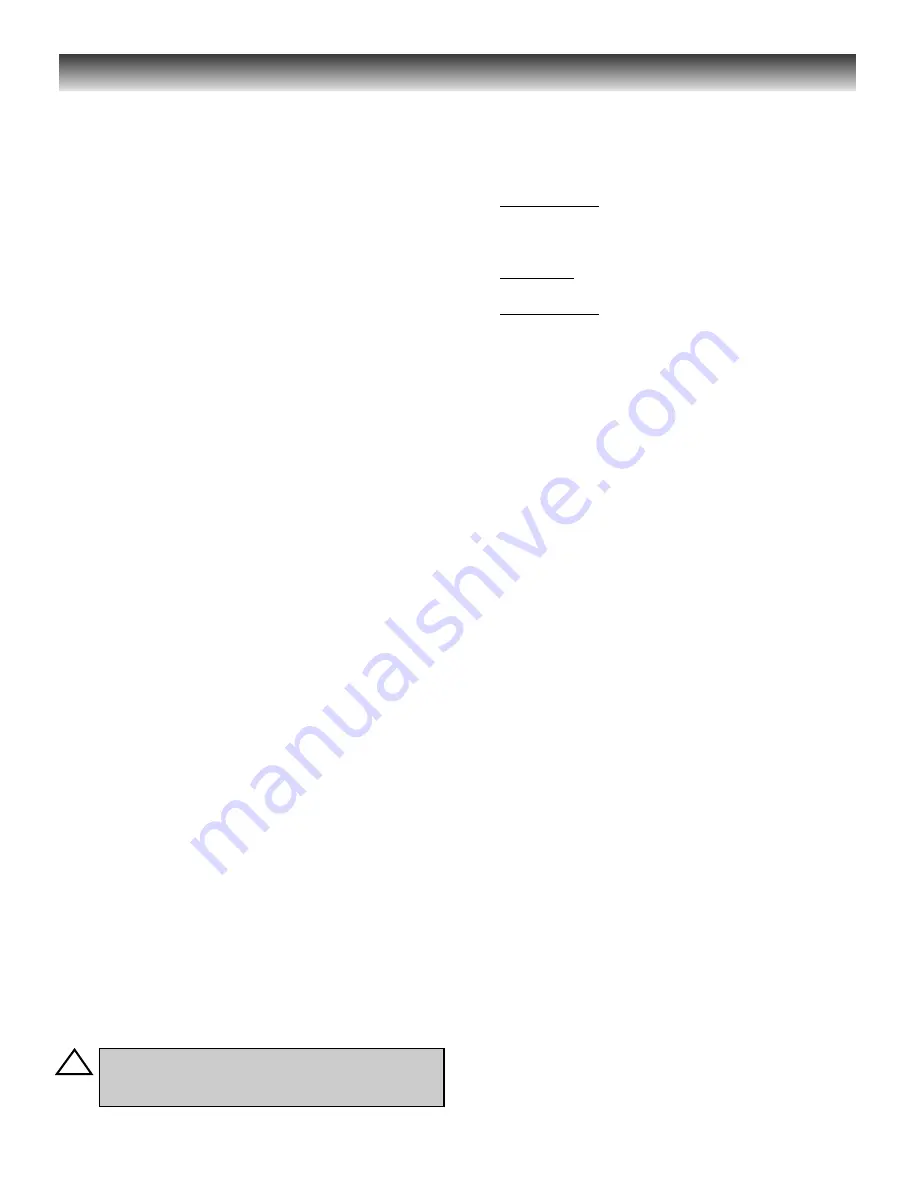
MODEL 244/244OS TOOL
HUCK FASTENERS
8
The Model 244/244OS Installation Tool is shipped with a
plastic plug in the air inlet connector. The connector has
1/4-18 female pipe threads to accept the air hose fitting.
Quick disconnect fittings and 1/4” inside diameter air hose
(1) are recommended. An air supply of 90-100 psi capable
of 6.3 CFM must be available. Air supply should be
equipped with a filter-regulator-lubricator unit.
1. Remove plastic shipping plug from Air Inlet Connector
and put in a few drops of Automatic Transmission
Fluid, DEXRON III, or equivalent.
2. Screw quick disconnect fitting into Air Inlet Connector.
CAUTION:
Do not use TEFLON tape on threads - - use
TEFLON in stick form only.
(Huck P/N 503237)
3. Set air pressure on regulator to 90-100 psi.
4. Attach optional Air Hose (Huck part number 115436),
supplied with tool, to air inlet connector.
5. Connect air hose to tool.
6. Cycle tool a few times by depressing and releasing
trigger.
7. Disconnect air hose from tool.
8. Remove Retaining Nut and Stop.
(244Only)
9. Select proper Nose Assembly from
SELECTION
CHART
for fastener to be installed.
10.
244OS Model:
Set stroke required for Nose Assembly selected. Refer
to Adjust Stroke section of this manual for adjustment
procedure
(Fig 11)
.
11. 244 Model:
Attach Nose Assembly per Nose Assembly Data Sheet.
244OS Model:
Attach nose assembly per instructions on page 21
of this manual (Fig 12).
12. Connect air hose to tool and install fastener(s) in test
plate of proper thickness with proper size holes.
Inspect fastener(s).
NOTES:
1 Air quick disconnect fittings and air hoses are not
available from Huck International, Inc.
2 On old style nose assemblies with lock collars,
VIBRA-
TITE
should be used on collet threads, since there is
no staking hole provided on the 244 pull piston. Refer
to nose assembly data sheets.
P
REPARATION FOR
U
SE
G
ENERAL
1. The efficiency and life of any tool depends upon proper
maintenance. Regular inspection and correction of
minor problems will keep tool operating efficiently and
prevent downtime. The tool should be serviced by
personnel who are thoroughly familiar with how it
operates.
2. A clean, well lit area should be available for servicing
the tool. Special care must be taken to prevent
contamination of pneumatic and hydraulic systems.
3. Proper hand tools, both standard and special, must be
available.
4. All parts must be handled carefully and examined for
damage or wear. Always replace Seals, when tool is
disassembled for any reason. Components should be
disassembled and assembled in a straight line without
bending, cocking, or undue force. Disassembly and
assembly procedures outlined in this manual should
be followed.
5.
Service Parts Kit 244KIT
includes consumable parts and
should be available at all times. Other components,
as experience dictates, should also be available.
D
AILY
1. If a Filter-Regulator-Lubricator unit is not being used,
uncouple air disconnects and put a few drops of
Automatic Transmission Fluid or light oil into the air
inlet of the tool. If the tool is in continuous use, put a
few drops of oil in every two to three hours.
2. Bleed the air line to clear it of accumulated dirt or water
before connecting air hose to the tool.
3. Check all hoses and couplings for damage or air leaks,
tighten or replace if necessary.
4. Check the tool for damage or air/hydraulic leaks,
tighten or replace if necessary.
5. Check the nose assembly for tightness or damage,
tighten or replace if necessary.
6. Check oil level in tool reservoir, replenish if necessary.
W
EEKLY
1. Disassemble and clean nose assemblies and
reassemble per applicable NOSE ASSEMBLY DATA
SHEET.
2. Check the tool and all connecting parts for damage or
oil/air leaks, tighten or replace if necessary.
S
ERVICING THE TOOL
!
WARNING: Inspect tool for damage or wear
before each use. Do not operate if damaged or
worn, as severe personal injury may occur