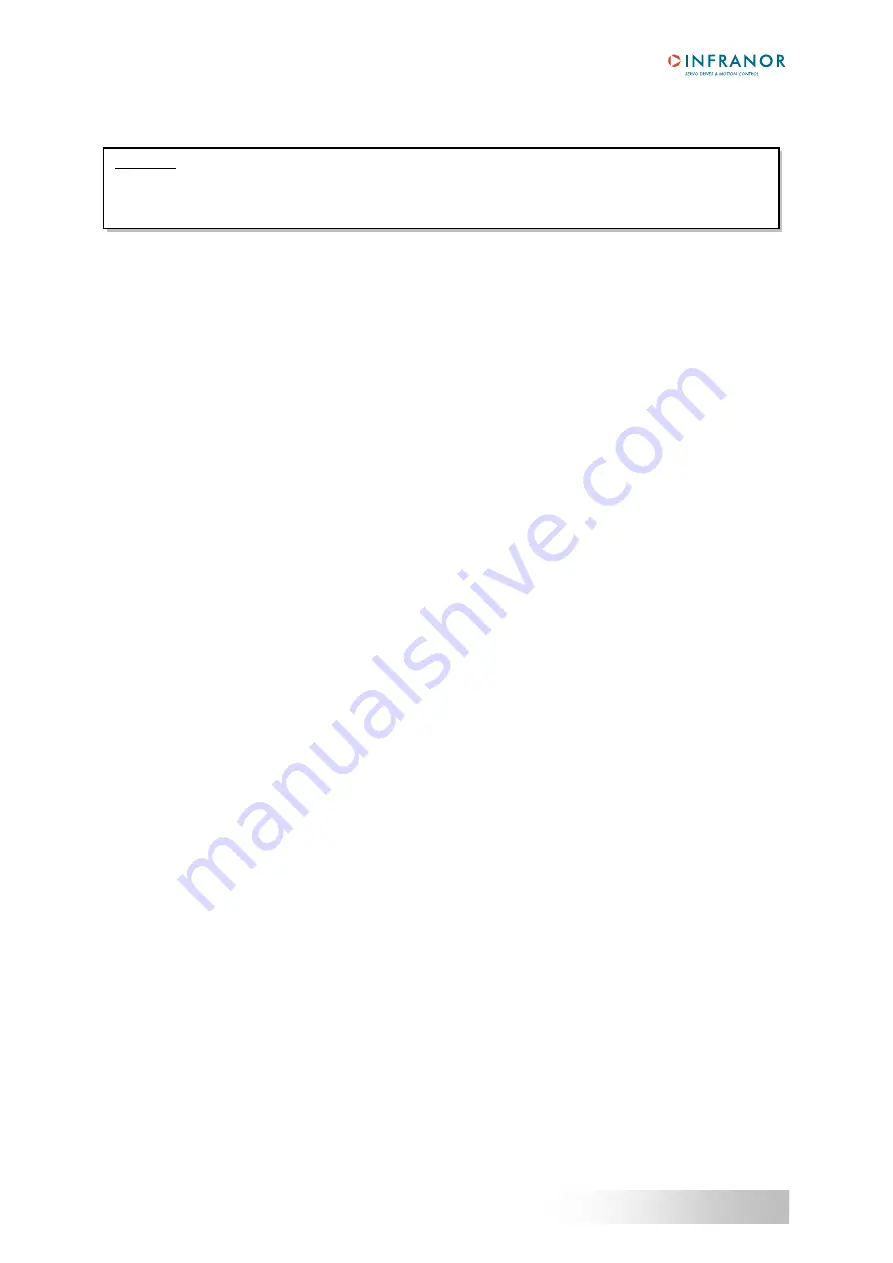
32
CHAPTER 6 – Commissioning
SMT-BD1/t
5.6 - PID loop adjustment for tension control
The PID loop parameters are at first initialised according to the following values :
Error scaling gain
is set at 10 %.
Proportional gain
is set at 1.
Integral gain
and
Derivative gain
are both set at 0.
Speed variation limit
parameter is set at a low value (100 rpm).
The tension control parameters are at first initialised according to the following values :
Tension error tolerance
is set at 10 %.
Overspeed limit
is set at the
Maximum motor speed
value.
Tension sequence error link
is not defined in order to get the motor stopped in case of tension sequence error.
If possible, the
Undertension limit
parameter value is set out off the voltage range given by the dancer or the
load cell (according to the previous tension measurement sensor calibration). This avoids the tension sequence
error to be released during the PID adjustment.
A tension control sequence is programmed according to following conditions:
Tension set point
is set according to the previous tension measurement sensor calibration.
Holding time
parameter value is set at more than 16000 ms in order to have the sequence active until the STOP
input activation.
Engage the material in the unwinder/rewinder and lock it by means of the downstream traction system.
The TDI input must be disabled in order to enable the PID loop for the tension regulation.
Start the tension control sequence execution.
If the tension loop is instable (continuous material unwinding or saturated motor torque), reverse the sign of the
error scaling gain
parameter.
If the tension loop is oscillating, reduce the value of the
Proportional gain
until the loop remains stable. When
the system is stable, increase the
Proportional gain
parameter up to the value where it starts oscillating; then
reduce the parameter
Proportional gain
in order to ensure the tension stability.
Increase progressively the parameters
Derivative gain
and
Integral gain
in order to optimise the tension loop
response in case of a disturbance by manual jerking of the spool or of the material.
In case of loud noise in the motor due to the tension measurement signal, reduce the
Tension input filter
cut-off
frequency value.
Adjust the parameter
Speed variation limit
according to the speed offset command value that is necessary for
regulating the material tension over the whole speed range (generally 5 to 10 % of the maximum motor speed
value).
CAUTION
It is advisable to limit the motor torque by limiting the amplifier
Max. current
and
Rated current
during the
PID adjustment phase in order to avoid a material braking if the tension loop becomes instable.