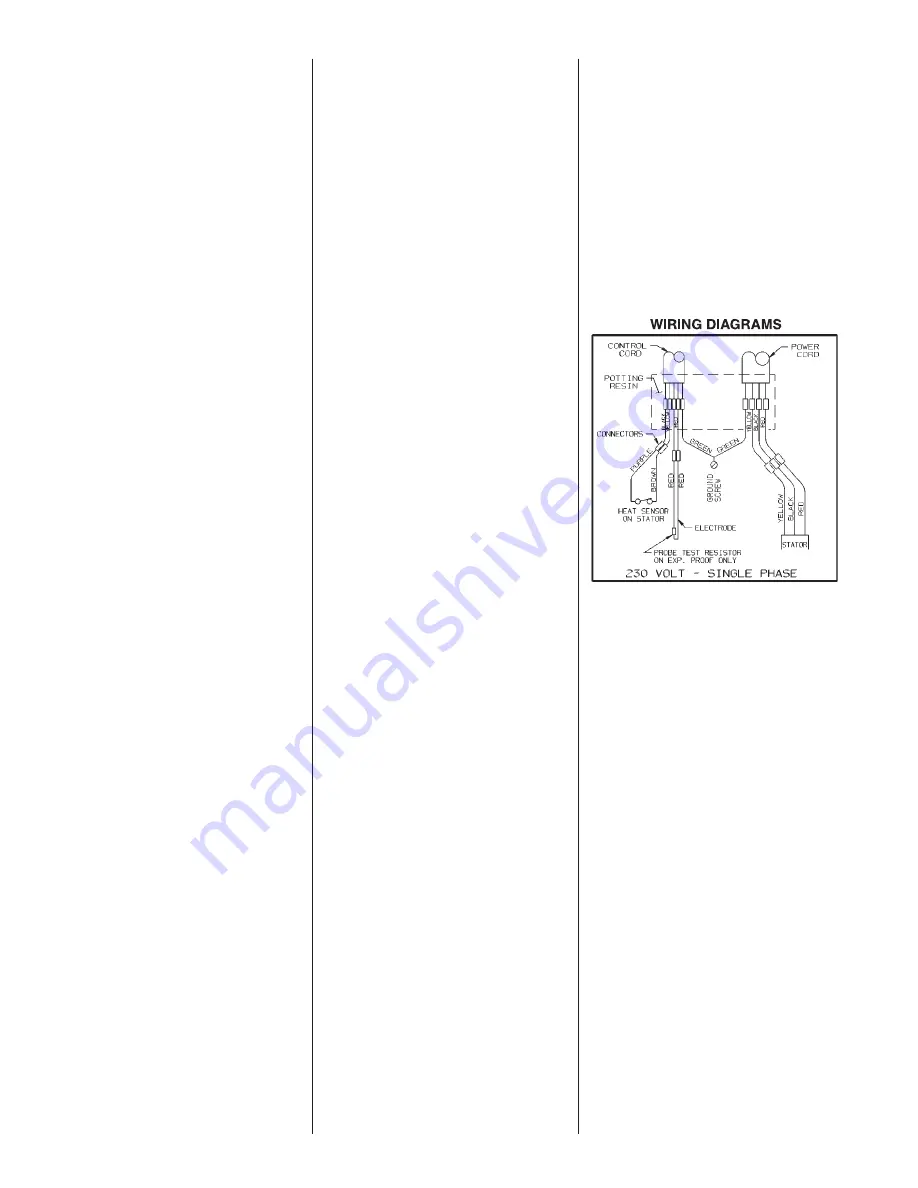
6
around the entire diameter.
Note, these parts should be
discarded and a new seal
assembly installed.
5. If the oil in the seal
chamber was drained, examine
the contents to determine if the
upper seal has been damaged.
Signs of grit or other abrasive
material may indicate that the
upper seal has also been
damaged. Pressurizing the
motor housing assembly
between 7 and 10 psi and
observing any drop in
pressure will indicate if
the upper seal is functioning
properly.
NOTE: Upper seal repairs must
be done at a Hydromatic
authorized service center or at
the Hydromatic factory. Any
unauthorized field repair voids
warranty and the explosion-
proof approval on the CSA
listed pumps.
Reassembly:
1. Remove the ceramic
portion of the new seal from
the package. Brush new
dielectric oil around the rubber
portion of the stationary
assembly and into the pocket
in the seal housing. Note,
keep the oil off the seal face.
Without scratching the seal
face, press the ceramic
stationary portion into the seal
housing. A piece of PVC pipe
that fits onto the face of
the seal works well for
installation. With clean cloth,
lightly wipe the face of the
seal surface to make sure it is
dirt free. Remove the rotating
portion of the seal from the
package and lubricate the
inside diameter of the rubber
bellows and the outside
diameter of the shaft. Place
the seal over the shaft. Evenly
press on the body of the
rotational assembly and slide it
down the shaft until the seal
faces meet. PVC pipe with the
inside diameter slightly larger
than the shaft diameter can
work well to press the
rotational assembly into
position. Once the seal
assembly is in position, place
the spring over the register
on the rotational portion
of the seal.
2. Thread the impeller onto the
shaft, making sure that the seal
spring is registered properly
onto the back side of the
impeller. Place the proper
Loctite fluid on the impeller
retaining nut. Tighten nut
on shaft.
3. Fill the seal chamber with new
dielectric oil. An air gap of
10–15% volume must be
left for the expansion of the
oil when it is at operating
temperature.
4. The motor and impeller
assembly can be installed into
the volute, making sure that
the units are aligned properly.
Install the volute retaining
bolts and tighten.
5. Air tends to trap in the pump
case when water rises in the
sump or when the pump is
lowered into the water after
service. To vent off this air, a
small hole is drilled into the
volute casting. Be sure this
vent hole is clean after any
service work on pump. Air
venting is not a problem after
initial start.
Содержание SPX50
Страница 8: ...8 Pump Wiring Diagrams ...
Страница 9: ...9 Pump Wiring Schematic WIRING SCHEMATIC FOR 230V 1Ø SIMPLEX SYSTEM ...
Страница 10: ...10 Performance Curves ...