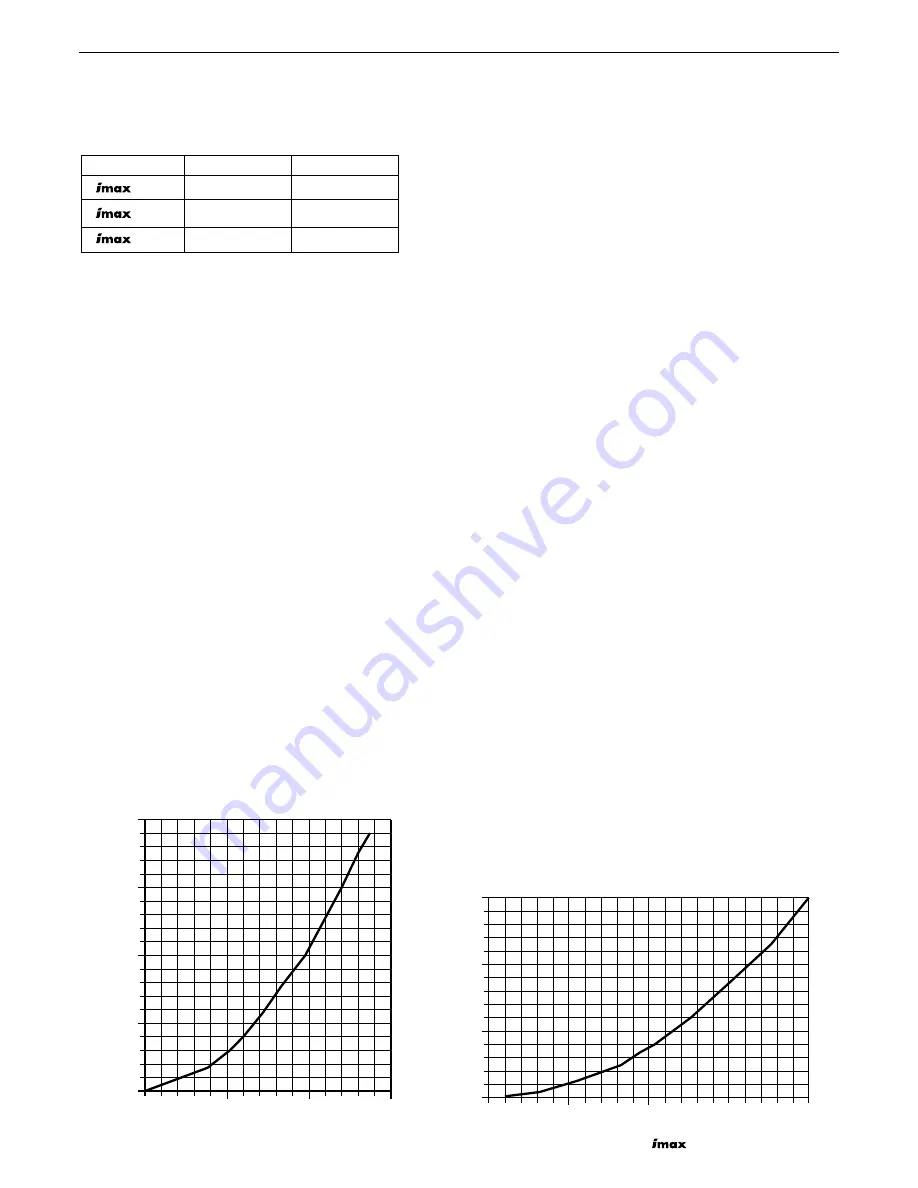
6
-
Installation & Servicing
GENERAL
HYDRAULIC RESISTANCE W80
HYDRAULIC RESISTANCE W45 / W60
When sizing pumps, reference should be made to the graphs
below which show the boiler resistance against flow rates, to
achieve the required temperature differential.
Flow rates for common systems using either 11ºC or 20ºC
temperature differentials are given in the table below.
11ºC
20ºC
W45
0.94 l/s
0.53 l/s
W60
1.28 l/s
0.69 l/s
W80
1.69 l/s
0.94 l/s
Note.
•
With the boiler firing at maximum rate, the temperature
differential should not be less than 10ºC. High flow rates
required for lower temperature differentials could lead to
errosion of the heat exchanger water ways.
•
With the boiler firing at minimum rate, the temperature
differential should not be greater than 35ºC. Lower flow rates
generating higher temperature differentials will lead to lock
out of the boiler.
•
The lower the return temperature to the boiler, the higher the
efficiency.
In installations where all radiators have been provided with
thermostatic radiator valves, it is essential that water circulation
through the boiler is guaranteed. This can be best achieved by
means of a differential pressure valve, which is installed in a
bypass between the flow and return pipes. The bypass should
be fitted at least 6m from the boiler, and should use a minimum
size of 28mm pipe. The bypass should be capable of allowing a
minimum flow rate to achieve a temperature differential of no
greater than 35ºC at minimum rate.
WATER TREATMENT
These boilers incorporate an ALUMINIUM heat exchanger.
IMPORTANT. The application of any other treatment to this
product may render the guarantee of Caradon Ideal Limited
INVALID.
Caradon Ideal Limited recommend Water Treatment in
accordance with Guidance Notes on Water Treatment in Central
Heating Systems.
Caradon Ideal Limited recommend the use of Fernox Copal or
MB1, GE Betz Sentinel X100 or Salamander Corrosion Guard
inhibitors and associated water treatment products, which must
be used in accordance with the manufacturers' instructions.
For further information contact:
Fernox Manufacturing Co. Ltd., Cookson Electronics,
Forsyth Road, Sheerwater, Woking, Surrey, GU21 5RZ
Tel: +44 (0) 1799 521133
or
G E Betz Ltd, Sentinel Division, Foundry Lane, Widnes,
Cheshire, WA8 8UD
Tel: +44 (0) 151 424 5351
or
Salamander Engineering Ltd., Unit 24, Reddicap Trading Estate,
Sutton Coldfield, West Midlands, B75 7BU
Tel: +44 (0) 121 378 0952
Notes.
1. It is most important that the correct concentration of the water
treatment products is maintained in accordance with the
manufacturers' instructions.
2. If the boiler is installed in an existing system any unsuitable
additives MUST be removed by thorough cleansing.
BS7593:1992 details the steps necessary to clean a
domestic heating system.
3. In hard water areas, treatment to prevent limescale may be
necessary - however the use of artificially softened water is
NOT permitted.
4. Under no circumstances should the boiler be fired before the
system has been thoroughly flushed.
ELECTRICAL SUPPLY
Wiring external to the appliance MUST be in accordance with the
current I.E.E. (BS7671) Wiring Regulations and any local
regulations which apply. For Ireland reference should be made
to the current ETCI rules for electrical installations
The point of connection to the mains should be readily
accessible and adjacent to the boiler.
CONDENSATE DRAIN
A condensate drain is provided on the boiler. This drain must be
connected to a drainage point on site. All pipework and fittings
in the condensate drainage system MUST be made of plastic -
no other materials may be used.
IMPORTANT. Any external runs must be insulated.
pressure drop (mbar)
0
200
150
100
50
0
0.5
1.0
1.5
waterflow litres/second
ima5391
pressure drop (mbar)
0
300
200
100
0
0.5
1.0
1.5
2.0
waterflow litres/second
ima5389
Содержание imax W45
Страница 1: ......
Страница 53: ...53 Installation Servicing NOTES...
Страница 54: ...54 Installation Servicing NOTES...
Страница 55: ...55 Installation Servicing NOTES...