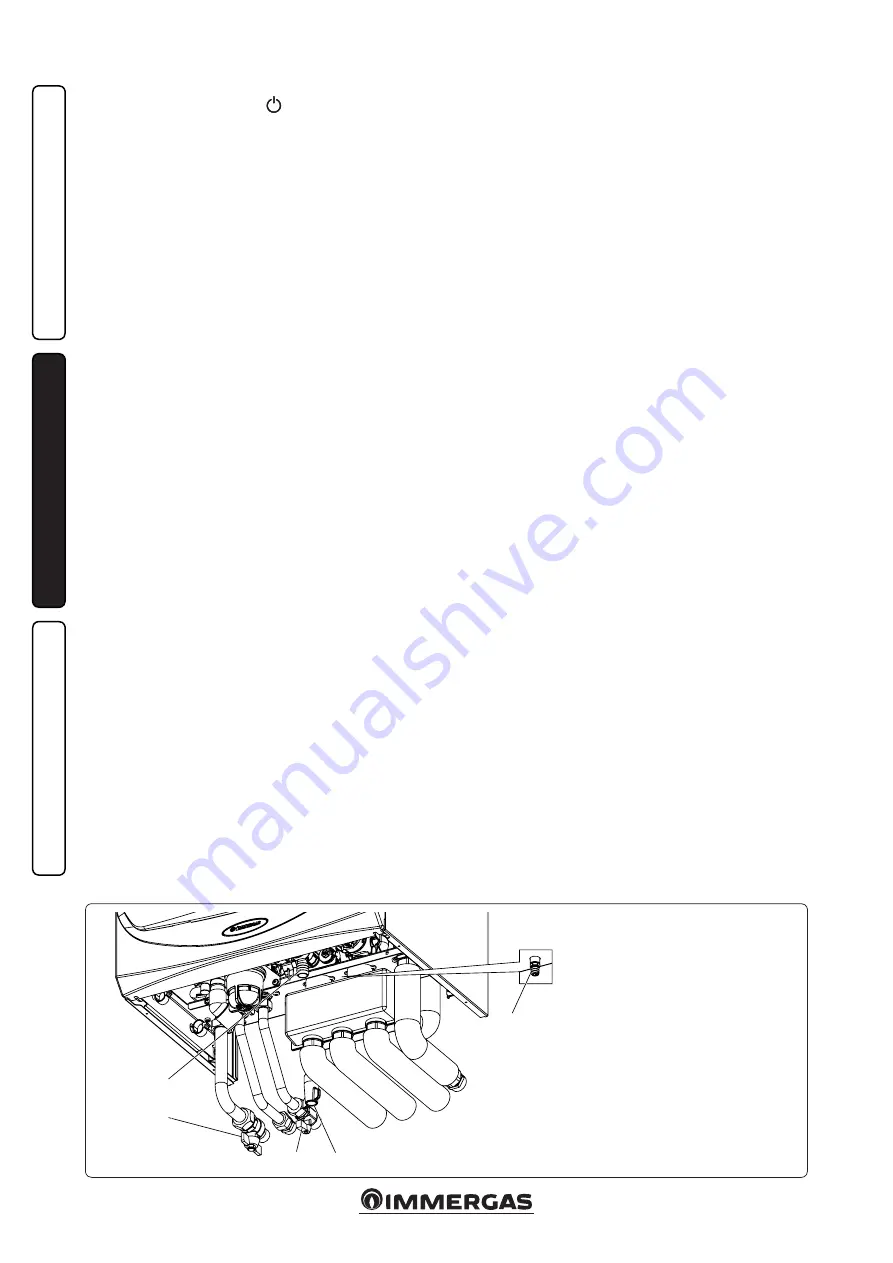
28
2-6
2
3
4
1
5
INS
TALLER
US
ER
MAINTEN
AN
CE TECHNI
CI
AN
2.8 BOILER SHUTDOWN
Switch the boiler off by pressing the “
” but-
ton, disconnect the onmipolar switch outside of
the boiler and close the gas cock upstream of the
appliance. Never leave the boiler switched on if
left unused for prolonged periods.
2.9 RESTORE CENTRAL HEATING
SYSTEM PRESSURE.
Periodically check the system water pressure.
The boiler pressure gauge should read a pressure
between 1 and 1.2 bar.
If the pressure falls below 1 bar (with the circuit
cold) restore normal pressure via the valve located
at the bottom of the boiler (Fig. 2-6).
N.B.:
close the valve after the operation.
If pressure values reach around 3 bar the safety
valve may be activated.
In this case, remove water from an air vent valve
of a radiator until 1 bar is reached or ask for as-
sistance from an authorised company.
If frequent pressure drops should occur, ask an
authorised company for assistance to eliminate
the possible system leakage.
2.10 SYSTEM DRAINAGE.
To drain the boiler, use the special draining
valve (Fig. 2-6).
Before draining, ensure that the filling valve is
closed.
2.11 ANTI-FREEZE PROTECTION.
The “Magis Victrix ErP” series boiler features
an anti-freeze function that lights the burner
automatically when the temperature falls below
4°C (standard protection up to minimum tem-
perature of -3°C). All information relative to
the anti-freeze protection is stated in Par. 1.3. In
order to guarantee the integrity of the appliance
and the domestic hot water heating system in
zones where the temperature falls below zero,
we recommend the central heating system is
protected using anti-freeze liquid and installation
of the Immergas Anti-freeze Kit in the boiler. In
the case of prolonged inactivity (second case),
we also recommend that:
- disconnect the electric power supply;
- the central heating circuit and boiler domestic
hot water circuit must be drained. In systems
that are drained frequently, filling must be car-
ried out with suitably treated water to eliminate
hardness that can cause lime-scale.
2.12 CASE CLEANING.
Use damp cloths and neutral detergent to clean
the boiler casing. Never use abrasive or powder
detergents.
2.13 DECOMMISSIONING.
In the event of permanent shutdown of the
boiler, contact an authorised company for the
suitable procedures and also ensure the electri-
cal, water and fuel supply lines are shut off and
disconnected.
Key:
1 - 3 bar safety valve
2 - Gas cock
3 - Domestic cold water inlet valve
4 - System filling valve
5 - System draining valve
Содержание MAGIS VICTRIX ERP
Страница 1: ...MAGIS VICTRIX ERP IE Instruction and recommendation booklet 1 038946ENG ...
Страница 2: ......