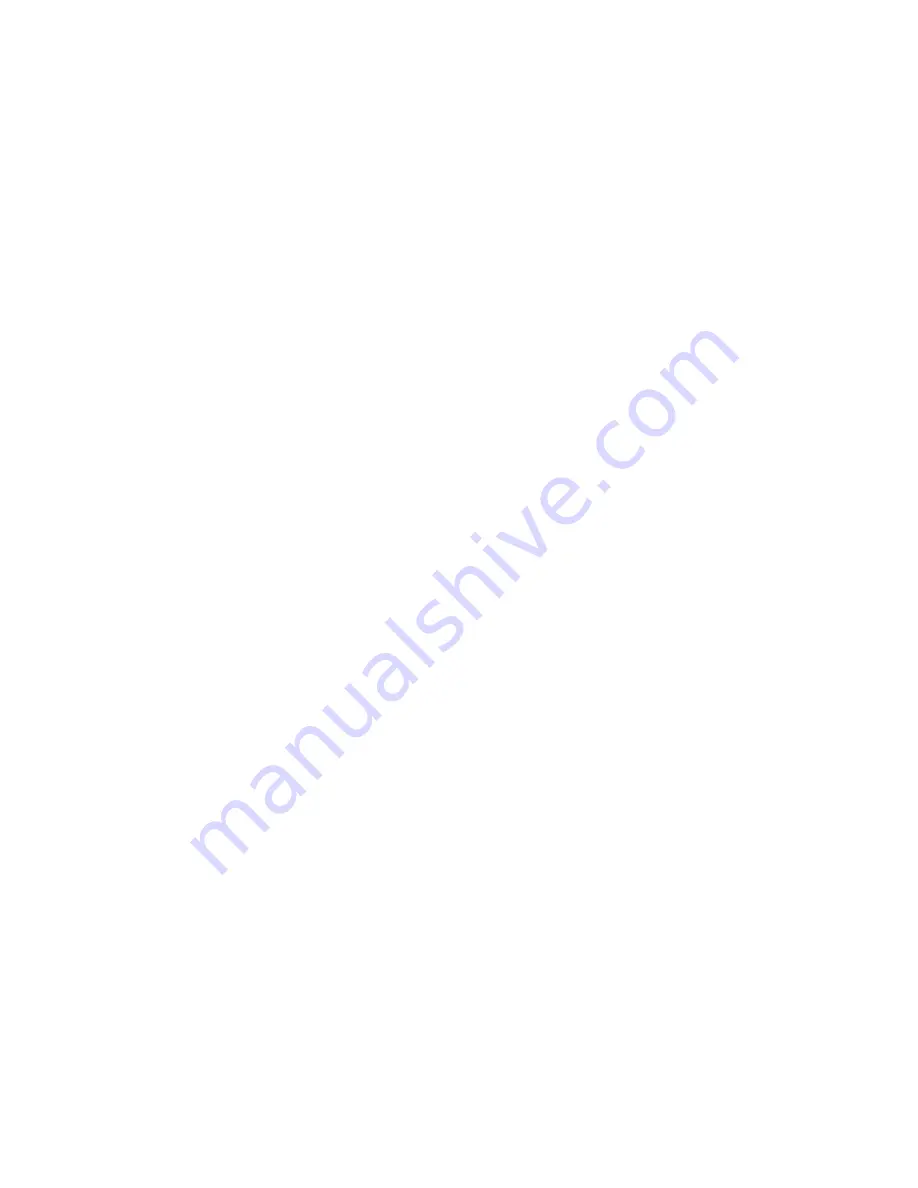
14
Please see the instructions that came with your aluminum wire for shielding gas flow rates and CTWD. A good gas flow
rate starting point for welding aluminum is about 40-50 CFH, but ultimately depends on wire diameter, nozzle shape,
nozzle size, etc. A good CTWD starting point for welding aluminum is about 3/4” to 1”. The pinch function needs to be
set no higher than 75 to prevent burn backs.
Pro Tip: We suggest starting out at 25 and then work your way up in
increments of five or ten until the ball at the end of the wire is cut off when you stop welding.
More pinch than that is
not necessary. The harder the wire and the larger the diameter of the wire, the more pinch you will need. Pinch for steel
wire is usually set at 100. To fill the crater at the end of the weld, slope down (t2) time may be set (a slope down time
between 2.5 and 4 seconds should suffice, but again, this number depends on the material thickness and the type of filler
wire used).
Everybody knows that aluminum is supposed to be preheated before welding. However, there are a few situations in
which preheating the material is not possible, practical, or safe. If you choose to not preheat the part(s) that you are
welding, for whatever reason, there is a hot start function built into the Pro Pulse 300 that will reduce the effects of
starting an aluminum MIG weld on a cold part.
Hot Start and Crater Fill in MIG 2T
The hot start function boosts the welding current by approximately 30% above the selected settings. As the chosen
settings reach 300 amps, the hot start setting tapers automatically because the machine is only capable of putting out a
maximum of 320 amps in MIG welding mode. The MIG 2T hot start function is a time-controlled application, and the
same hot start time occurs every time you pull the trigger when hot start is set. To select a hot start time from 0.2 to 4
seconds in the MIG 2T start menu, please follow the instructions below:
Set the start speed between 90% and 100% and the start time to 0.1 seconds for
NO
hot start. These settings still give
you 0.2 seconds of hot start time. In reality, however, this is the amount of time it takes to ignite the arc so you will
not notice any effects of hot start.
Set the start time to 2 seconds to get 4 seconds of hot start time. During the first 2 seconds, you will get 30% hot start.
During the following 2 seconds (seconds 3 and 4), you will get hot start tapering down from +30% to the selected
welding current.
You can activate the crater fill function through the t2 slope down setting. When you release the trigger with t2 slop down
set, the machine continues to weld (wire keeps coming out) for the amount of time you selected in the t2 setting. For
example, when you set slope down to 4 seconds, the wire continues to feed out of the gun while the settings automatically
lower (slope down) to fill the end crater. Depending on the alloy of the wire used, 5000 series wire works better than 4000
series wire, along with the material thickness and temperature, the slope down time may need to be adjusted.
Hot Start and Crater Fill in MIG 4T
In MIG 4T, you can set hot start from 10% to 90% over the selected settings. Another available feature is the base (final)
current function that you can select for better crater fill. The base current is a percentage of the welding current that you
choose. The welding current results from the wire speed and the voltage (material thickness) selected (the welding
amperage shown in the display is an estimation, which varies slightly by the distance of the MIG gun to the work surface
and the shielding gas flow rate). Nevertheless, the base current is a percentage of that amperage. This does not mean,
however, that the base current is a percentage of the wire speed or the voltage, but a percentage of the estimated
amperage.
To activate hot start and slope down in MIG 4T, please follow the instructions below (you fully control, with no time
limit, hot-start and base current through trigger motion in MIG 4T):
Pull and hold the trigger; the selected percentage of hot start is activated.
Release the trigger; the selected settings run, the arc stays lit, and welding is in progress.
Pull and hold the trigger; the machine initiates the slope down sequence and fills the crater at the end of the weld.
Once the slope down timer runs out, the welding current switches to the selected base current.
Содержание Pro Pulse 300
Страница 6: ...6 Fig 1...
Страница 8: ...8...
Страница 31: ...31 Pro Pulse 300 Wiring Diagram...
Страница 32: ...32 Pro Pulse 300 Parts Diagram...