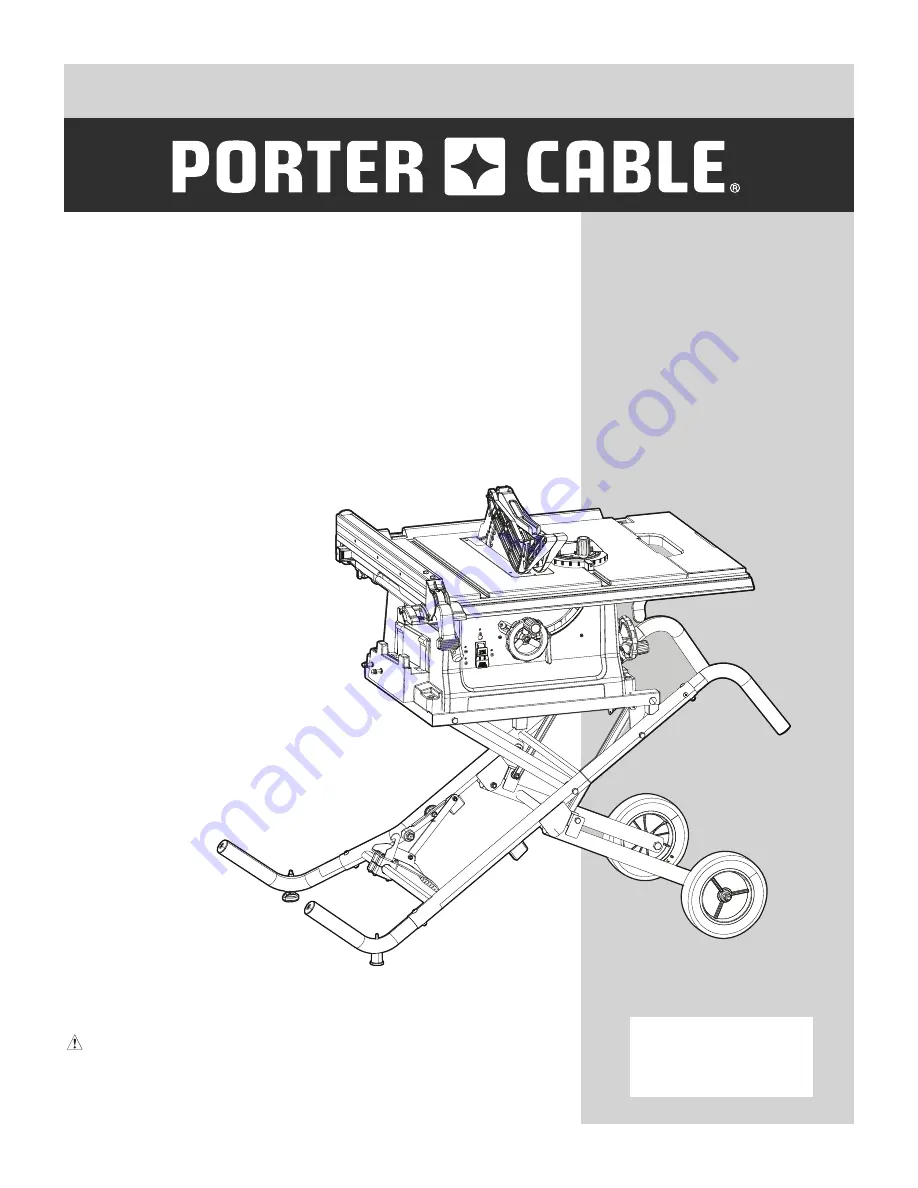
10 IN. (254 mm)
JOBSITE TABLE SAW
ScIE cIrcuLAIrE dE 254 mm
(10 pO) Sur LE LIEu dE TrAvAIL
SIErrA dE mESA dE 254 mm
(10 puLg.) pArA LA OBrA
cATALOg NumBEr
pcB222TS
Instruction manual
Manuel d’instructions
Manual de instrucciones
www.portercable.com
INSTRUCTIVO DE OPERACIÓN, CENTROS DE
SERVICIO Y PÓLIZA DE GARANTÍA.
AdvErTENcIA:
LÉASE ESTE INSTRUCTIVO
ANTES DE USAR EL PRODUCTO.