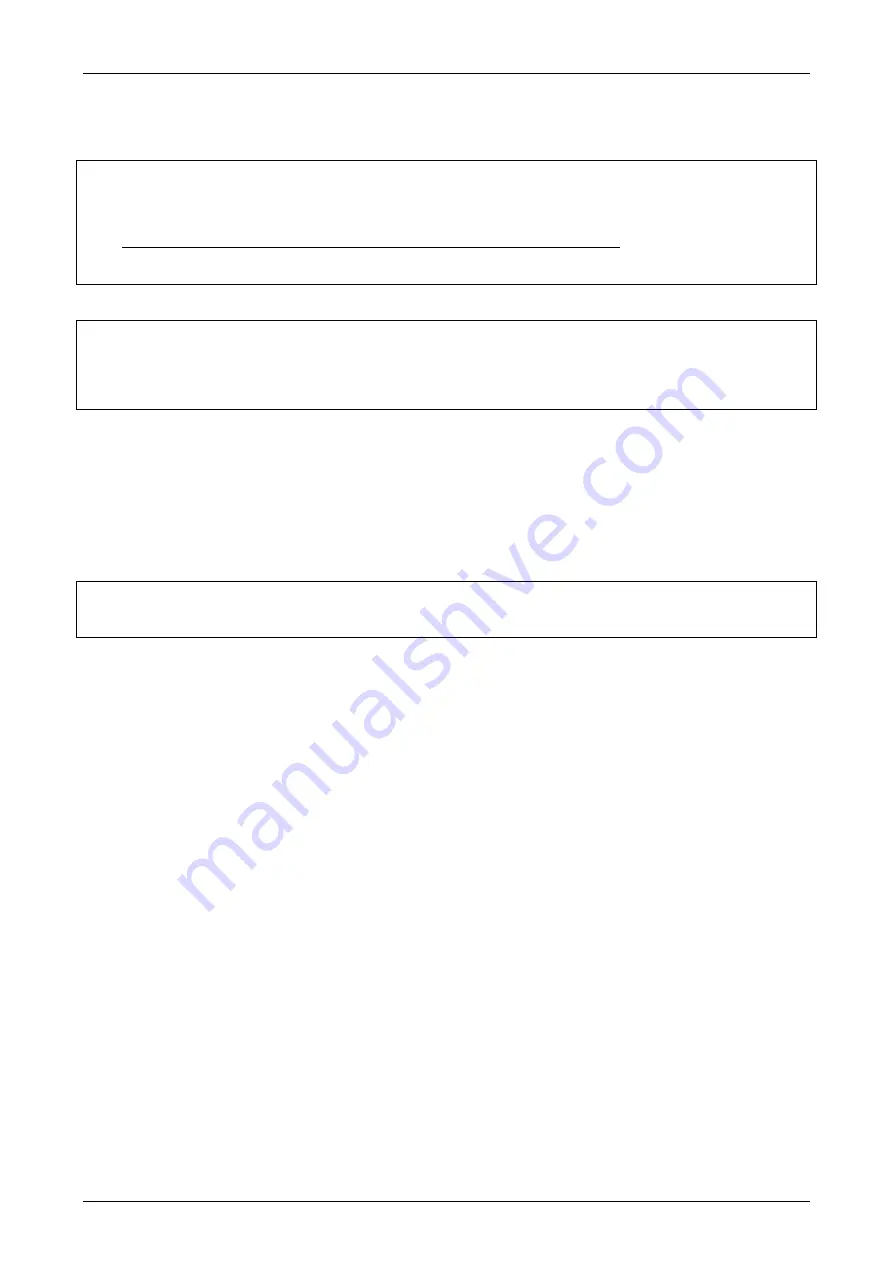
26
Pressurisation values should be included in the range given in the table of technical specifications.
I
MPORTANT
The delta T between flow and return must not exceed 30°C, in order to avoid thermal shocks in the
boiler. The boiler return temperature must be higher than 50°C on natural gas or LPG firing and high-
er than 40°C on oil firing, in order to protect the boiler from corrosion due to acid flue gas condensa-
tion; the guarantee therefore does not cover damages due to condensation.
If the system return temperature does not fulfill the above requirements, it is necessary to increase
the return temperature by using a mixing valve and/or a recirculation pump.
GREENOX BT COND:
IMPORTANT
The temperature gradient between flow and return, with burner running at rated output of the boiler,
must range from 10°C to 25°C. This protects the generator both from excessive flow, which can
cause vibrations and noise, and from hot water stagnation which causes limestone build-up and cre-
ates internal thermal shocks.
It is recommended that the burner switch is always switched on in order to maintain water temperature ap-
proximately equal to the value the thermostat is set to.
If the flue gas seal is poor in the front part of the boiler (manhole and burner plate) or the back part
(smokebox), the closing tie rods of the individual parts must be adjusted; if this is not sufficient, the seals
must be replaced
.
CAUTION
Do not open the manhole and do not remove the smokebox while the burner is working. Always wait
a few minutes after the burner has been switched off until the insulating parts are cooler
.
Содержание GREENOx BT COND 180
Страница 31: ......