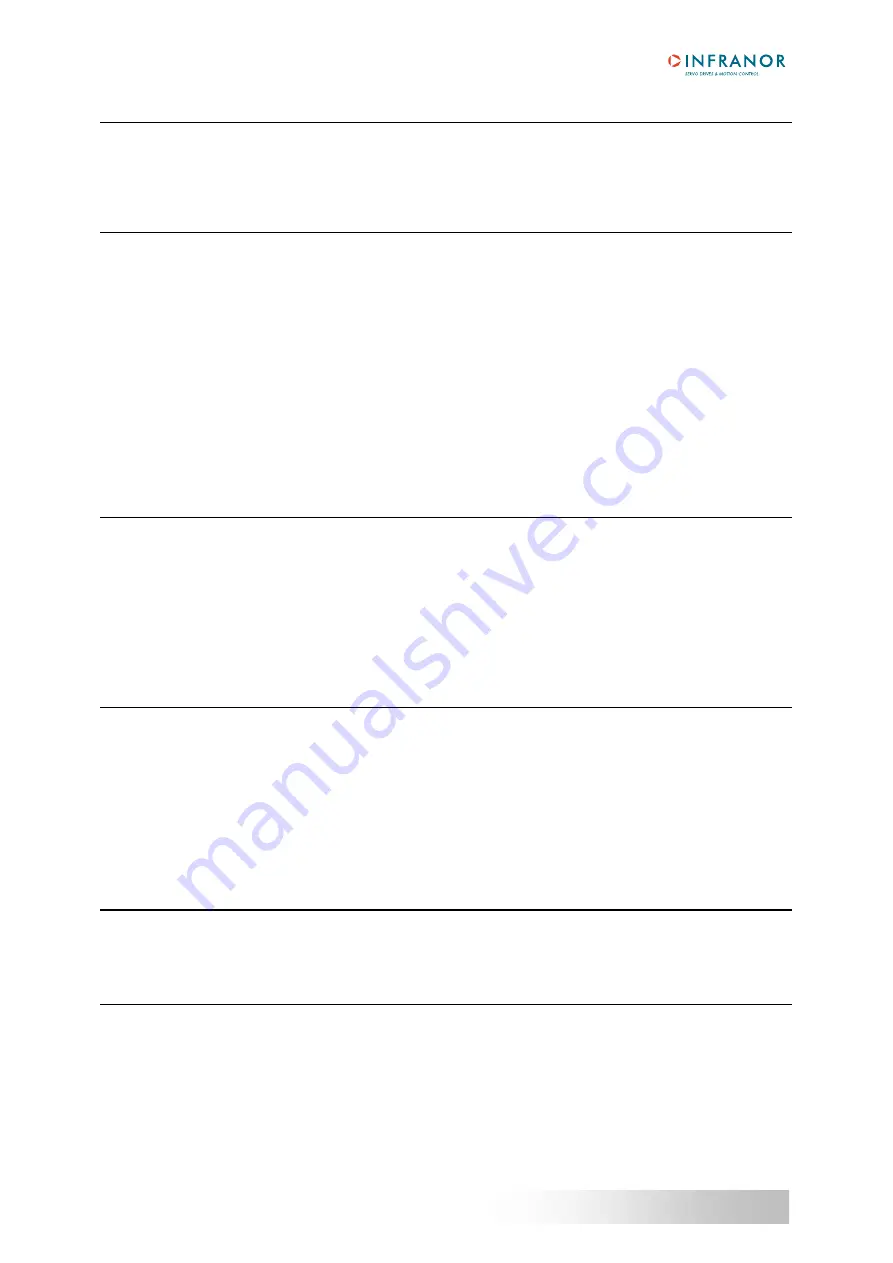
60
CHAPTER 9 – Parameter setting by Profibus
SMT-BD1/t
Reduced stiffness at standstill
PNU :
749
Reduce the speed regulator gain values at low speeds (below 100 rpm) when activated.
This parameter allows to reduce the motor vibrations in case of motor-load coupling backlashes.
Parameter
1
word.
= 0: disable the gains reduction,
= 1: enable the gains reduction.
Cogging acquisition procedure
PNU :
875
Parameter
None.
Limitation
Writing
only.
Note
This procedure allows the automatic acquisition of the motor cogging torque value in order to
provide the motor cogging torque compensation.
The motor cogging torque compensation is only necessary for specific applications where
torque accuracy better than 1 % is required. When changing either the motor, the amplifier or
the EEPROM, the cogging torque acquisition procedure must be renewed.
The motor must first be disabled and
uncoupled from the mechanical load
. The ENABLE
signal (X4 connector) must also be active. Before executing the procedure, check for free motor
shaft rotation over one revolution, that is not dangerous for the operator. Disable the
Reduced
stiffness at standstill
command if selected,
then execute an
Auto-tuning
procedure with the
High bandwidth
and the
Standard
filter selection before starting the cogging torque acquisition
procedure. The motor shaft must not be disturbed during the cogging torque acquisition
procedure. The procedure is taking a few minutes because the motor is moving at low speed
over 1 or 2 revolutions in both directions. The acquired cogging torque value is automatically
stored in the amplifier memory during the procedure execution.
Cogging torque compensation
PNU :
876
Enable the cogging torque compensation when activated.
Parameter
1
word.
= 0: disables the cogging torque compensation,
= 1: enables the cogging torque compensation.
Note
The motor cogging torque compensation is only necessary for specific applications where
torque accuracy better than 1 % is required. When changing either the motor, the amplifier or
the EEPROM, the cogging torque acquisition procedure must be renewed. The cogging
acquisition procedure must first be executed before enabling the cogging torque compensation.
2.4 - Application parameters
Amplifier mode
PNU :
720
Defines the amplifier operation mode (unwind/rewind, speed or torque).
Parameter
1
word
1
torque
mode
2
speed mode with PI regulator
4
unwind/rewind
mode
8
speed mode with P regulator
16
speed mode with PI
2
regulator
Execution
This instruction must be executed with disabled amplifier.
The amplifier is always configurated by default in unwind/rewind mode at power on.
Note
As from firmware EPROM version 506.64, the amplifier operating mode is saved in the
parameter EEPROM.
Maximum motor speed
PNU :
721
Defines the maximum motor speed value (and the speed scale as well) according to the application.
Parameter
1
word.
Limitation
This parameter varies between 100 rpm and 14000 rpm.
Execution
With
disabled
amplifier.
Motor rotation direction
PNU :
722
This instruction allows to reverse the motor rotation direction with regard to the input command. It also reverses
the position feedback.
Parameter
1
word
:
= 0: normal.
= 1: reversed.
Execution
With
disabled
amplifier.