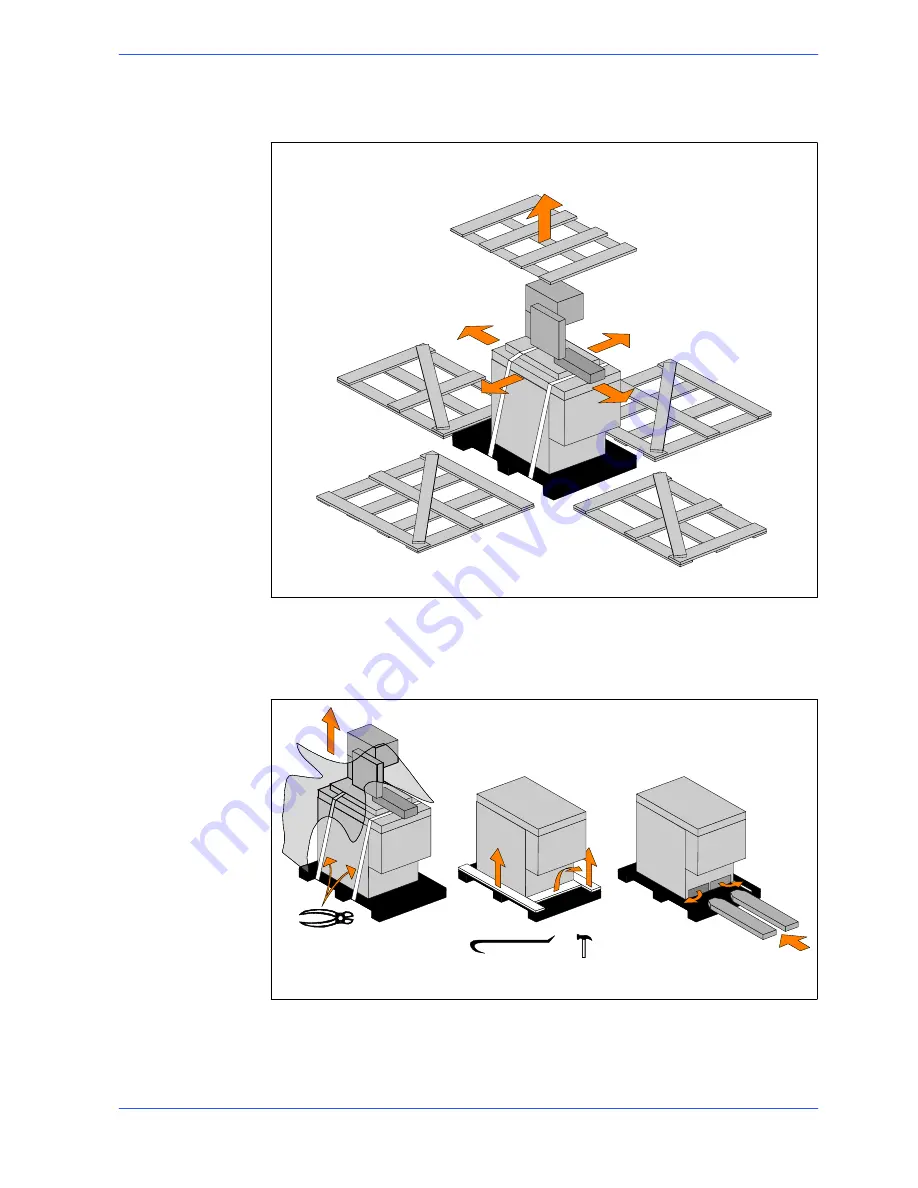
4--3
19
Machine installation
1. remove nails and lift the top of the cage;
2. remove nails and lower walls;
2
2
2
2
1
3. remove heat---shrink covering;
4. remove the straps;
5. remove nails from pallet securing planks and remove planks;
6. remove the front panel and insert fork tines.
3
4
5
6
To locate the machine in the workplace,
the machine dimensions
and necessary
operator working space, including
the spaces laid
down in safety standards,
must
be taken into account.
Содержание PH 211
Страница 1: ...EN YEAR OF MANUFACTURE ______________ PH 211 USE AND MAINTENANCE MANUAL ...
Страница 2: ......
Страница 6: ......
Страница 40: ...6 2 34 Use and maintenance manual PH211 Standardised Wiring Diagrams HB single phase ...
Страница 41: ...6 3 35 Diagrams exploded views and replace Standardised Wiring Diagrams three phase ...
Страница 44: ...6 6 38 Use and maintenance manual PH211 Motor assembly Handle assembly ...
Страница 46: ...6 8 40 Use and maintenance manual PH211 Blade adjustable assembly rear Blade adjustable assembly front ...
Страница 48: ...6 10 42 Use and maintenance manual PH211 Idler wheel and Drive wheel assembly Blade back cover assembly ...
Страница 50: ...6 12 44 Use and maintenance manual PH211 Control panel assembly ...
Страница 52: ...6 14 46 Use and maintenance manual PH211 Base assembly ...
Страница 54: ...6 16 48 Use and maintenance manual PH211 Vise assembly A Vise assembly B PH 211 ...
Страница 56: ...6 18 50 Use and maintenance manual PH211 Stand leg assembly ...
Страница 58: ......
Страница 72: ......
Страница 97: ......
Страница 98: ......