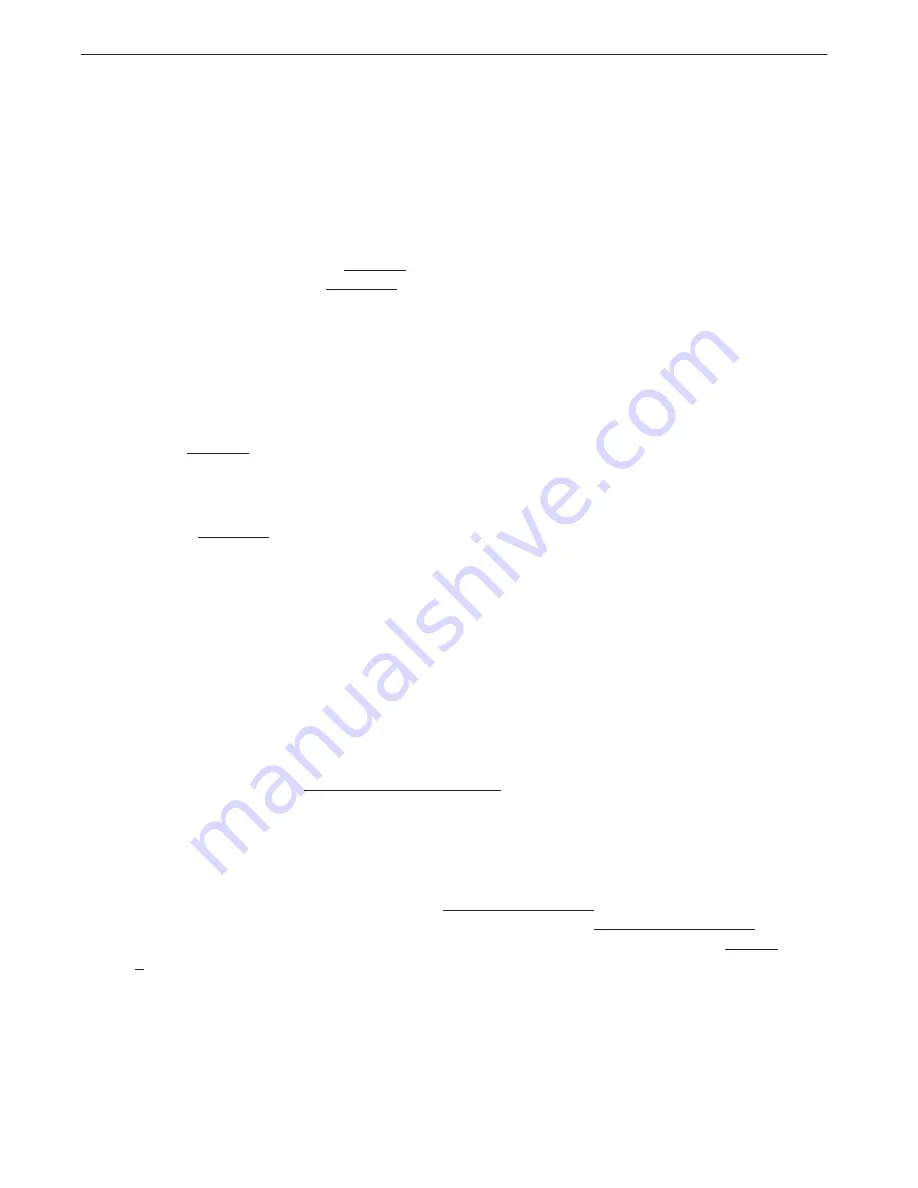
ACM 150
127
NOTE
The ACM 150 monitor’s valve cycle timing can be changed using the
configuration file. This file is to be accessed and modified only by HA, its agent
company or the user’s Authorized Service Technicians, who have been trained
or are following the instructions of HA or its agent company.
Sample valve tests
Verify that vacuum is present by observing the Sample Vacuum and the Bypass
Vacuum readings from the respective pressure transducers. At the monitor, you can
observe the vacuum LEDs,
Figure 7
, or from a remote location, observe the readings
using View Valve Cycles,
Figure 61
.
Continue to observe the Sample Vacuum as the ACM 150 monitor scans through all
of its active points. Minor fluctuations from one point to the next are normal. If you
notice a significant increase in vacuum above normal at one or more point, suspect
a flow restriction. The longest sample tube runs (from the most remote sample areas)
may always show a bump in vacuum, which is the ‘normal’ reading for that point.
The following tests are done at the monitor with the pumps running. Select the
Manual Control Mode and the Frontpanel Mode. Utilize the Sample Valve Control
Panel,
Figure 7
, and proceed:
•
Valve Test: Select one of the points, 1-40. Cycle the valve on and off. When off,
you should see a large increase in the Sample Vacuum, returning to normal when
switched on. Remote users can perform this test in the Manual Control Mode
(see
Figure 73
). Identify any valve that fails to cycle properly and service it.
•
Flow Test: With all of the sample valves off, disconnect the inlet tube fittings and
attach a flowmeter to each inlet port (a flowmeter test assembly is available from
HA service). Measure the flow rate from point to point and compare the flows to
each other and to prior tests.
NOTE
Avoid mixing sample tubes. Before disconnecting all of the tube fittings, make
sure that every sample tube is labeled with the correct ACM 150 port number.
If not labeled correctly, disconnect one tube at a time and reconnect before
moving on.
Points with flows that have changed significantly or are out of the normal range
require service as per
Servicing the cycle valves
. Too low a flow indicates a restricted
flow control orifice in the valve or a loose valve that is leaking in room air (service the
valve). Too high a flow rate indicates that the valve is leaking across its seat or that
the bypass orifice is allowing excess flow (replace the valve).
Line leak tests (optional)
If you are using the Line Leak Test, refer
Hardware servicing
and select ‘Perform an
Entire Line Leak Test’. Every point that is currently scanned (
Programmable relays
)
is included in the test. The Line Leak LED on the Sample Valve Control Panel (
Figure
7
) lights while the test is running. The test starts with point 1 and progresses in
sequence, skipping any points not in the Order of Scan, until the last point is tested.
Содержание ACM 150
Страница 1: ...ACM 150 Air Composition Monitor Guide to Installation Operation and Maintenance ...
Страница 2: ......
Страница 15: ...ACM 150 15 Figure 1 ACM 150 outside labels ...
Страница 16: ...ACM 150 16 Figure 2 ACM 150 inside labels ...
Страница 29: ...ACM 150 29 Figure 15 Relay output board ...
Страница 59: ...ACM 150 59 Figure 30 Installation diagram ...
Страница 152: ...ACM 150 152 ...
Страница 153: ......
Страница 154: ......
Страница 155: ......
Страница 156: ...ACM 150 Air Composition Monitor Revision 2 ECO HAA150063 December 2015 Honeywell Analytics ...