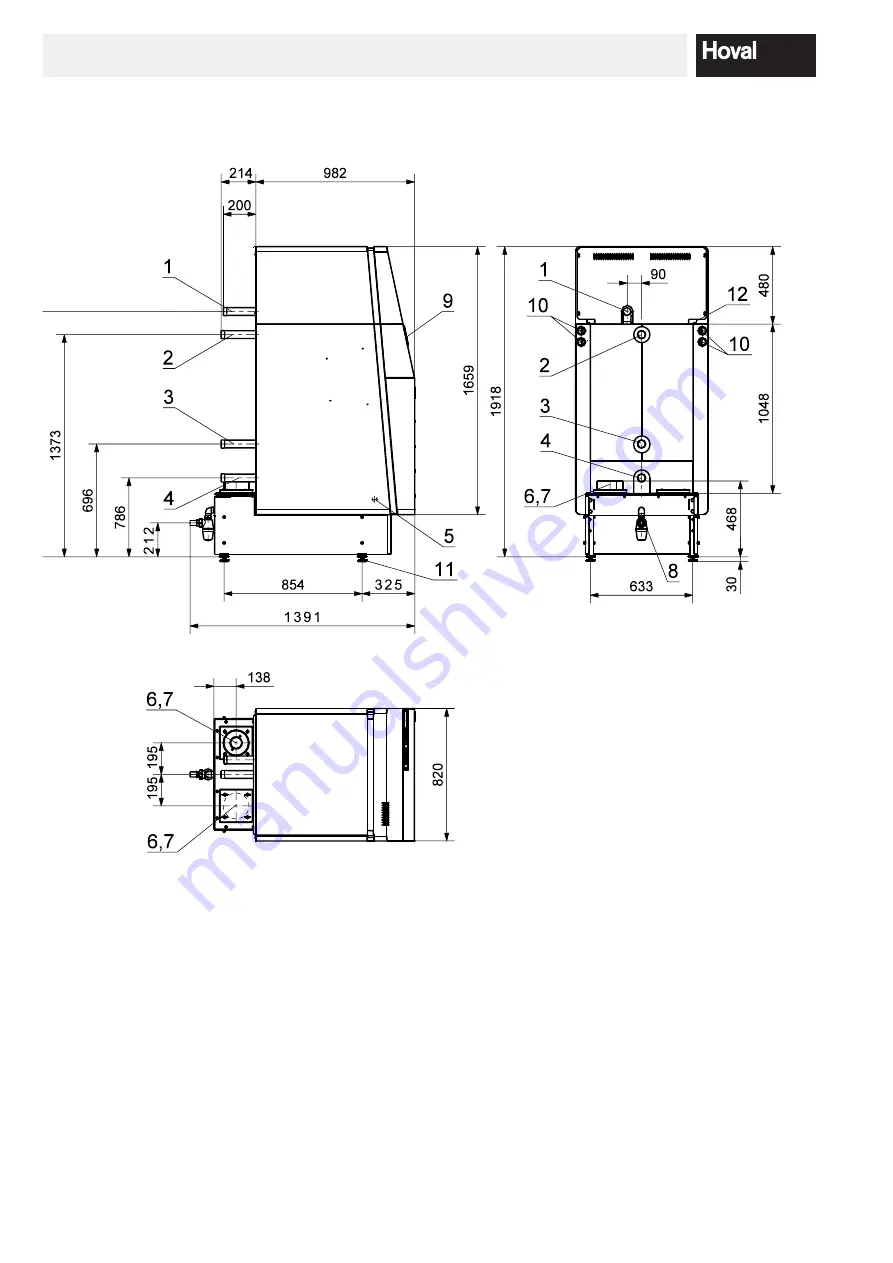
18
3.3
Dimensions UltraOil
®
(65,80)
(All dimensions in mm)
Fig. 24
1
Safety flow R1½"
2
Flow heating/calorifier R1½"
3
Return flow, high temperature R1½"
4
Return flow, low temperature R1½"
5
Draining ½"
6
Flue gas outlet inner Ø 155 mm
7
Cleaning aperture Ø 155 mm
8 Condensate drain incl. syphon DN25
9 Control panel
10 Electric cable infeed
11
Boiler feet adjustable 20-80 mm
12
Lead-through for oil pipe on left or right side
4 213 787 / 01
TECHnICAL DETAILS
Содержание UltraOil 65
Страница 43: ...43 4 213 787 01...