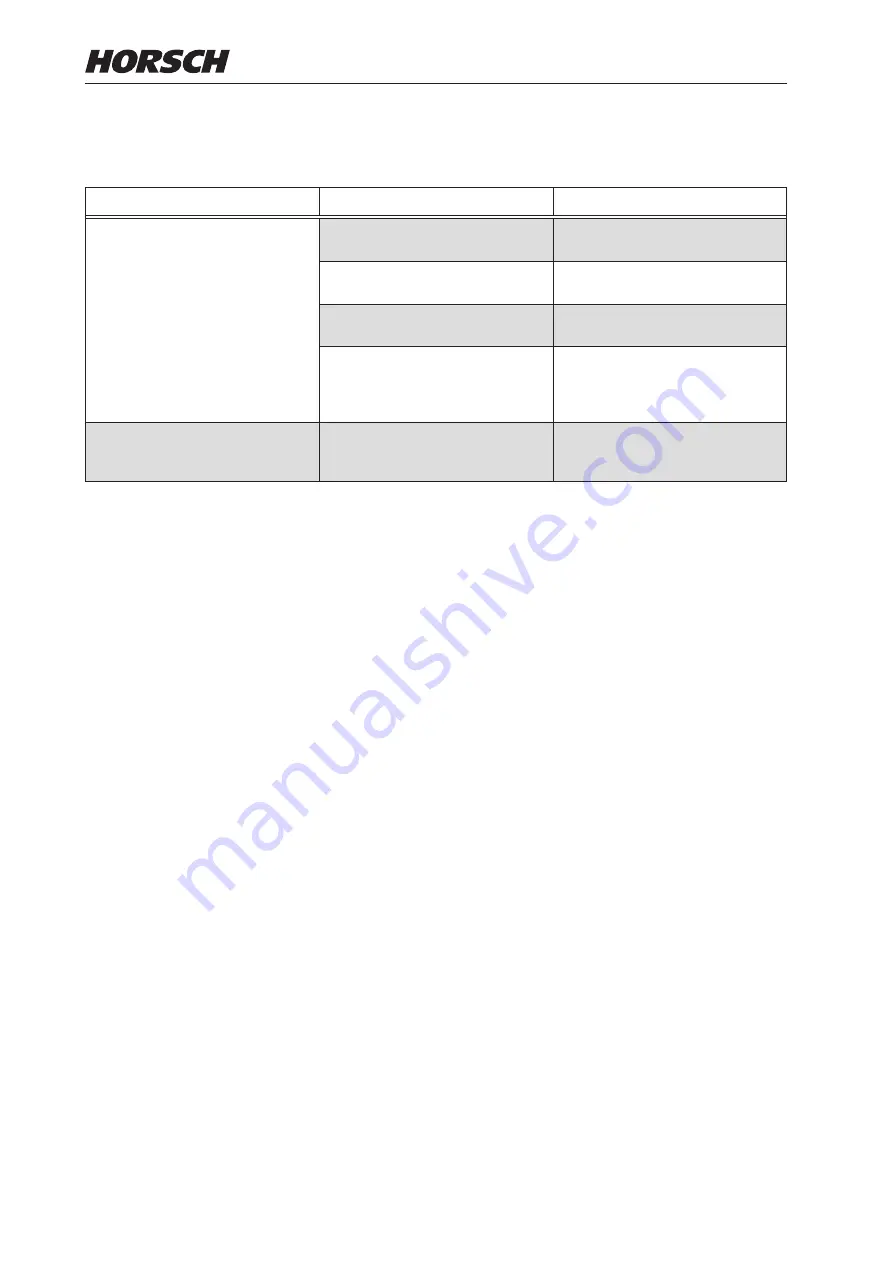
Troubleshooting
Fault
Possible cause
Remedy
The placing quantity is too low.
The sealing lip in the metering unit
is worn.
Replace the sealing lip.
The placing quantity is set too low.
Check the adjustment on the
terminal and correct as required.
The pressurized hopper of twin
hopper machines is leaking.
Check the hopper for leak tightness
and replace the seals if necessary.
The pneumatic system is leaking.
Check the distributor and all
pneumatic hoses for leak tightness.
Replace the respective components
if necessary.
Sporadic skipping of work signal.
The control unit on the tractor is not
set correctly.
Switch the control unit on the tractor
to the floating position when working
in the field.
106
MF
Содержание Pronto 3 - 6 DC
Страница 2: ......
Страница 5: ......
Страница 20: ...Keep sufficient safety distance to the slewing range of the machine 00381117 16 ...
Страница 128: ......