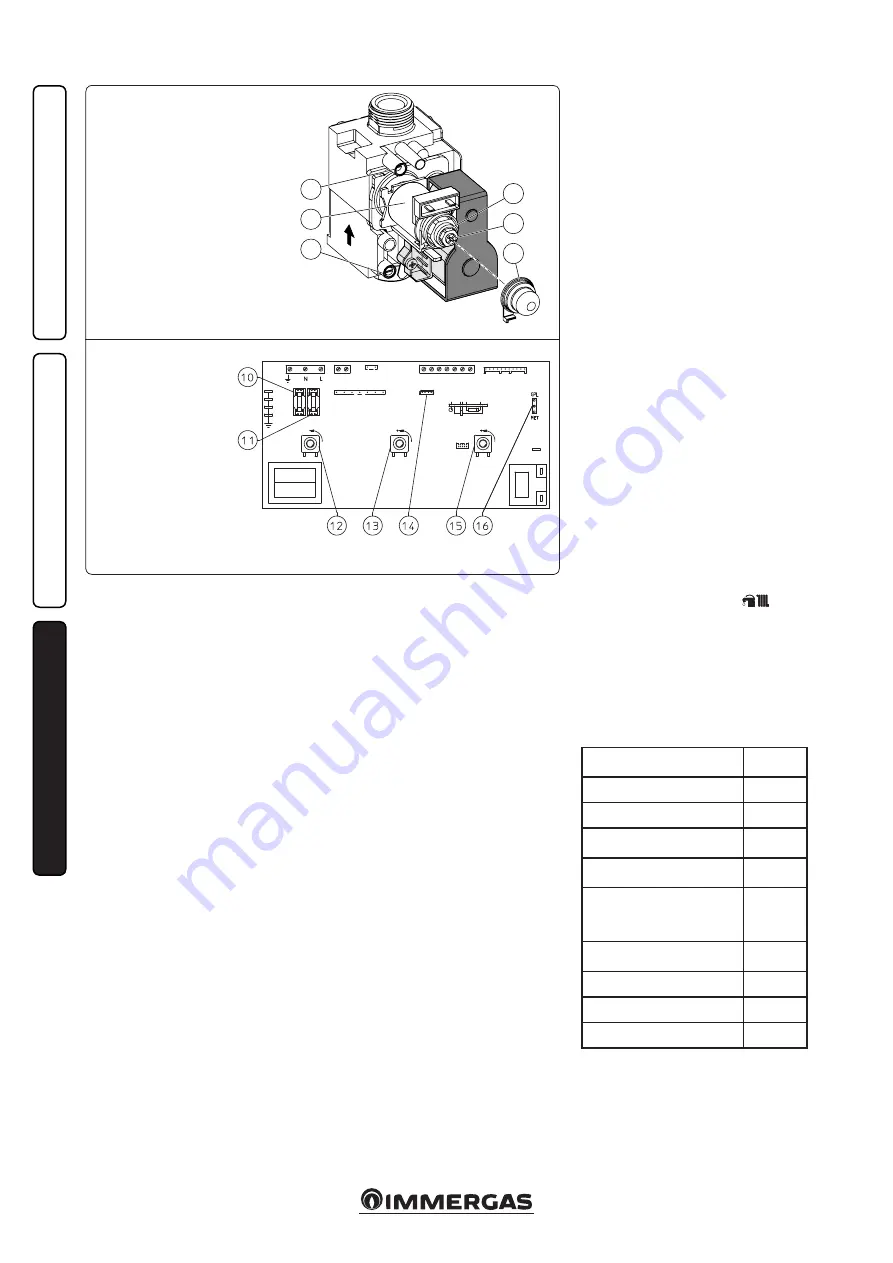
16
3-3
3-4
4
3
2
1
5
6
INS
TALL
AT
O
R
US
ER
MAINTEN
AN
CE TECHNI
CI
AN
3.4 CONVERTING THE BOILER TO
OTHER TYPES OF GAS.
If the boiler has to be converted to a different gas
type to that specified on the data-plate, request
the relative conversion kit for quick and easy
conversion.
The gas conversion operation must be carried
out by an authorised company (e.g. Authorised
Technical After-Sales Service).
To convert to another type of gas the following
operations are required:
- remove the voltage from the appliance;
- replace the main burner injectors, making sure
to insert the special seal rings supplied in the
kit, between the gas manifold and the injectors;
- move jumper 16 (Fig. 3-4) into the correct
position for the type of gas in use (Methane or
L.P.G.);
- to access adjustments on the circuit board the
cover must be removed from the dashboard by
loosening the rear screw fasteners;
- apply voltage to the appliance;
- adjust the boiler maximum heat power;
- adjust the boiler minimum heat power;
- adjust (eventually) the heating power;
- seal the gas flow rate devices (if adjusted);
- after completing conversion, apply the sticker,
present in the conversion kit, near the data-
plate. Using an indelible marker pen, cancel
the data relative to the old type of gas.
These adjustments must be made with reference
to the type of gas used, following that given in
the table (Par. 3.16).
3.5 CHECKS FOLLOWING
CONVERSION TO ANOTHER TYPE
OF GAS.
After making sure that conversion was carried
out with a nozzle of suitable diameter for the
type of gas used and the settings are made at the
correct pressure, check that:
- there is no flame in the combustion chamber
- the burner flame is not too high or low and that
it is stable (does no detatch from burner)
- the pressure testers used for calibration are
perfectly closed and there are no leaks from
the gas circuit.
N.B.:
all boiler adjustment operations must be
carried out by a qualified company (e.g. Au-
thorised After-sales Service). Burner calibration
must be carried out using a “U” or digital type
differential pressure gauge, connected to the gas
valve pressure outlet (part. 4 Fig. 3-3), keeping
to the pressure value given in the tables (Par.
3.16) according to the type of gas for which the
boiler is prepared.
3.6 POSSIBLE ADJUSTMENTS OF THE
GAS VALVE.
• Adjustment of boiler nominal heat output (Fig.
3-3).
- Turn the domestic hot water selector knob (10
Fig. 2-1) to the maximum functioning position;
- open the domestic hot water cock in order to
prevent modulation intervention;
- adjust the boiler nominal power on the brass
nut (3), keeping to the maximum pressure
values stated in the tables (Par. 3.16) depending
on the type of gas;
- by turning in a clockwise direction the heating
potential increases and in an anti-clockwise
direction it decreases.
• Adjust the boiler minimum thermal input (Fig.
3-3).
N.B.:
only proceed after having calibrated the
nominal pressure.
Adjustment of the minimum thermal input is
obtained by operating on the cross plastic screws
(2) on the gas valve maintaining the brass nut
blocked (3);
- disconnect the power supply to the modulating
reel (just disconnect a faston); By turning
the screw in a clockwise direction, the
pressure increases, in an anti-clockwise
direction it decreases. On completion of
calibration, re-apply the power supply to the
modulating reel. The pressure to which the
boiler minimum power must be adjusted,
must not be lower than that stated in the
tables (Par. 3.16) depending on the type of gas.
N.B.:
to adjust the gas valve, remove the plastic
cap (6); after adjusting, refit the cap and screw.
3.7 PROGRAMMING THE CIRCUIT
BOARD.
The Avio 24 2 ERP boiler is prepared for possible
programming of several operation parameters. By
modifying these parameters as described below, the
boiler can be adapted according to specific needs.
To access the programming phase, proceed as
follows: position the main selector switch on Reset
for a period of time between 15 and 20 seconds
(after about 10 sec. LEDs 2 and 3 will start to flash at
the same time. Wait for this to end and re-position
the main selector switch on domestic water and
heating). At his point, re-position the main selector
switch on domestic water-heating.(
).
When the programming phase has been
activated, enter the first level where it is possible
to choose the parameter to be set.
The latter is indicated by the fast flashing of one
of the LEDs between 1 and 8 (Fig. 2-1).
Selection is made by turning the domestic hot
water temperature selector switch (10). For
association of the LED to the parameter, see the
following table:
List of parameters
Flashing
LED (fast)
Minimum heating power
Led 1
Maximum heating power
Led 2
Heating switch-on timer
Led 3
Heating power output ramp
Led 4
Heating switch-on delay on request
from Environmental Thermostat,
Mini Digital Remote Control or
Remote Friend Control
V2
Led 5
Domestic water thermostat/Boiler
hysteresis
Led 6
Circulating pump functioning
Led 7
Functioning gas
Led 8
Boiler mode
Led 1 and 8
Once the parameter to be modified has been
selected, confirm by turning the main selector
switch to Reset momentarily until the LED
relative to the parameter switches-off, then
release.
Given the OK for selection, pass to the second
level where it is possible to set the value of the
SIT 845 gas valve
Key:
1 - Coil
2 - Minimum power adjustment screws
3 - Maximum power adjustment nut
4 - Gas valve outlet pressure point
5 - Gas valve inlet pressure point
6 - Protection hood
Circuit board
10 - Line fuse 3.15AF
11 - Neutral fuse 3.15AF
12 - Main selector switch
13 - Domestic water temperature trimmer
14 - RS232 computer interface
15 - Heating temperature trimmer
16 - METHANE L.P.G. gas type selector
Содержание AVIO 24 2 ERP
Страница 27: ......