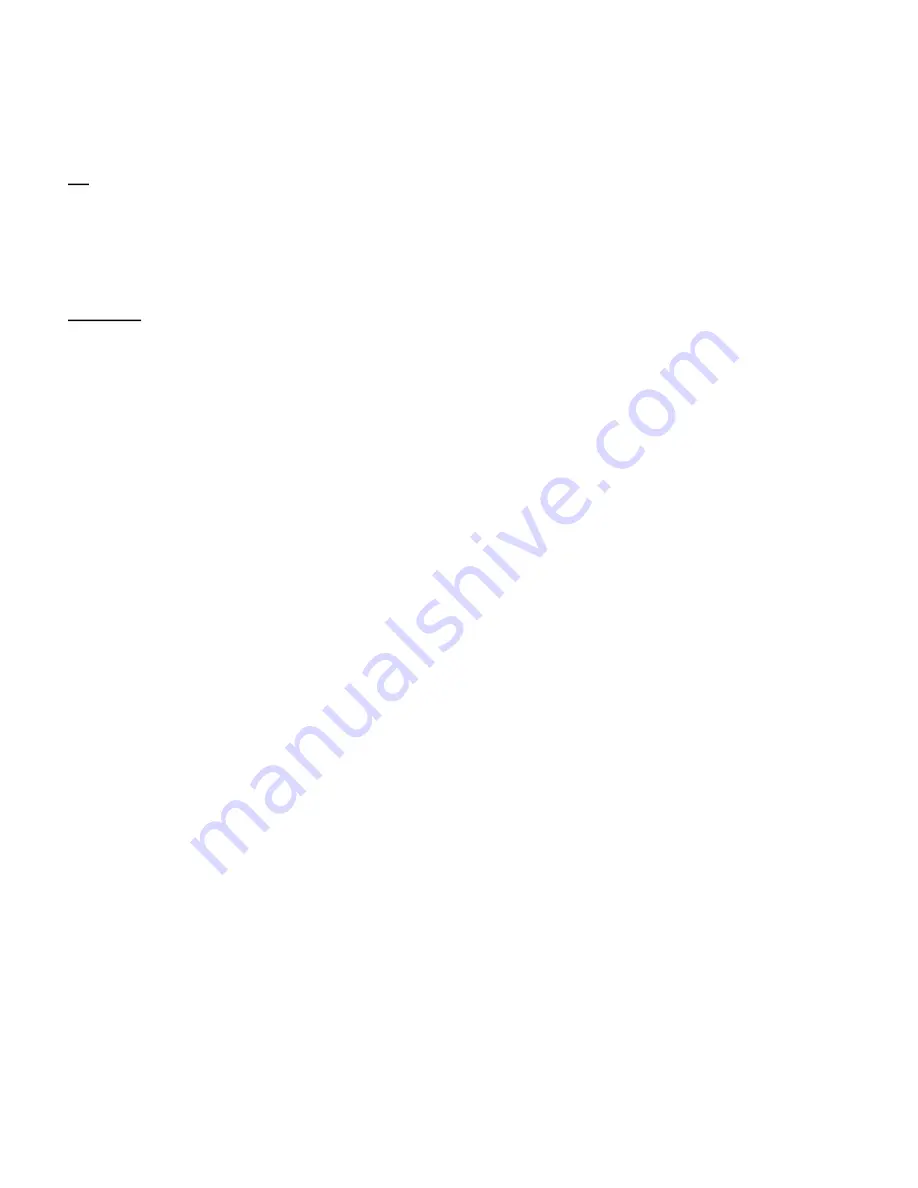
26
Important Things to Know about the JOB Mode
When you receive the Pro Pulse 300, the machine
includes some preprogrammed JOBs (typically, slots 20-
29). However, you can delete the preprogrammed JOBs,
as well as the JOBs you saved on the machine. To delete
all
saved J OBs, press and release the JOB button
C
,
and then press and hold the Select Mode button
A
and
button
E
at the same time for approximately five (
5
)
seconds. After hearing five (
5
) beeps, all JOBs,
including the preprogrammed demo JOBs, will be
permanently erased from the machine’s memory.
When saving a JOB, please note that the machine saves
everything
, which means not just wire speed,
material thickness, and voltage, but also any voltage
corrections you make, if you made the weld in 2T or 4T
mode, induction (when and where applicable), run-in
speed and time (or hot start), burn back, pinch, pre– and
post-flow gas, t2 slope down (when and where
applicable), etc. For different JOBs, these settings can
and will be different, and, as you recall each JOB, the
JOBs will load with the exact settings used when you
saved them.
Why is the JOB Mode Important and How Do You Use
It?
We will illustrate the importance of the JOB mode and
explain how you use it with an example (more
particularly, with an example of using the JOB mode, as
well as the Trigger JOB Function). Let’s say you weld
with a lot of mild steel. You may choose to save two or
three JOBs with your favorite or most often used wire
diameter in the first three memory slots. To access each
of your three most often used JOBs, you simply need to
pull the trigger (see
Trigger JOB Function
on page 23)
to switch from one JOB to the next. Regarding the JOBs
themselves, for example, you could set up the first JOB
based on the actual material thickness you are welding
(for flat work or in-position welding). Then, you could
set up the second JOB for vertical welding (so the
parameters would be slightly cooler than JOB #1).
Lastly, you could set up a third JOB as a stitch weld
function to more easily fill gaps on less than perfect fit
up.
Pro Tips:
If you program a JOB for stainless steel, we
suggest using a long post-flow time (5 to 10
seconds) to shield the weld.
If you program a JOB for aluminum, we
recommend setting the pinch low to prevent burn
backs. Also, set the t2 slope down between 2.5 and
5 seconds to fill the crater at the end of the weld.
Remote Control Option
The Pro Pulse 300 features a remote control (foot pedal
or hand control) option for MIG welding. The unique
feature of using a remote control for MIG welding
allows you to change settings (material thickness = wire
speed + voltage) while welding—giving you 100%
control, 100% of the time. If, for instance, you encounter
a section of poor fit-up when welding and need to lower
the setting of the machine to bridge the gap, you can do
so with a simple movement of the remote control.
The remote control feature is especially handy when
welding aluminum because it allows you to adjust hot
start as much as or as little as and for as long as or as
short as you want. The properties and weld-ability of
aluminum change dramatically with increased heat so
bridging gaps on poor fit-up can be difficult. However,
the remote control feature makes welding aluminum, in
every thickness and temperature range and with good or
poor fit-up, a breeze.
Содержание Pro Pulse 300
Страница 6: ...6 Fig 1...
Страница 8: ...8...
Страница 31: ...31 Pro Pulse 300 Wiring Diagram...
Страница 32: ...32 Pro Pulse 300 Parts Diagram...