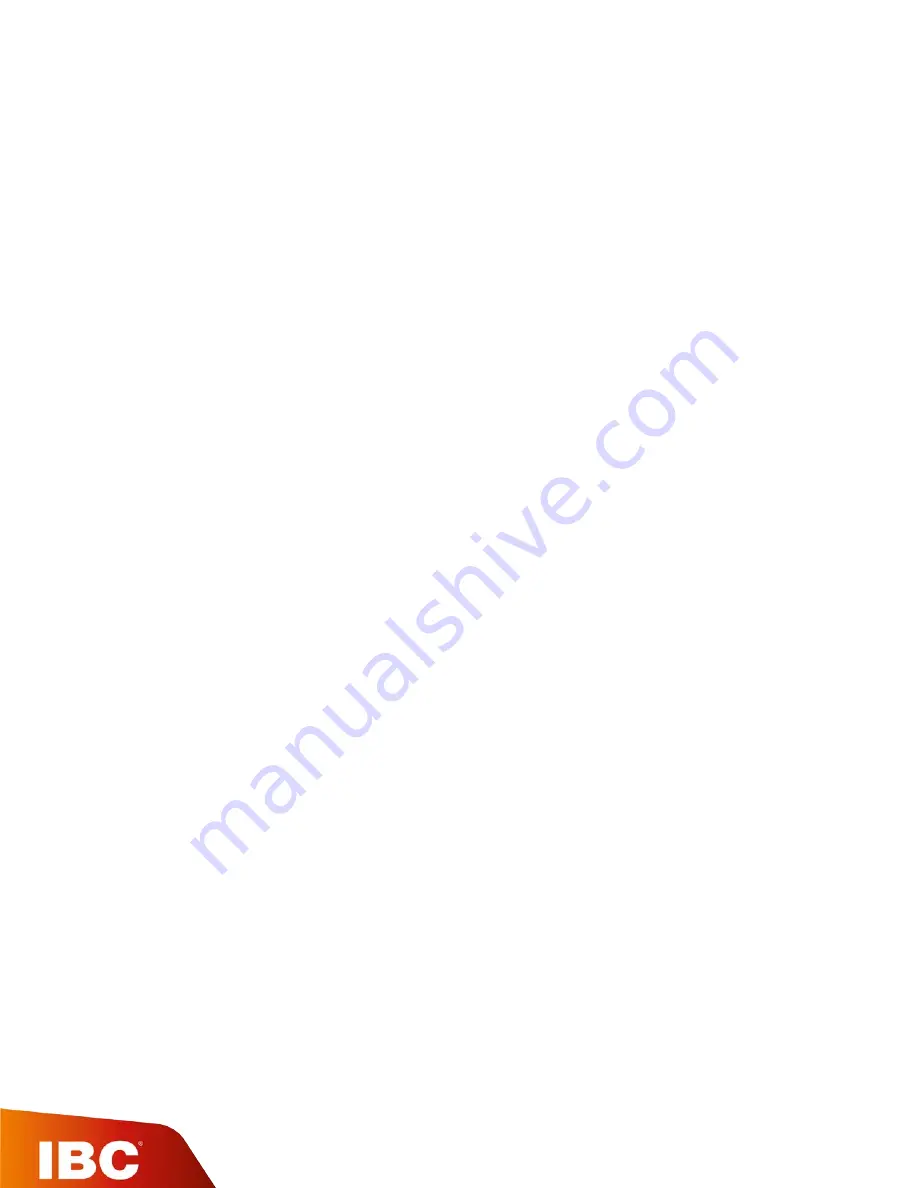
CAN
IBC Technologies Inc.
USA
IBC Technologies USA Inc
A
8015 North Fraser Way
A
121 Walter A Gaines Way
Burnaby, BC Canada V5J 5M8
Lawnside, NJ 08045 USA
T
604-877-0277
T
856-877-0544
F
604-877-0295
F
856-735-5584
Toll Free: 1-844-HEAT-IBC/ 1-844-432-8422
www.ibcboiler.com
Information in this document is subject to change without notice. IBC assumes no responsibility for
changes made to the manual due to clerical errors, to regulation changes, or to product development.
September 23, 2022
|
120-270E10
©
IBC Technologies Inc. 2022
Содержание SL Series
Страница 8: ...Intentionally left empty...
Страница 12: ...Figure 5 Top view SL 40 399 G3 Figure 6 Bottom view SL 40 399 G3 8 Section Specifications...
Страница 14: ...Intentionally left empty...
Страница 64: ...Figure 40 Electric wiring connections 60 Section Installation...
Страница 76: ...Intentionally left empty...
Страница 96: ...Intentionally left empty...
Страница 108: ...Intentionally left empty...
Страница 109: ...105 Appendices Wiring diagrams V 10 Controller electrical diagram Figure 45 Controller electrical diagram...
Страница 110: ...Internal wiring diagram Figure 46 Internal wiring diagram 106 Section Appendices...
Страница 111: ...Sequence of operations Figure 47 Sequence of Operation 107 Sequence of operations...
Страница 113: ...Item Description Part ID Kit Quantity 200 Fan or 240 113 P 311 1 109 Boiler part diagrams SL 26 260 G3...