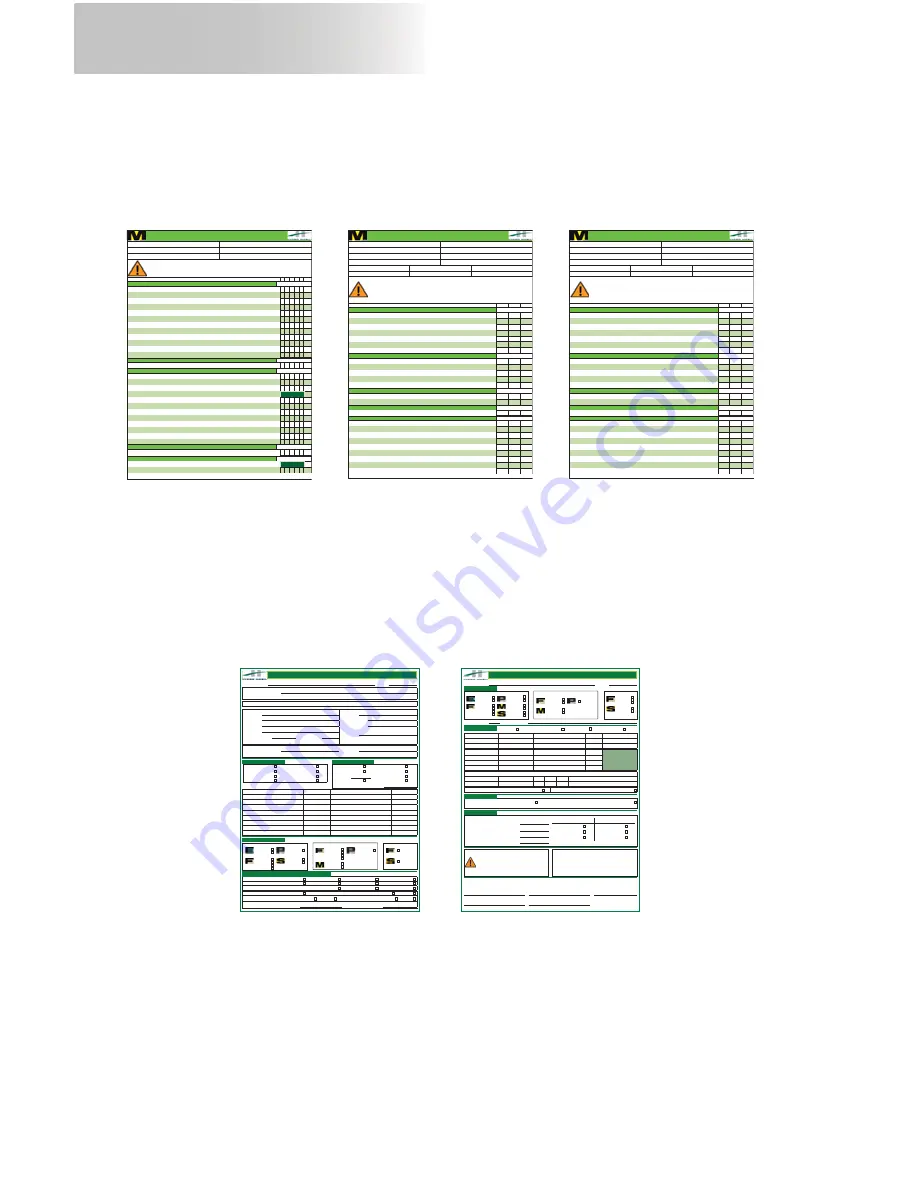
124
fi g. 8.19
fi g. 8.20
fi g. 8.21
fi g. 8.22
fi g. 8.23
8 - T
RANSPORT
, S
TORAGE
AND
M
AINTENANCE
Copies of inspection and maintenance checklists shown below can be obtained by contacting
the distributor/service center or the Hydro Mobile technical support team or downloaded
directly from the Hydro Mobile website at www.hydro-mobile.com.
Inspections and Maintenance
WEEK
1
USE CHECK MARK FOR EACH ENTRY VERIFIED. IF NECESSARY, TAKE CORRECTIVE ACTION BEFORE INSERTING CHECK MARK.
PROJECT:
COMPETENT PERSON (full name):
Each Hydro Mobile motorized unit and its accessories must be inspected daily or before every working shift, as well as weekly. Use the spaces below to monitor 6 days of
the daily and weekly inspections of an M2 Series motorized unit and its accessories. Use the Notes and Comments form to indicate any discrepancy or any item found to
be not acceptable. Any discrepancy must be reported and appropriate corrective action must be taken immediately. Corrective actions must be performed by qualified
personnel.
LOCATION:
CONTRACTOR:
MOTORIZED UNIT SERIAL NUMBER:
DATE (WEEK OF):
2
3
4
5
DAILY INSPECTION CHECKLIST
M2 SERIES
MOTORIZED UNITS and ACCESSORIES
SERIAL NUMBER (if applicable):
ACCESS and SAFETY
All access panels are clear of material and equipment.
All safety guardrails are in position and doors are operational (no fall hazard).
An evacuation plan specific to the job site is available to all workers and a legible copy of the owner’s manual is in the tool box.
Construction traffic is controlled on and around job site (proper barriers installed).
If the work platform is accessed from inside the building or off a scaffold stair tower, transfer is safe and free from obstruction.
Mast climbing is not impeded in any way and access walkway is clear of debris and working properly.
Minimum clearance from overhead power lines is maintained according to local regulation.
On special façade shapes, cross box kits, face guardrails and plank guardrails are properly installed and secure.
Perimeter of setup is safe and delimited (warning tape, concrete blocks).
Setup and installation meet the requirements prescribed by owner’s manual or approved engineering drawing.
The platform clears all obstacles (building, balconies, etc.) and can be raised or lowered.
Work and circulation areas on the platform are clear of any obstruction.
SERIAL NUMBER (if applicable):
BASE
Base is level and cribbing under jacks has not moved.
SERIAL NUMBER (if applicable):
MOTORIZED UNIT – COMPONENTS
Cables and control levers have been verified and are functioning properly.
Each cylinder hook, secondary hook and lowering cam is in good condition and functioning properly.
Each cylinder, hydraulic hose and hydraulic component is free of leaks and signs of wear.
Each roller has been greased using Prolab GS1000 #28840 only. (WEEKLY)
Each roller has been verified and is in good condition.
Gasoline and engine oil levels are appropriate or have been replenished. Air filter has been verified and is in good condition or has been replaced, if necessary.
Hydraulic oil level has been verified and hydraulic tank has been replenished, if required, with oil recommended by Hydro Mobile.
Lifting mechanism is clear of debris (mortar, masonry material, etc.) and shows no signs of excessive wear.
Motorized unit structure has been inspected and shows no signs of damage or distortion.
On an electrical unit, the power cable has been inspected and shows no signs of damage. Input power is adequate and phases are in sync.
On an electrical unit, the routing of the power cable is free from obstruction and the cable recoils properly.
Rubber on each cylinder hook has been verified as described in Owner’s manual procedure and is in good condition.
SERIAL NUMBER (if applicable):
MOTORIZED UNIT – SAFETY DEVICES
Each backup safety hook has been inspected and shows no sign of engagement prior to inspection. Each safety hook is clean and can move freely. Motorized unit
must be put out of service if any safety hook is found to be defective or shows signs of having been engaged previously.
SERIAL NUMBER (if applicable):
MASTS and MAST TIES
Mast bolts are tightened at the proper torque (120 lb-ft or 163 N-m). Mast bolt washers have been replaced if bent. (WEEKLY)
Mast sections have been inspected and show no signs of damage or distortion.
Page 1 of 2
M2_MAINTDAILY_1014
M2 SERIES
MOTORIZED UNITS and ACCESSORIES
FREQUENT INSPECTION CHECKLIST
AUTHORIZED DEALER NAME and ADDRESS:
USER/OWNER NAME and ADDRESS:
NAME of AUTHORIZED TECHNICIAN:
MOTORIZED UNIT MODEL and SERIAL NUMBER:
DATE of INSPECTION:
Each Hydro Mobile motorized unit and its accessories must be submitted to a frequent inspection. Use the spaces below to monitor inspections that need to be performed
every three months. Use the Notes and Comments form to indicate any discrepancy or any item found to be not acceptable. Any discrepancy must be reported and
appropriate corrective action must be taken immediately. Corrective actions must be performed by a technician certified specifically for M2 Series motorized units and
their accessories. All inspection steps included in the daily inspection checklist must be performed before the frequent inspection steps.
It is recommended to use replacement parts manufactured by or recommended by Hydro Mobile. The use of substitution parts could not only void the warranty covering
this motorized unit and its components but cause serious damages that could lead to injury or death. It is recommended to replenish and grease components only with
fluids and lubricants recommended by Hydro Mobile.
Frequent inspections must be performed by a technician specifically certified for M2 Series motorized units and their accessories.
USE CHECK MARK FOR EACH ENTRY VERIFIED. IF NECESSARY, TAKE CORRECTIVE ACTION BEFORE INSERTING CHECK MARK.
OK
CORRECTED
N/A
SERIAL NUMBER (if applicable):
BASE
Check condition of outriggers (4x) and outrigger shims.
Check squareness and alignment of the base as per technical procedure.
Inspect base outriggers for any welding defects, damaged parts and excessive rust or corrosion.
Inspect base structure for any welding defects, damaged parts or excessive rust or corrosion (LEFT).
Inspect base structure for any welding defects, damaged parts or excessive rust or corrosion (RIGHT).
Inspect center beam for any welding defects, damaged parts or excessive rust or corrosion.
Inspect jack (4x or 8x, as applicable) gears and mechanism. Grease jack mechanism, if necessary.
SERIAL NUMBER (if applicable):
MOTORIZED UNIT STRUCTURE
Check integrity of engine access panel.
Check integrity of mast tie door and hinges (LEFT).
Check integrity of mast tie door and hinges (RIGHT).
Check integrity of walkway access door, hinges and locking mechanism.
Check motorized unit structure for any welding defects, damaged parts or excessive rust or corrosion, and any sign of distortion.
SERIAL NUMBER (if applicable):
ACCESS WALKWAY and COMPONENTS
Check access walkway structure for any welding defects, damaged parts or excessive rust or corrosion.
Check condition of safety straps.
SERIAL NUMBER (if applicable):
GAS ENGINE
Perform recommended maintenance on Honda engine as per instructions in Honda owner’s manual.
SERIAL NUMBER (if applicable):
POWER PACK and HYDRAULIC COMPONENTS
Adjust engine RPM at full throttle and idle speed as per technical procedure.
Check all hydraulic hoses and fittings for any leaks or signs of wear.
Check choke actuation.
Check condition and adjustment of hydraulic control cable.
Check condition and adjustment of hydraulic control lever.
Check condition of the hydraulic return filter and replace, if necessary.
Check electrical connection to the engine starter switch.
Check electrical wiring and connections.
Check engine control rods.
Page 1 of 3
M2_MAINTFREQ_1014
M2 SERIES
MOTORIZED UNITS and ACCESSORIES
ANNUAL INSPECTION CHECKLIST
AUTHORIZED DEALER NAME and ADDRESS:
USER/OWNER NAME and ADDRESS:
NAME of AUTHORIZED TECHNICIAN:
MOTORIZED UNIT MODEL and SERIAL NUMBER:
DATE of INSPECTION:
Each Hydro Mobile motorized unit and its accessories must be submitted to an annual inspection. Use the spaces below to monitor inspections that need to be performed
every year. Use the Notes and Comments form to indicate any discrepancy or any item found to be not acceptable. Any discrepancy must be reported and appropriate
corrective action must be taken immediately. Corrective actions must be performed by a technician certified specifically for M2 Series motorized units and their
accessories.
It is recommended to use replacement parts manufactured by or recommended by Hydro Mobile. The use of substitution parts could not only void the warranty covering
this motorized unit and its components but cause serious damages that could lead to injury or death. It is recommended to replenish and grease components only with
fluids and lubricants recommended by Hydro Mobile.
Annual inspections must be performed by a technician specifically certified for M2 Series motorized units and their accessories.
USE CHECK MARK FOR EACH ENTRY VERIFIED. IF NECESSARY, TAKE CORRECTIVE ACTION BEFORE INSERTING CHECK MARK.
OK
CORRECTED
N/A
SERIAL NUMBER (if applicable):
BASE
Check condition of outriggers (4x) and outrigger shims.
Check squareness and alignment of the base as per technical procedure.
Inspect base outriggers for any welding defects, damaged parts and excessive rust or corrosion.
Inspect base structure for any welding defects, damaged parts or excessive rust or corrosion (RIGHT).
Inspect base structure for any welding defects, damaged parts or excessive rust or corrosion (LEFT).
Inspect center beam for any welding defects, damaged parts or excessive rust or corrosion.
Inspect jack (4x or 8x, as applicable) gears and mechanism. Grease jack mechanism, if necessary.
SERIAL NUMBER (if applicable):
MOTORIZED UNIT STRUCTURE
Check integrity of engine access panel.
Check integrity of mast tie door and hinges (LEFT).
Check integrity of mast tie door and hinges (RIGHT).
Check integrity of walkway access door, hinges and locking mechanism.
Check motorized unit structure for any welding defects, damaged parts or excessive rust or corrosion, and any sign of distortion.
SERIAL NUMBER (if applicable):
ACCESS WALKWAY and COMPONENTS
Check access walkway structure for any welding defects, damaged parts or excessive rust or corrosion.
Check condition of safety straps.
SERIAL NUMBER (if applicable):
GAS ENGINE
Perform recommended maintenance on Honda engine as per instructions in Honda owner’s manual.
SERIAL NUMBER (if applicable):
POWER PACK and HYDRAULIC COMPONENTS
Adjust engine RPM at full throttle and idle speed as per technical procedure.
Check all hydraulic hoses and fittings for any leaks or signs of wear.
Check choke actuation.
Check condition and adjustment of hydraulic control cable.
Check condition and adjustment of hydraulic control lever.
Check electrical connection to the engine starter switch.
Check electrical wiring and connections.
Check engine control rods.
Check gasoline level. Replenish, if necessary.
Page 1 of 3
M2_MAINTANNUAL_1014
Copies of the job survey checklist and the handover checklist shown below can be obtained
by contacting the distributor/service center or the Hydro Mobile technical support team or
downloaded directly from the Hydro Mobile website at www.hydro-mobile.com.
Daily inspection checklist
Frequent inspection checklist
Annual inspection checklist
F300 – 460V
F200 – 460V
F300 – 600V
F200 – 600V
F300 – 460V
F200 – 460V
F300 – 600V
F200 – 600V
240V
400V
230V
400V
Power pack
bridge
24' (7,3 m)
14' (4,3 m)
Crane available for
Erecting
Repositioning
Dismantling
Loading / unloading
Forklift available for
Erecting
Repositioning
Dismantling
Loading / unloading
Installation to be erected / dismantled by
Hydro Mobile
Hydro Rents
Dealer
Installation to be erected / dismantled by user
User installers are appropriately qualifi ed
YES
NO
Erector / dismantler training required
YES
NO
User / operator training required
YES
NO
Number of E&D training attendees
Number of U/O training attendees
JOB SURVEY – JOB HAZARD ANALYSIS
Project Name:
Date:
Series to be used for project
ELECTRIC-POWERED
GAS-POWERED
TRANSPORT PLATFORM
Project address
City
State/Province
Estimated start date
Estimated duration
WEEKS
Company
Contact
Address
Contact phone
Contact email
City
Notes
State/Province
Zip/Postal code
Phone
Fax
General contractor
Contact
Phone
Contact phone
Brick
Roofi ng
Block / stone
Material only
Stucco
Personnel / material
Glazing
Other
Scope of work
Steel frame
Wood frame
Concrete
Post tension cables
psi
Balcony slab
Load bearing masonry
Other
(specify)
Building / structure details
Height of building
FT
M
Number of bearing bridges
Number of motor units
Maximum cantilever length
FT
M
Number of repositions
Outrigger support
Number of hoists
Length of planking
FT
M
Number of swivel bridges
Number of MPIs or planked corner returns
Required capacity
LB
KG
Counterweight required
Total mast height
FT
M
Number of ties per mast (if tied)
Distance between tie levels
FT
M
Type of anchors (if tied)
Height of fi rst tie level
FT
M
Max travel distance above last tie level
MAST(S)
Available services and training levels
HMJAJHA0315
F300 – 480V
F200 – 480V
F300 – 600V
F200 – 600V
F300
F200
480V
600V
240V
400V
Power pack
bridge – 480V
24' (7,3 m)
14' (4,3 m)
240V
400V
480V
600V
240V
400V
Power pack
bridge – 600V
Single unit
Multiple units
(bearing bridge)
Freestanding
With mast ties
INSTALLATION HANDOVER SHEET
Project Name:
Date:
Number of units:
Serial numbers:
Series used for project
ELECTRIC-POWERED
GAS-POWERED
TRANSPORT PLATFORM
WARNING
To ensure safety at all times on a mast climbing work platform system,
bridges should not be loaded beyond their maximum rated weight capacities.
In addition, to prevent a mast climbing work platform system from stalling
because of an overload, maximum rated load capacities of the motorized
unit(s) should be observed. Overloading a mast climbing work platform
system could result in serious injury or death.
It is mandatory to refer to the load capacity charts located on the motorized
unit and included in the owner’s manual at all times.
NOTE
All assembly and operation instructions located on motorized units and bridges take precedence over information
contained in this manual. Should there be any discrepancies discovered throughout any published documentation
issued by Hydro Mobile or its authorized affi liates, the following order of precedence shall prevail:
1.
Written documents issued by the Hydro Mobile Engineering department
2. Recall
instructions
3.
Assembly or operation instructions displayed on the motorized unit
4. Owner's
manual
Any use of one or several Hydro Mobile motorized units, with or without accessories, in such a confi guration
or manner as not explicitly described in this manual is not allowed without the permission of Hydro Mobile Inc.
Progressive installation
If setup will be installed progressively, skip ties and anchors information
section
Complete installation
Mast ties must be installed to the top of the installation before the start of any
work
Method of installation
Ties and anchors
Maximum height
FT
M
Height of fi rst tie level
FT
M
Distance between tie levels
FT
M
Number of mast sections above last tie level
Anchor type
Shelf angle
Mechanical expansion
Welded
Mechanical screw
Drilled
Chemical / resin
Brick anchor
Details of installation
This motorized unit installation has been assembled following Hydro Mobile’s instructions and complies with applicable local regulations. The motorized unit(s)
and its (their) accessories have been submitted to all steps included in the daily inspection checklist recommended for Hydro Mobile motorized units and their
accessories. The installation has been tested and handed over in a fully functional, safe condition. This installation cannot be re-confi gured in any way without
the owner’s permission.
Installer signature
Installer name (IN PRINT)
Date of installation
Cantilever bridges
Length
Composition
No. planks Counterweight
Left cantilever
FT
M
LB
KG
Right cantilever
FT
M
LB
KG
Bearing bridge(s)
Length
Composition
No. planks
Bridge 1
FT
M
Bridge 2
FT
M
Bridge 3
FT
M
Length of corner returns
Left
FT
M
O
M
S
(Circle
O
for Outriggers,
M
for MPI or
S
for Swivel Bridge)
Right
FT
M
O
M
S
(Circle
O
for Outriggers,
M
for MPI or
S
for Swivel Bridge)
HMHS0315
Owner signature
Owner name (IN PRINT)
GAS-POWERED
Load capacities must be compliant with Owner’s manual
Load capacities must be compliant with approved layout