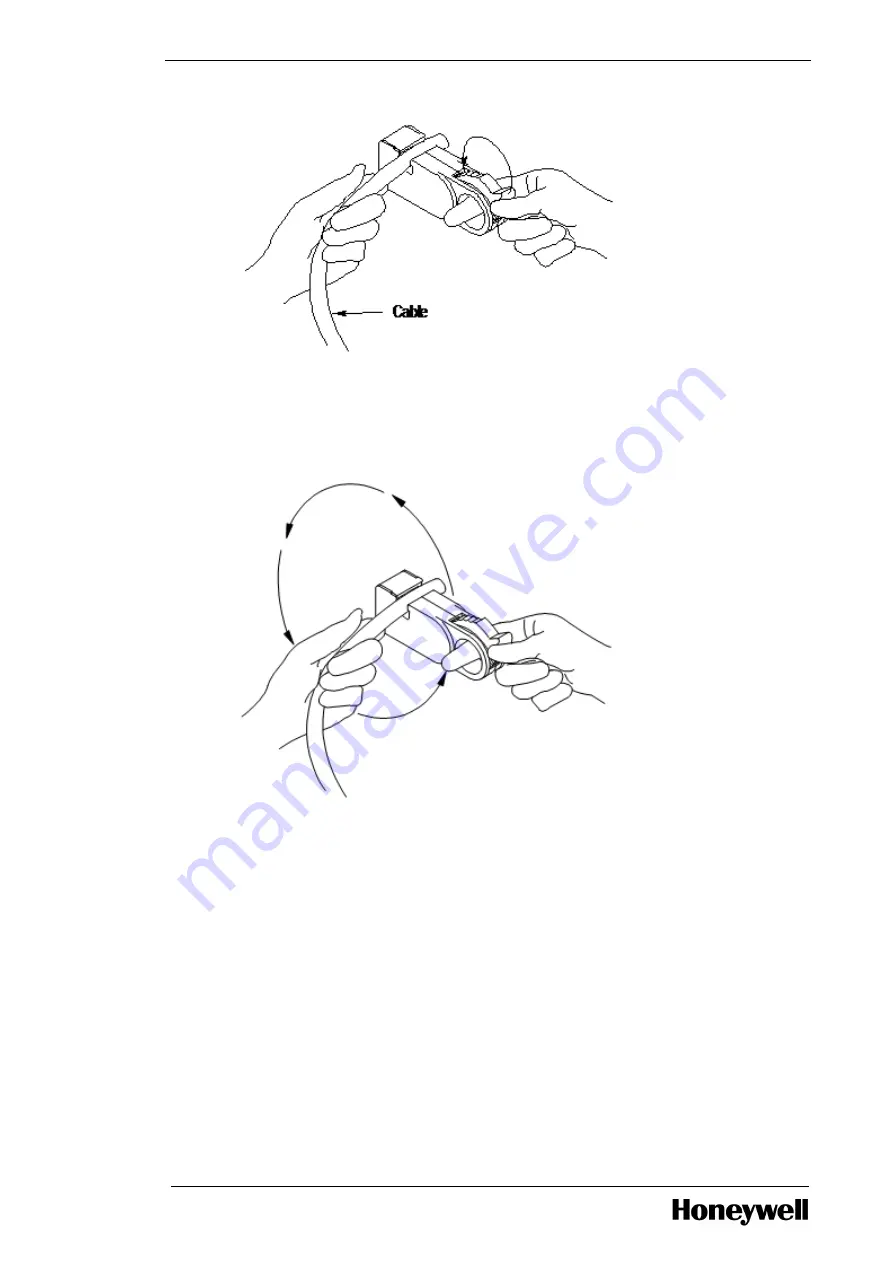
Chapter 5 - Building ControlNet Trunk Cables
4. Holding the cable in one hand, place the index finger of your other hand inside the chamber-gauge
ring. Turn the strip tool 360° around the cable. Make four or five full rotations until the strip tool
glides easily around the cable.
5. Continue repeating Steps 3 and 4, moving the chamber-gauge ring forward one notch each time
you repeat the steps until you reach the last notch. Each time you move the chamber ring forward a
notch, the strip tool makes a deeper cut into the cable. On your last repetition of Steps 3 and 4,
apply sufficient pressure on the chamber-gauge ring to ensure the ring has reached the last stage.
6. After you have moved the chamber-gauge ring to the last position and turned the strip tool the final
time, move the chamber-gauge ring backward to release the strip tool, and remove it from the
cable.
l
move the chamber-gauge ring backward to release the strip tool, and remove it from the cable.
l
strip away the appropriate portion of the cable, without using the strip tool.
l
clean the remaining cable parts from the strip chamber after each use.
- 33 -