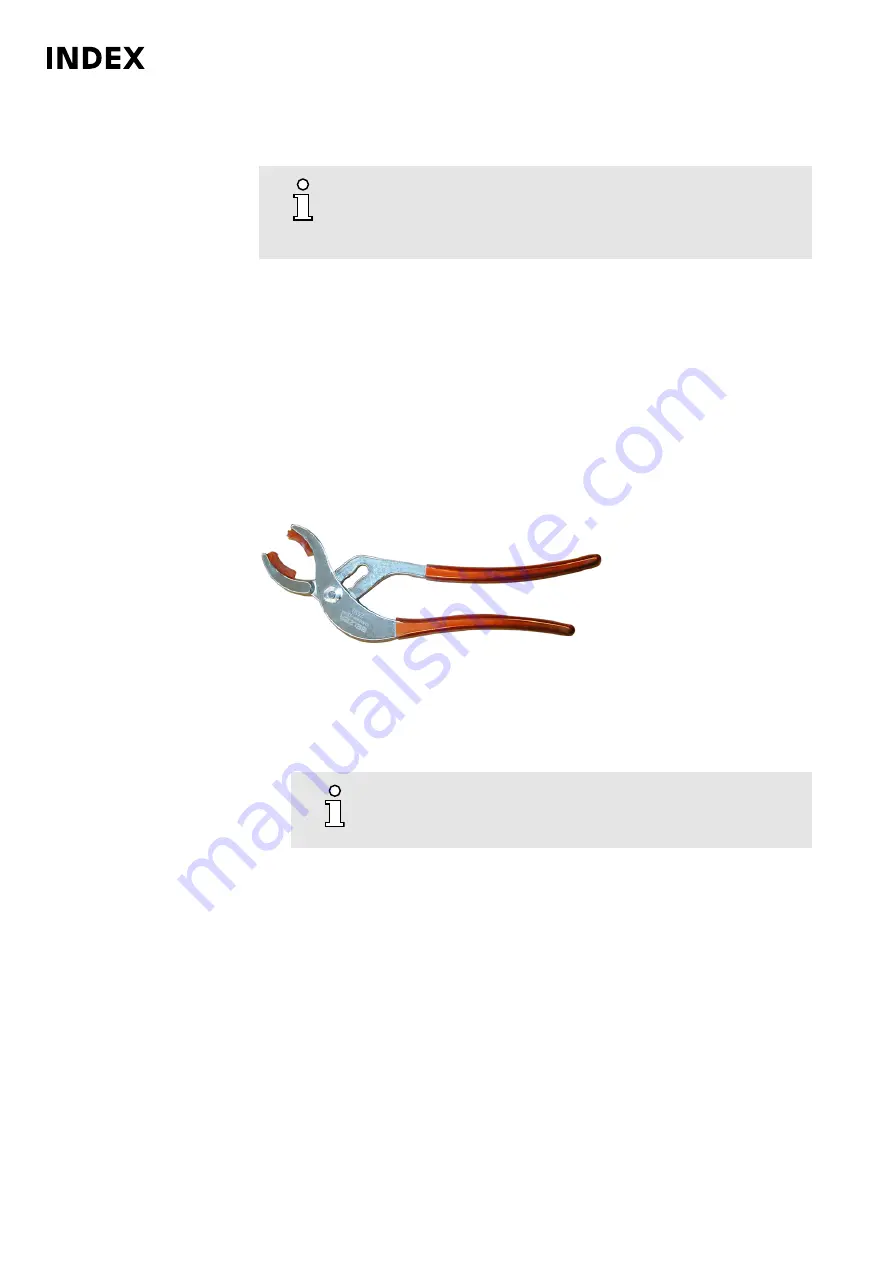
- Check all electrical connections and drive belts of the drive motors
Carrying out the maintenance activities described below requires
special knowledge. For this reason, these maintenance activities
must only be carried out by staff that has received adequate training
by the machine manufacturer!
Orientation
This activity is merely a test to check the power and encoder connections for proper
seating and tightness. Simultaneously, all drive belts are subjected to a visual
inspection.
Requirement
Move the tool carriers to a suitable position.
It may also be necessary to remove various covers or plates for carrying out a visual
inspection. Furthermore, a special pair of pliers is needed for tightening the power
and encoder connections.
Example: Special pliers for tightening power and encoder connections on the motors
Procedure
1. Loosen connector and check for corrosion and leaks.
2.
If traces of corrosion or moisture are visible, they must be
eliminated and their causes must be determined. If the
connectors cannot be cleaned, they must be replaced.
Maintenance Summary - 2.000 Operating hours
52
Maintenance Instructions
ABC.2
DIE244EN - 15.08.2022
Содержание ABC 2 Series
Страница 6: ...Table of contents IV Maintenance Instructions ABC 2 DIE244EN 15 08 2022 ...
Страница 50: ...Maintenance Summary 1 000 Operating hours 44 Maintenance Instructions ABC 2 DIE244EN 15 08 2022 ...
Страница 72: ...Maintenance Summary 2 000 Operating hours 66 Maintenance Instructions ABC 2 DIE244EN 15 08 2022 ...
Страница 109: ...Service Interval 5 Years Service Interval 5 Years 103 Maintenance Instructions ABC 2 DIE244EN 15 08 2022 ...
Страница 114: ...Maintenance Summary 5 Years 108 Maintenance Instructions ABC 2 DIE244EN 15 08 2022 ...
Страница 115: ...Service Interval 8 Years Service Interval 8 Years 109 Maintenance Instructions ABC 2 DIE244EN 15 08 2022 ...