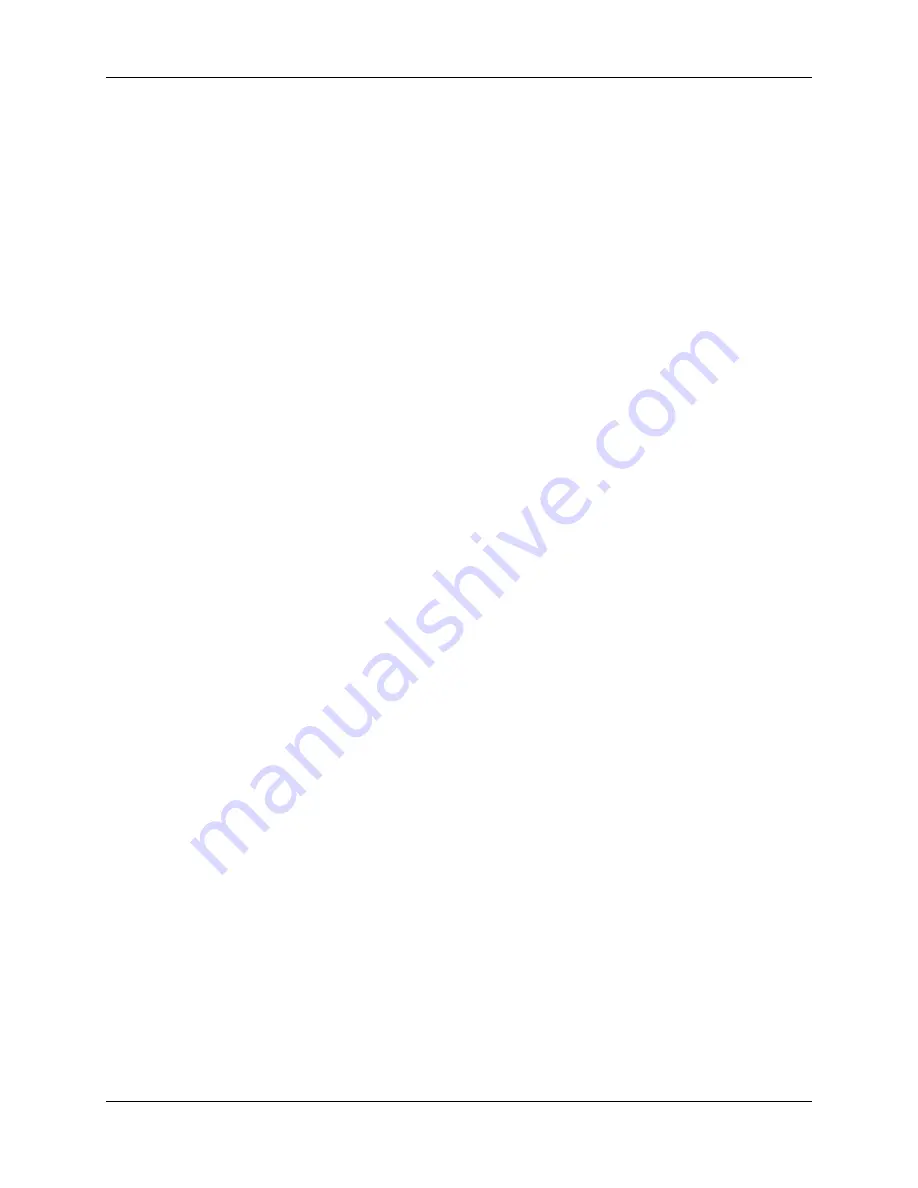
ii
UDC3300 Basic Model: DC330B User Manual
5/00
Notices and Trademarks
Copyright 2000 by Honeywell
Release 0 May, 2000
Warranty/Remedy
Honeywell warrants goods of its manufacture as being free of defective materials
and faulty workmanship. Contact your local sales office for warranty information. If
warranted goods are returned to Honeywell during the period of coverage,
Honeywell will repair or replace without charge those items it finds defective. The
foregoing is Buyer’s sole remedy and is in lieu of all other warranties, expressed
or implied, including those of merchantability and fitness for a particular
purpose. Specifications may change without notice. The information we supply is
believed to be accurate and reliable as of this printing. However, we assume no
responsibility for its use.
While we provide application assistance personally, through our literature and the
Honeywell web site, it is up to the customer to determine the suitability of the
product in the application.
Sensing and Control
Honeywell
11 West Spring Street
Freeport, IL 61032
UDC2300 is a U.S. registered trademark of Honeywell
Other brand or product names are trademarks of their respective owners.
Содержание DC3300
Страница 1: ...Sensing and Control UDC3300 Basic Model DC330B User Manual 51 52 25 78 5 00 ...
Страница 26: ...Installation 18 UDC3300 Basic Model DC330B User Manual 5 00 ...
Страница 70: ...Setpoint Rate Ramp Soak Program Operation 62 UDC3300 Basic Model DC330B User Manual 5 00 ...
Страница 72: ...Environmental and Operating Conditions 64 UDC3300 Basic Model DC330B User Manual 5 00 ...
Страница 74: ...Model Selection Guide 66 UDC3300 Basic Model DC330B User Manual 5 00 ...
Страница 80: ...Position Proportional Calibration 72 UDC3300 Basic Model DC330B User Manual 5 00 ...
Страница 82: ...Input Ranges 74 UDC3300 Basic Model DC330B User Manual 5 00 ...
Страница 83: ......