from the system and observe water at the
water outlet port.
4. Connect the water stop valve.
Harsh water coolers (shell and tube heat exchangers):
1. Locate the water system vent cocks on top of the aftercooler and oil
cooler.
2. Open the water valve(s) allowing water to flow to the package.
. Open the vent cocks and allow all air to escape from the system.
When water is observed at the vent cocks, close them.
110812.16.23
Содержание R132
Страница 45: ...110812 16 23...
Страница 46: ...110812 16 23...
Страница 48: ...ingersollrandproducts com 2012 Ingersoll Rand plc 110812 16 23...