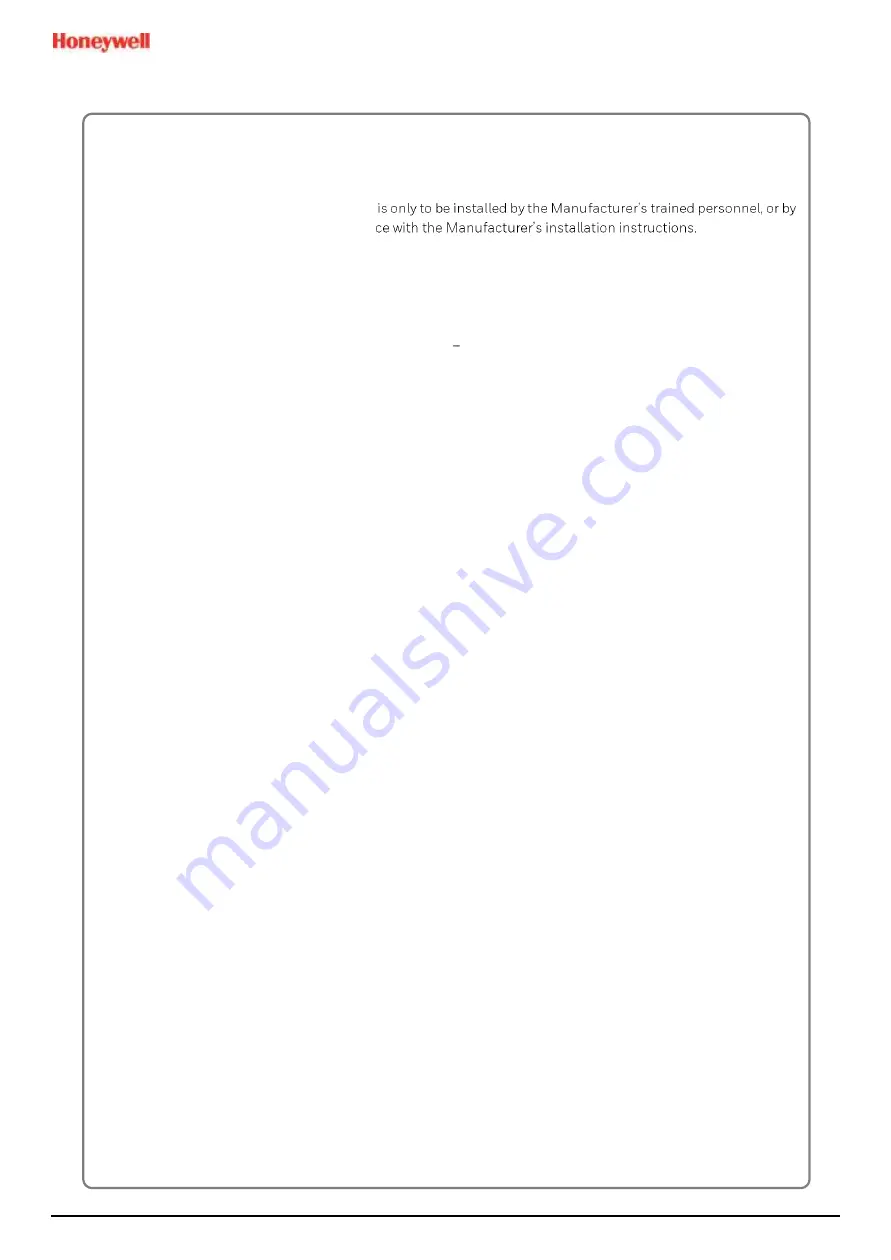
MAN0984_Iss 4_01/19
Touchpoint Plus
Pt. No. 3011M5001
10
Technical Handbook
1.4
TPPL General Warnings
1)
HIGH OFF-SCALE READINGS MAY INDICATE AN EXPLOSIVE CONCENTRATION
2)
ONLY THE COMBUSTIBLE GAS DETECTION PORTION OF THIS INSTRUMENT HAS BEEN ASSESSED FOR
PERFORMANCE PER CSA C22.2 No.152.
3)
The equipment specified in this manual
competent persons trained in accordan
4)
Installation must be in accordance with the recognized standards of the appropriate authority in the country
concerned. Refer to local, national and company regulations.
5)
Do not operate the Touchpoint Plus system or its components outside of their rated operating specification.
6)
Touchpoint Plus must not be operated in Oxygen enriched atmospheres, i.e. greater than 25% v/v Oxygen.
7)
All equipment containing a User Interface must be suitably protected from direct sunlight and rain.
8)
Power Supply Fluctuations are not to exceed DC 18 32 V SELV Supply or ±10 % of nominal.
9)
All versions of Enclosure apparatus are electrical Class 1, and must be connected to Protective Earth
(Ground).
10)
The Touchpoint Plus installation must include a means of isolating or disconnecting the input voltage
supply. The isolation or disconnection device must be conveniently located close to the system and be clearly
labelled. For an AC mains voltage supply, the isolation or disconnection device must disconnect both the
line and neutral poles, but maintain earth (ground) continuity.
11)
The Touchpoint Plus input voltage supply must include over-current protection.
12)
All cabling must be appropriately rated and approved in accordance with local, national and company
regulations, and suitable for the installation. Additionally, cabling must satisfy requirements defined in the
manuals of connected field devices, in particular if the field device is certified for use in a hazardous location.
13)
All signal cables and interconnections must be shielded and the shields terminated only at the unified earth
(ground) bus bar situated inside the enclosure
14)
All conduits and cable armour shall be bonded to protective earth (ground), and care must be taken to avoid
ground loops and to avoid contact with cable shielding.
15)
Cable entry glands, blanking plugs, reducers, adaptors and breather devices must be suitably approved and
must not reduce the IP rating or protection levels. Items should not be used if there is a high risk of
mechanical damage to the equipment or enclosure.
16)
Access doors and entry points must be kept closed when the system is energised in normal operation.
17)
The TPPL Enclosures must be securely closed and the locking handle security screws must be fully tightened
during normal operation.
18)
All equipment in this manual is rated to +2000 m (6562 ft) altitude maximum.
19)
For safety reasons this equipment must be operated by qualified personnel only. Read and understand the
Instruction Manual completely before operating or servicing the equipment.
20)
Touchpoint Plus systems may contain hazardous live terminals. Appropriate precautions should be taken
during operation, installation, and maintenance and servicing. Specifically, operators must have appropriate
training and experience to be aware of the hazards to which they may be exposed, and of measures to
minimise risk to themselves or other people.
21)
The protection provided by TPPL may be impaired or lost if the equipment is installed or used in an incorrect,
unspecified or unauthorised way.
22)
Be aware that extended exposure of a detector element to certain concentrations of combustible gases and
air can introduce stress to the element that may seriously affect its performance, and therefore recalibration
should be carried out or the sensor replaced, or both, after an alarm due to an indication of a high
concentration.
23)
When used in a Gas Detection summing up role, the gas reading may be higher than the actual
concentration at any one detector head location, or it may be the actual concentration at one specific
detector head.
24)
Exposure to some chemicals may degrade the sealing properties of materials used in the alarm relay.
25)
Do not open TPPL enclosures or disconnect/reconnect equipment until power has been isolated and the
area is made safe / non-hazardous. This includes replacing backup batteries.
26)
Substitution of any components may impair suitability for Class I, Division 2.
27)
Touchpoint Plus oxygen detection is intended for measurement of oxygen deficiency and enrichment. Do
not use for oxygen inertisation.