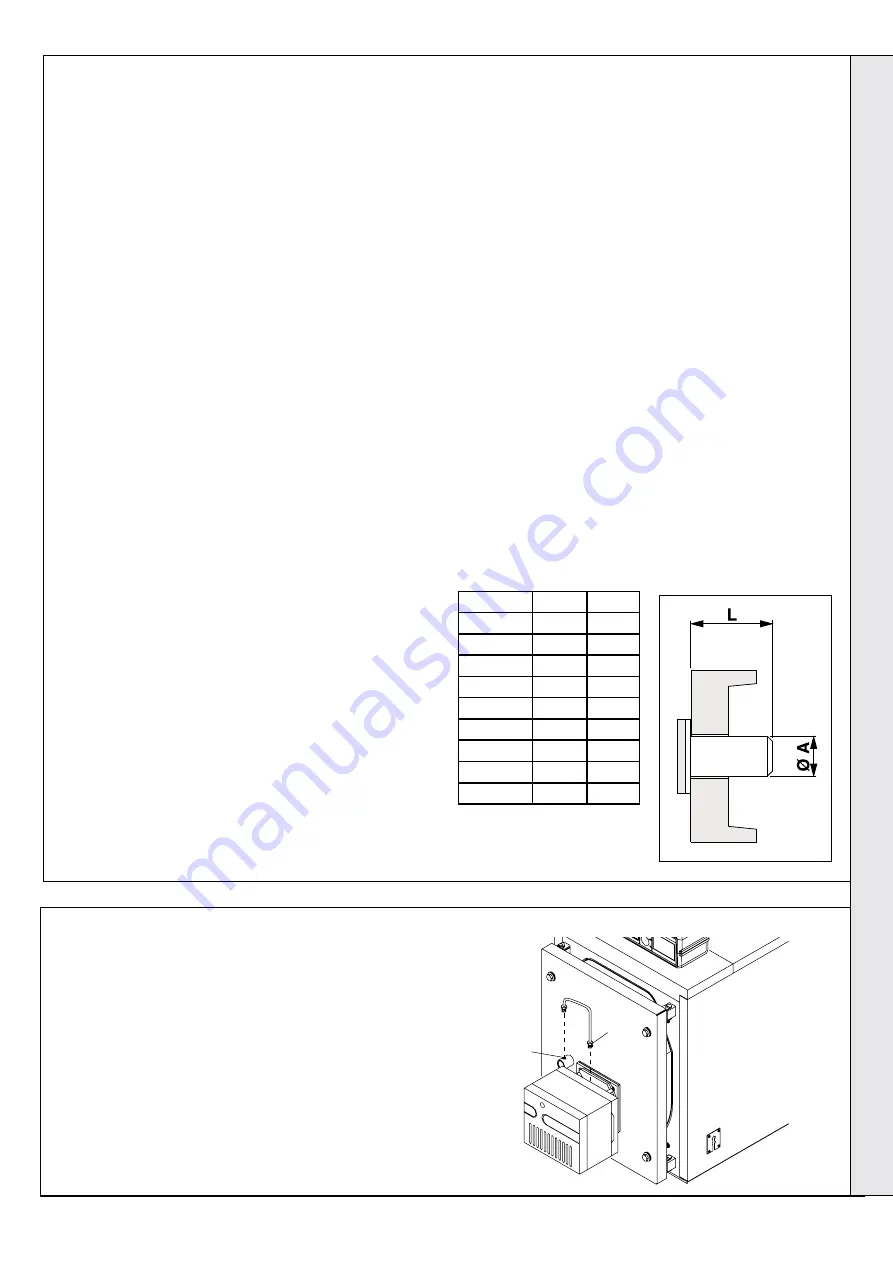
29
Vanguard L -
Installation & Servicing
INSTALLATION
2
1
van 5721
28 BURNER
The Vanguard boiler range is suitable for use with oil, gas, or
dual fuel burners. Nuway, EOGB and Riello burners can be
supplied as standard.
Burners from other manufacturers can be supplied on request.
Burners will be supplied for on/off or high/low operation.
Modulating burners can be supplied on request.
Burner Door
Burner doors have been pre-drilled to match the standard
burners offered. Should another manufacturer's burner be
used then it is the responsibility of the burner manufacturer to
match the burner to the doors available.
Burner Mounting
When mounting the burner to the boiler front door, check for
soundness around the burner flange and its gasket. Each
boiler is supplied with a length of ceramic fibre rope (cross
section 25x25 mm). This rope has to be put around the burner
tube to completely seal the tube and the hole in the door
insulation.
Gas Supply
The gas supply MUST be sized in accordance with British Gas
recommendations and be prefabricated in compliance with
CP 331 Pt 1 and any Local Gas Board installation standards.
The Local Gas Board should be contacted, at a stage prior to
installation, for any advise or information required. Details and
advice, relating to the use of L.P.G. for firing the Ideal Vanguard
L range of boilers, are available on request to
Ideal
.
Oil Storage Tank
The oil storage tank, oil supply pipe and connections to the
burner unit MUST comply with the requirements of BS 779 and
CP 5410.
The installation should conform to the recognised standards of
good practice in the trade and comply with the relevant Codes
of Practice, Building Regulations and Local Authority, Fire and
Insurance requirements.
Conformity of the Burner
All the burners equipping the Vanguard L boilers must be CE
certified and must conform to the following directives and
standards;
- Gas Appliances Directive (90/396/CEE)
- EN 267 - Automating oil burners of monoblock type testing
- EN 676 - Automatic forced draught burners for gaseous fuels.
Choice of the Burner
The correct choice and the adjustment of the burner are
fundamental for the best operation of the boiler and then they
shall be accurate and not under evaluated.
The burner will be selected by a verifying that its working
diagram (fuel flow rate - pressure in the furnace) is compatible
with the same features declared for the boiler.
Remember that the smoke side resistance, i.e. the
counterpressure in the furnace, are referred to "0" draught at
the chimney base.
It is also convenient that the burner blast tube has its length not
shorter than that shown in the table and that the flame has a
shape suitable to the characteristics of the Vanguard L furnace.
In fact to better exploit all the heating surface of the reversed
flame furnace, it is necessary to use burners capable to
guarantee a long and narrow flame at all operating conditions
or also at minimum input in case of two stage or modulating
burners.
Too short flames can cause a localised overheating of the
front part of the furnace, and the combustion products, not
sufficiently cooled down, entering the smoke pipes at a too high
temperature, can cause important damages to the boiler.
The burner manufacturing companies are available to supply
the flame dimensions developed by their burners.
More informations are given in the paragraph "Commissioning".
Burner Blast Tube Minimum Length
Model
Ø A mm L mm
340-630
220
250
760-970
270
270
1100-1320
320
300
1570-1850
320
320
2200-2650
380
350
3000
380
400
3500-4000
400
400
4500-6000
500
480
6500-7000
500
630
29 FLAME INSPECTION
The Vanguard boiler range is provided with a
sightglass tube placed above the burner door.
The sightglass tube has a thread (1) suitable for
a pressure gauge and or for a cooling line (2) (not
supplied) connection as shown in the diagram.
INST
ALLA
TION
Содержание Vanguard L 340
Страница 37: ...37 Vanguard L Installation Servicing NOTES...
Страница 38: ...38 Vanguard L Installation Servicing NOTES...
Страница 39: ...39 Vanguard L Installation Servicing NOTES...