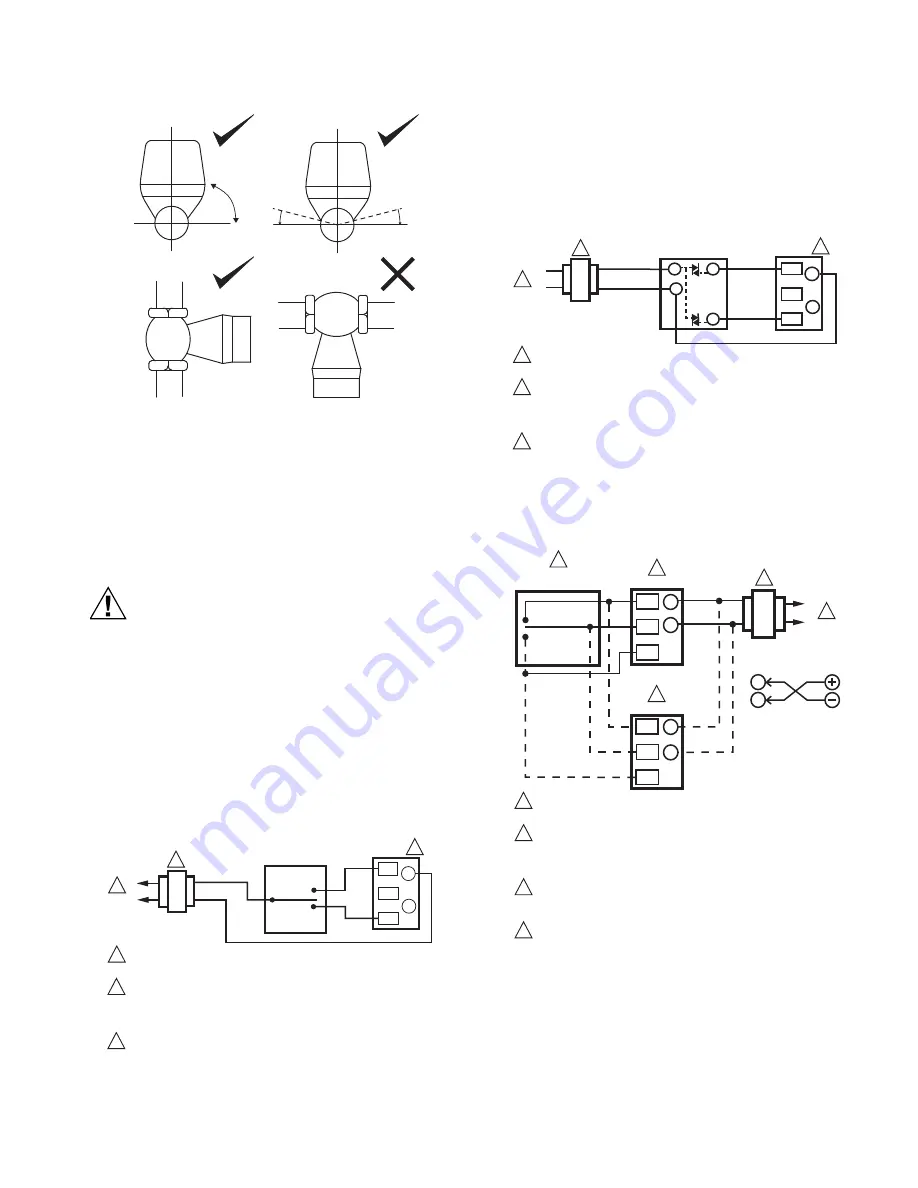
ML6984, ML7984 SERIES 4000 DIRECT COUPLED VALVE ACTUATORS
5
95C-10939—11
Fig. 7. Mounting Positions.
WIRING SCHEMATICS
MLx984 actuators are designed to operate from a Safety
Extra Low Voltage, Class II power source. A 7/8 in. (22 mm)
wiring hole is provided for attaching a flexible conduit
where required by local codes. When installing outdoors,
weatherproof conduit fittings approved for outdoor and
wet locations must be used.
CAUTION
Electrical Shock or Equipment Damage Hazard.
Can Shock Individuals or Short Equipment
Circuitry.
Disconnect power supply to the actuator to prevent
electrical shock and equipment damage, or remove
and cap the air line to the actuator.
NOTE:
In all cases when wiring multiple actuators, the
power supply to all actuators must be connected
in a “star” fashion to reduce excessive voltage
drop. DO NOT “daisy chain” i.e. connect power to
one actuator then branch to another.
Fig. 8. 3-Wire Control of ML6984 with Series 60
Controller.
Operation
The recommended valve actuator power source is a Safety
Extra-Low Voltage (SELV) Class II, 24 V transformer or
regulated 28 Vdc across terminals T5 and T6. Internal
circuitry provides dc power for the electronic sensing and
drive motor circuits.
Fig. 9. 3-Wire Control of ML6984 with Electronic
Controller.
Fig. 10. 5-Wire Control of ML6984.
Outdoor
NEMA3R
Indoor
90°
>5°
>5°
M25491
M25492A
TYPICAL ELECTRO-MECHANICAL
CONTROLLER
R
W
B
W
B
R
T6
T5
ML6984
L1
L2
24 VAC
POWER SUPPLY PROVIDES OVERLOAD PROTECTION AND DISCONNECT
MEANS.
ALLOW UP TO 0.5 AMPS FOR EACH DEVICE. ACTUATORS AND
CONTROLLER CAN SHARE SAME TRANSFORMER, PROVIDED THAT THE
VA RATING OF THE TRANSFORMER IS NOT EXCEEDED AND PROPER
PHASING IS OBSERVED. DO NOT MIX A.C. AND D.C. POWER SOURCES.
CONTROLLER CAN BE LOW VOLTAGE SPDT SERIES 20 “ON-OFF” OR
SP3T SERIES 60 “FLOATING” (TRI-STATE) TYPE. TERMINALS R AND T5
ARE CONNECTED INSIDE THE ML6984.
1
2
3
1
2
3
M25493A
3
1
3
W
R
B
T6
T5
C
H
ML6984
TYPICAL ELECTRONIC
CONTROLLER
L1
L2
POWER SUPPLY PROVIDES OVERLOAD PROTECTION AND
DISCONNECT MEANS.
ALLOW UP TO 0.5 AMPS FOR EACH DEVICE. ACTUATORS AND
CONTROLLER CAN SHARE SAME TRANSFORMER, PROVIDED THAT THE
VA RATING OF THE TRANSFORMER IS NOT EXCEEDED AND PROPER
PHASING IS OBSERVED. DO NOT MIX A.C. AND D.C. POWER SOURCES.
CONTROLLER CAN BE LOW VOLTAGE SPDT SERIES 20 “ON-OFF” OR
SP3T SERIES 60 “FLOATING” (TRI-STATE) TYPE. TERMINALS R AND T5
ARE CONNECTED INSIDE THE ML6984.
1
2
3
1
2
M25494A
W
B
R
W
W
R
R
B
B
24 VAC
T5
T5
T5
T6
T6
T6
28 VDC
OR
L1
L2
ML6984
TYPICAL SPDT
CONTROLLER
ML6984
POWER SUPPLY PROVIDES OVERLOAD PROTECTION AND DISCONNECT
MEANS.
ALLOW UP TO 0.5 AMPS FOR EACH DEVICE. ACTUATORS AND
CONTROLLER CAN SHARE SAME TRANSFORMER, PROVIDED THAT THE
VA RATING OF THE TRANSFORMER IS NOT EXCEEDED AND PROPER
PHASING IS OBSERVED. DO NOT MIX A.C. AND D.C. POWER SOURCES.
CONTROLLER CAN BE LOW VOLTAGE SPDT SERIES 20 “ON-OFF” OR
SP3T SERIES 60 “FLOATING” (TRI-STATE) TYPE. TERMINALS R AND T5
ARE CONNECTED INSIDE THE ML6984.
MULTIPLE ACTUATORS CONTROLLED BY A COMMON CONTROLLER IN
PARALLEL MUST BE WIRED SO THAT THEY ALL TRAVEL IN THE SAME
DIRECTION. REVERSE ACTING ACTUATORS WILL NOT OPERATE
RELIABLY IN COMBINATION WITH DIRECT ACTING UNITS DUE TO
GEARBOX TOLERANCES. USE ML7984 MODULATING ACTUATORS, OR
DEDICATED CONTROLLERS, OR SEPARATE CONTROLLER OUTPUTS
FOR EACH GROUP INSTEAD.
1
2
3
4
2
3
4
4
1