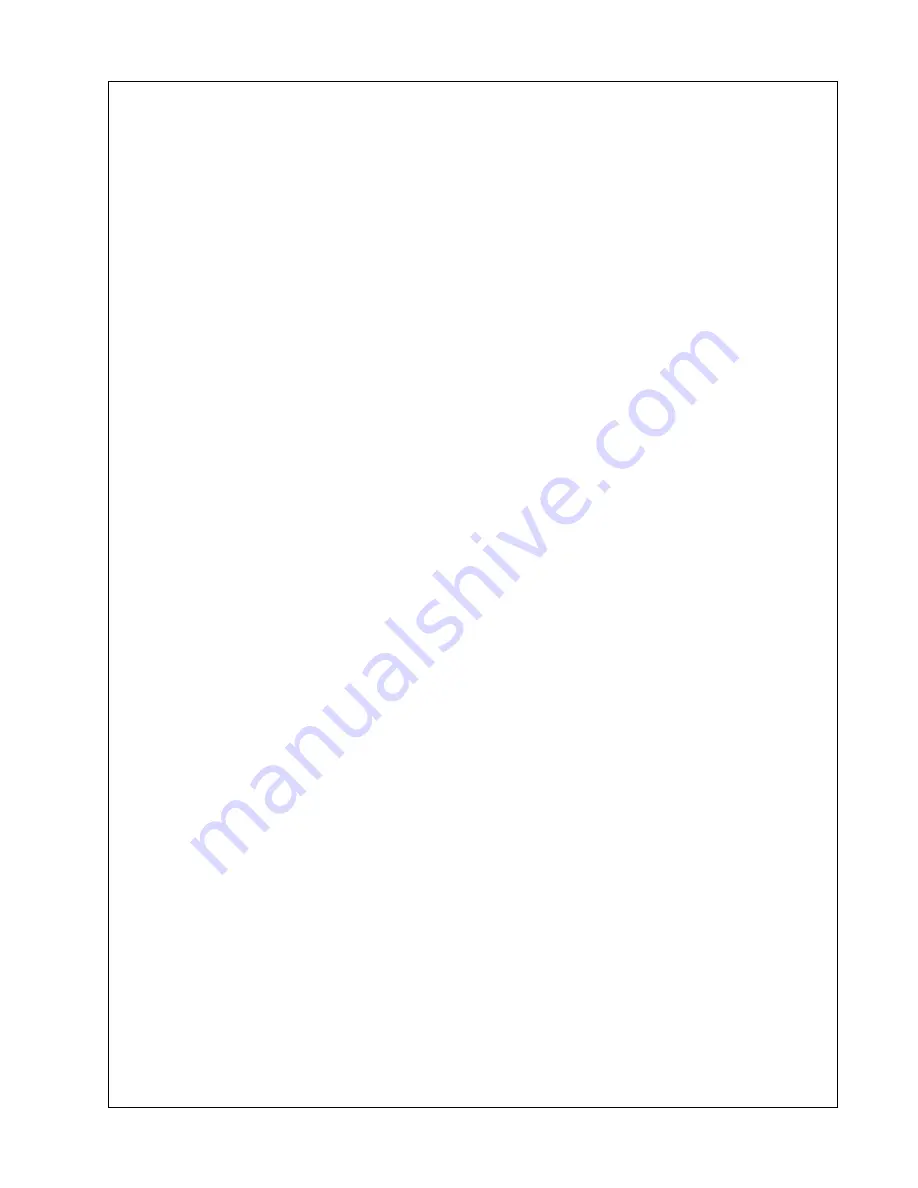
Safety
Operating & Maintenance Manual
13
ends of one booster cable to the positive (+)
terminal of each battery. Connect one end of
other cable to the negative (-) terminal of the
booster battery and other end to a ground
connection away from dead battery (to avoid
a spark occurring near any explosive gases
that may be present). After starting unit,
always disconnect cables in reverse order.
High Pressure Air can cause serious injury or
death. Relieve pressure before removing
filler plugs/caps, fittings or covers.
Air pressure can remain trapped in air supply
line which can result in serious injury or
death. Always carefully vent air supply line at
tool or vent valve before performing any
service.
This machine produces loud noise with doors
open or service valve vented. Extended
exposure to loud noise can cause hearing
loss. Always wear hearing protection when
doors are open or service valve is vented.
Never inspect or service unit without first
disconnecting battery cable(s) to prevent
accidental starting.
Do not remove the pressure cap from a HOT
radiator. Allow radiator to cool down before
removing pressure cap.
Do not use petroleum products (solvents or
fuels) under high pressure as this can
penetrate the skin and result in serious
illness.
Wear eye protection while cleaning unit with
compressed air to prevent debris from
injuring eye(s).
Disconnected air hoses whip and can cause
serious injury or death. Always attach a
safety flow restrictor to each hose at the
source of supply or branch line in accordance
with OSHA Regulation 29CFR Section
1926.302(b).
Rotating fan blade can cause serious injury.
Do not operate without guard in place.
Use care to avoid contacting hot surfaces
(engine exhaust manifold and piping, air
receiver and air discharge piping, etc.).
Ether is an extremely volatile, highly
flammable gas. USE SPARINGLY! DO NOT
use ETHER if unit has GLOW Plug starting
aid. Engine damage will result.
Never allow the unit to sit stopped with the
pressure in receiver-separator system. As a
precaution, open manual blowdown valve.
Never operate unit with guards, covers or
screens removed. Keep hands, hair,
clothing, tools, blow gun tips, etc. well away
from moving parts.
Make sure wheels, tires and tow bar
connectors are in safe operating condition
and tow bar is properly connected before
towing.
Whenever the machine is stopped, air will
flow back into the compressor system from
devices or systems downstream of the
machine unless the service valve is closed.
Install a check valve at the machine service
valve to prevent reverse flow in the event of
an unexpected shutdown when the service
valve is open. Stop machine to add fuel.
Hazardous Substance Precaution
The following substances are used in the
manufacture of this machine and may be
hazardous to health if used incorrectly.
Avoid ingestion, skin contact and breathing
fumes for the following substances:
Antifreeze, Compressor Oil, Engine
Lubricating Oil, Preservative Grease, Rust
Preventative, Diesel Fuel and Battery
Electrolyte.
:
Содержание P185AWIR
Страница 6: ...1 4...
Страница 7: ...3 FOREWORD...
Страница 8: ...4...
Страница 10: ...6...
Страница 11: ...7 DRAWBAR NOTICE...
Страница 12: ...Operating Maintenance Manual 8...
Страница 14: ...Operating Maintenance Manual 10...
Страница 15: ...11 Section 1 Safety...
Страница 19: ...Safety Operating Maintenance Manual 15...
Страница 20: ...Operating Maintenance Manual Safety 16...
Страница 22: ...Operating Maintenance Manual Safety 18...
Страница 23: ...Safety Operating Maintenance Manual 19...
Страница 25: ...21 Section 2 WARRANTY...
Страница 30: ...Operating Maintenance Manual WARRANTY 26...
Страница 32: ...Operating Maintenance Manual WARRANTY 28...
Страница 33: ...29 Section 3 NOISE EMISSION...
Страница 39: ...35 Section 4 GENERAL DATA...
Страница 42: ...Operating Maintenance Manual GENERAL DATA 38...
Страница 43: ...39 SECTION 5 OPERATION...
Страница 51: ...47 Section 6 MAINTENANCE...
Страница 59: ...55 Section 7 LUBRICATION...
Страница 61: ...57 Section 8 Trouble Shooting...
Страница 69: ...65 Section 9 4IRI8N 4IRI8T ENGINE...