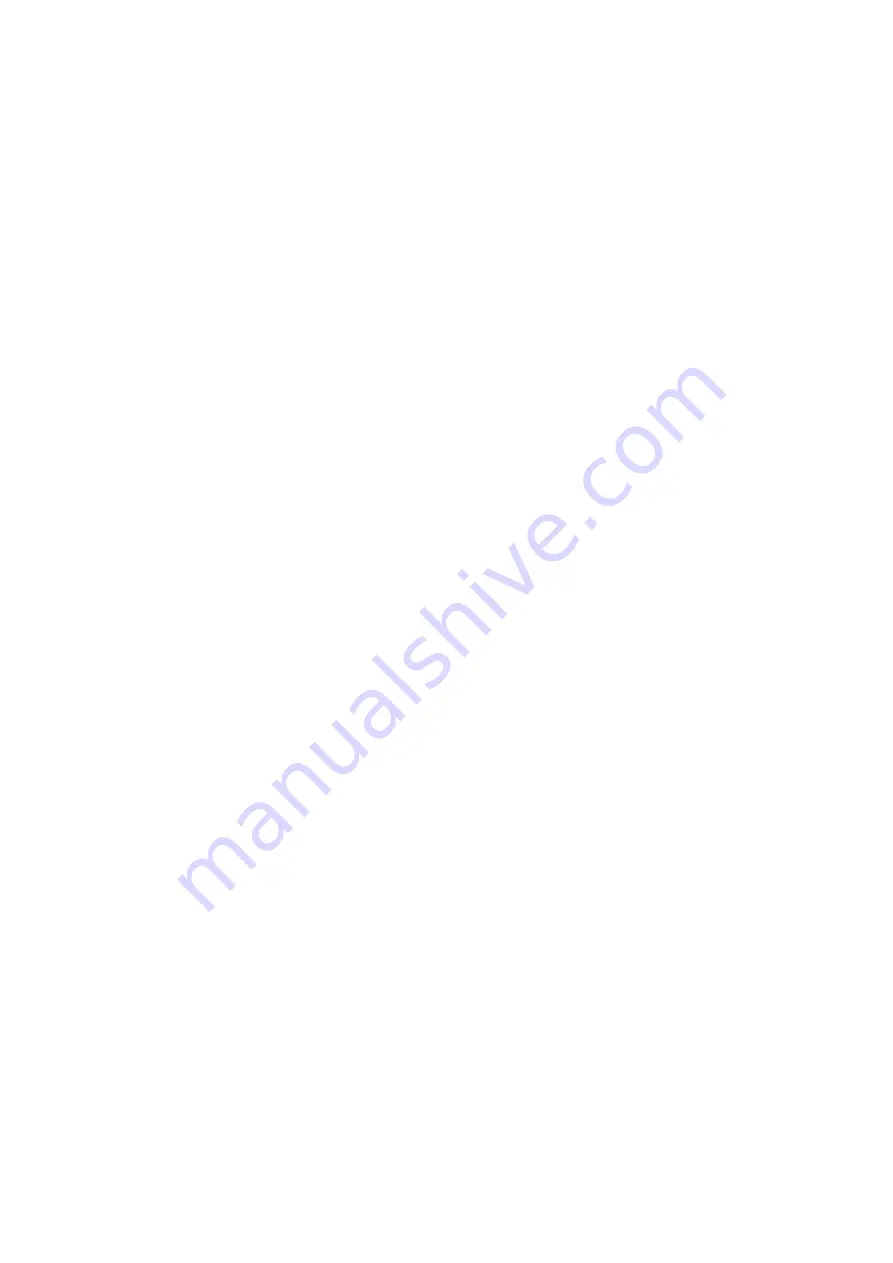
28/11/02-\\SERVER\TECNICO\-SNZ\0Sit\hVtf500shie.doc-Scheda Identificazione Codice Padre (mac.sott.etc...)-
12 di 62 pagine.
Pagina
n°-
12
63LA
8 - MACHINE SETTING FOR STARTING
Verify that machine has not clear damages or faults and check upon the standard equipment that includes
the tools, fittings to do some adjustments, using and maintenance handbook .
In case the machine is supplied with additional equipment make sure that it is adaptable to the machine.
Point in good time the possible damages or faults to the reseller or to the service staff before starting
machine( for ex. rust on the metallic parts, dinges on the sheets, and so on... ).
Remove the lock flask-pos.2 and 3/dr.RI0101- between the saw frame and the base , and bring it again the
screws in their seat. Remove the protective substances from the surfaces, used to keep the machine during
the moving and transit, by cleaning them with a non-filamentous cloth or paper and please check that there
is no rust in the metallic parts.
In case of using compressed air jet always wear proper eye protection.
Open the base doors-pos.5 and 6/dr.RI RI0102 ( the keys are fixed at the vice feeding cables) Take away
the chip pan tank -pos.7/dr.RI0102 - by unhooking it from the guides then remove the possible dirty that can
obstruct the passage of the coolant.
The parts in motion ( band guides, trolleys, pivots, bearing support, bearing disc and so on ) are already
lubricated, the reducer gear holds the exact quantity of oil necessary to the operation ( lubrication FOR-LIFE
).
Hydraulic system is ready to start.
8.1 - COOLING SYSTEM
Prepare the cooling mixing the cutting oil and water ( the tank holds about 30 litres ) in proportion 1/10, 1/15
or according to the instructions of product supplier . After taking the chip pan tank away , pour out the
cooling in the tank or directly on the work table - In this case keep attention that chip pan tank and the tank
are correctly placed .
8.2 - ELECTRICAL CONNECTION
Verify that voltage and power frequency are compatible with numbers reported in the technical data plate (
placed on the right side of the floor stand ) difference over 10% causes some working unevenness more or
less manifested. This operation must be made by authorized , operators ( for ex. by an electrician ) .
Connect an electric cable ( four-polar 4 mmq of section, made according to CEI 20-22 ) to the terminals
marked R, S, T, PE placed on the right, inside the door-pos.6/dr.RI0102-. Mount a plug proper to the wall
socket used in the place where the machine must be installed.
The pashing performed by the manufacturer allows to get a right rotation of all motors by connecting the
wires in the following order L1=R, L2=S, L3=T, anyhow check as follows : ( close the coverband carters in
the tight way ) .
a) in case of EMERGENCY the button is on , turn it off and turn it 1/4 of turning in the marked direction -
pos.1/drawing RI0055-
b) turn on the main switch-pos.8/drawing RI0102- , some leds flash on the control panel -pos. drawing
RI0055- and the display shows some numbers and/or figures.
c) be sure that pressure gauge of hydraulic installation-pos.1/drawing RI0085 , accessible from the door-
pos.5/dr.RI0102 , shows a pressure of about 16/20 BAR.
d) if does not happen in the first 10 seconds turnf off the machine by switching off the general switch and
check the connection to the line ( throw off the feeding plug , reverse the connection of two of the wires of
line connection , excluding the green / yellow cable of grounding and start again from point a) .
e) Be sure that coolant is sucked in by the tank and arrives in the cutting area. ( only if pump recycling is
working ).
f) Stop the working by pushing the main switch-pos.8/dr.RI0102- . If it is supplied with the external
VOLTAGE TRANSFER , place it in the right way and far from the material loading/unloading area.
8.3 - BAND TENSIONING
The machine is equipped with an untensioned band and the starting of the motor is impossible if right force
of tension has not been opened up before. Therefore, let the saw frame on cutting position at 0 deg., open