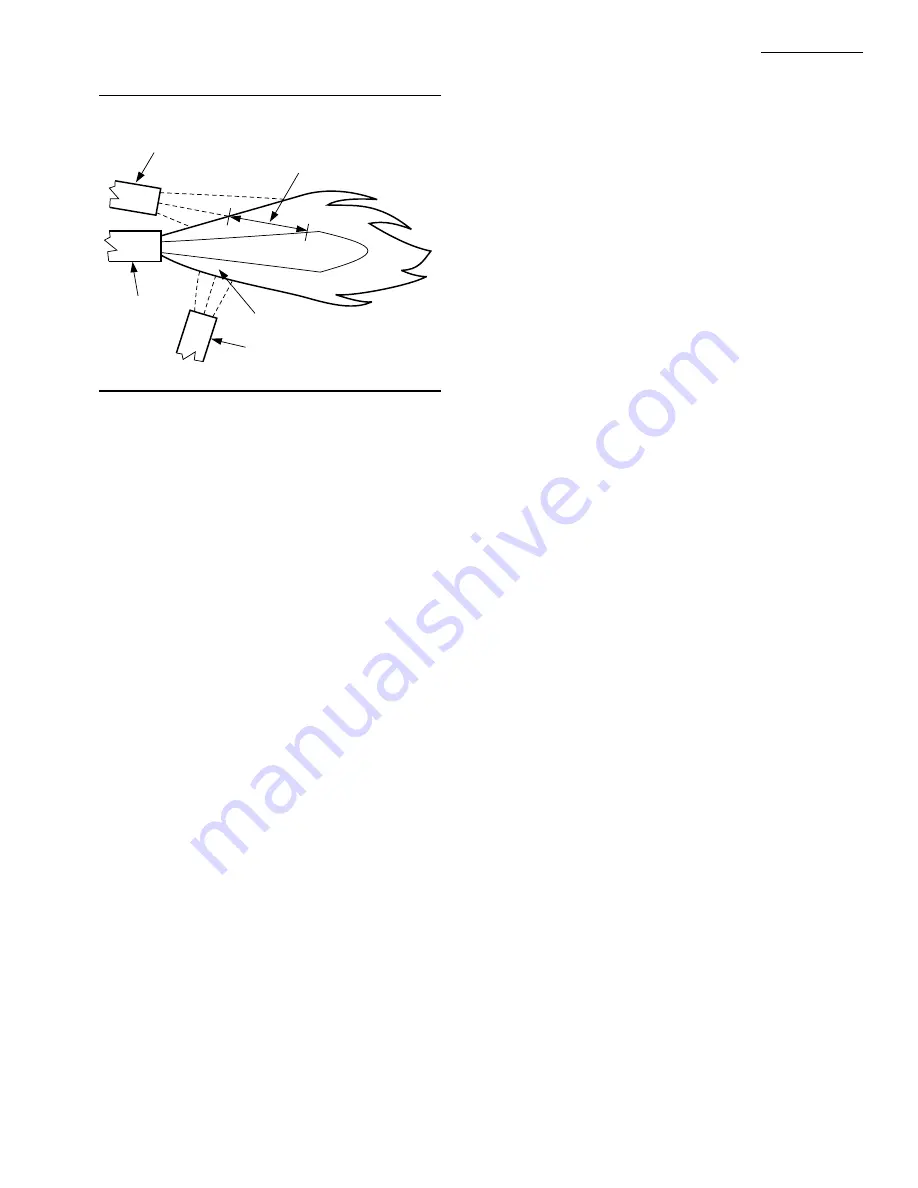
5
65-0156—1
C7024E,F
INSTALLATION
Fig. 3—Detector sighting angle.
FLAME DEPTH–
ANGLE VIEW
M1956
DETECTOR IN GOOD
SIGHTING POSITION
(LOW ANGLE SIGHTING)
UNBURNED FUEL
FLAME DEPTH–
PERPENDICULAR VIEW
BURNER
NOZZLE
DETECTOR IN POOR
SIGHTING POSITION
Low angle sighting permits the detector to view a
greater depth of flame, thus reducing the effects of
instabilities in the flame pattern. Also, the environment
near the burner nozzle is usually cleaner than at any
other part of the combustion chamber. This provides a
clearer line of sight and may keep the viewing window
cleaner, reducing the maintenance required.
NOTE: When possible, it is desirable to tilt downward
the detector and sighting pipe to prevent buildup of
soot in the pipe or on the viewing window.
In most installations, the detector will need to re-
spond to pilot flame alone, then the pilot and main
burner flame together, and finally the main burner flame
alone. The detector must meet all sighting requirements
that apply:
Pilot flame alone—the smallest pilot flame that can
be detected must be capable of reliably igniting the main
burner.
Pilot and main burner flame together—the detector
must sight the junction of both flames.
Main burner flame alone—the detector must sight the
most stable part of the flame for all firing rates.
PARALLEL FLAME DETECTORS
Shifting flame patterns, commonly encountered on
burners with high turndown ratios, may require two
parallel detectors to prove the flame at the highest and
lowest firing rates and for the modulation in between. In
this case, one detector supervises the pilot (interrupted)
and both detectors supervise the main burner flame.
During the main burner run period, either detector is
capable of maintaining system operation. A maximum
of two C7024 Detectors can be connected in parallel.
In addition to assuring more reliable flame detection,
parallel detectors facilitate maintenance during burner
operation. Each detector can be removed, in turn, with-
out shutting down the supervised burner. However, a
flame simulating failure occurring in the flame signal
amplifier or in either detector will cause a shutdown.
SCREENING EFFECTS
Smoke, oil, mist, dirt and dust are masking agents
that attenuate the ultraviolet radiation emitted by the
flame. If they absorb too much radiation, the amount of
ultraviolet radiation reaching the detector is reduced.
The flame signal then can become too low to hold in the
flame relay, resulting in burner shutdown.
The problem can be eliminated by diluting the con-
taminants. A strong flow of air through the sight pipe
will clear a viewing path through the attenuating mate-
rial. Refer to Sight Pipe Ventilation section.
It is also desirable to sight the detector at an area
containing fewer masking agents such as near the burner
nozzle or near the entrance of the combustion air. Increas-
ing the viewing area of the detector by shortening the sight
pipe or by increasing the diameter of the sight pipe also
reduces the attenuating effects of masking agents.
MULTIBURNER REQUIREMENTS
(Flame Discrimination)
In addition to meeting the requirements for a single
burner, a multiburner installation requires discrimina-
tion between flames. Flame discrimination can be de-
fined as locating all flame detectors so that each detector
responds only to the flame produced by the burner it is
supervising.
In multiple burner systems, not every detector can be
positioned so its line-of-sight does not intercept flames
from other burners. For example, this situation occurs in
front-fired boiler-furnaces having more than one row of
burners, or in multilevel opposed-fired furnaces where
the burners face each other.
When planning such an installation, locate each flame
detector so that it has the best possible view of the first
30 percent nearest the burner nozzle (flame root) it is
supervising, and the worst possible view of all other flames.
Fig. 4 illustrates a critical detector application prob-
lem that requires flame discrimination. Flame discrimi-
nation is accomplished for Detector A by repositioning
it until the flame relay (in the flame safeguard control)
does not respond to Flame B. Note that Detector A is
aimed at the first 30 percent of Flame A where the
ultraviolet radiation is most intense. It sights the tip of
Flame B, but is not aimed at the first 30 percent of Flame
B where UV is intense. Detector A is repositioned to
assure maximum response to Flame A while rejecting
Flame B. Similarly, Detector B is positioned to assure
maximum response to Flame B while rejecting Flame A.
If you reposition a detector and still cannot achieve
flame discrimination, try reducing the viewing area by
increasing the length or decreasing the diameter of the
sight pipe, or adding an orifice plate.
INSTALL THE SIGHT PIPE (See Fig. 5)
After you have determined the location and sighting
angle, select the sight pipe. A black iron pipe with a
minimum diameter of 1-1/2 in. [38.1 mm] is recom-
mended. Do not use stainless steel or galvanized pipe
because they reflect ultraviolet radiation internally and
complicate aiming the pipe.
Содержание C7024E
Страница 14: ...65 0156 1 14 ...
Страница 15: ...15 65 0156 1 ...