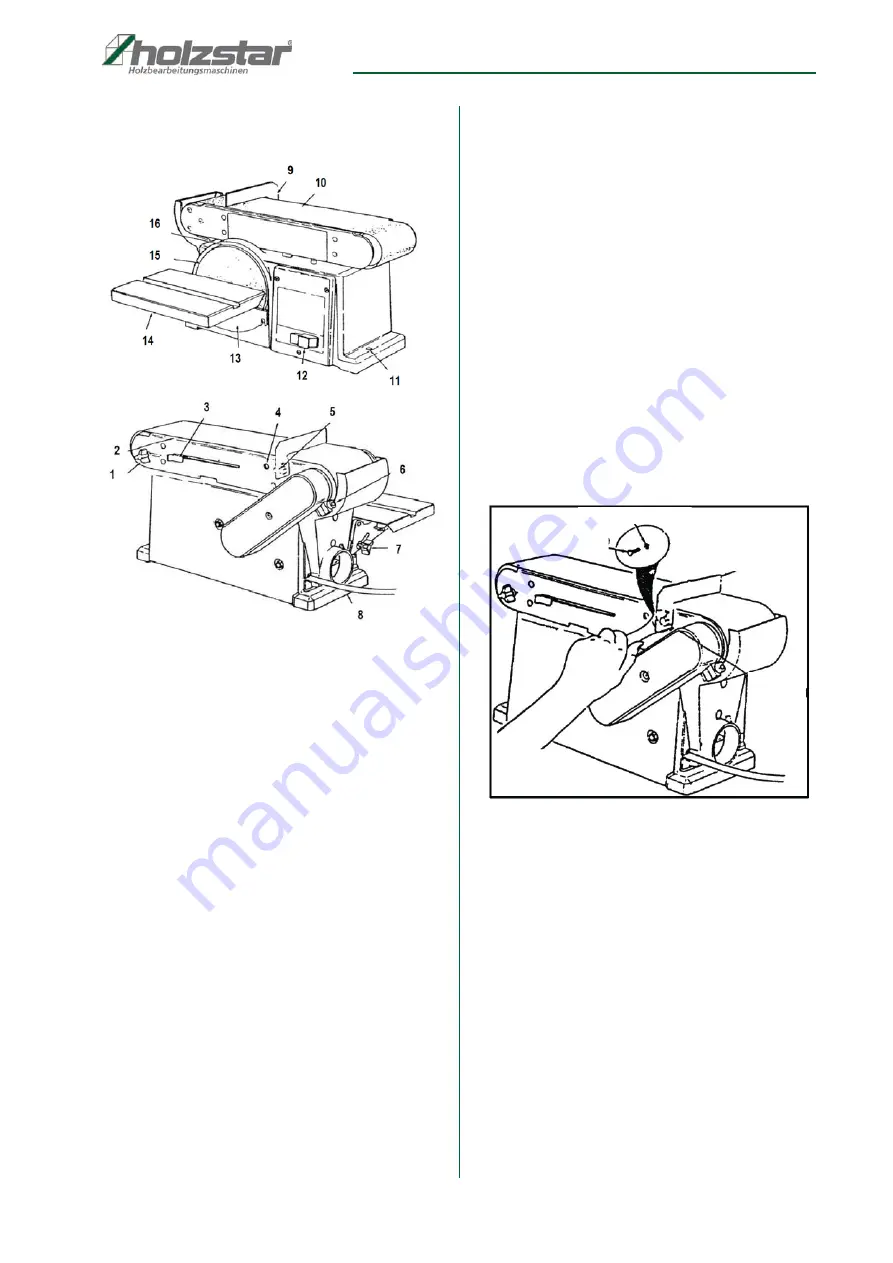
Description of the device
BTS-Series | Version 3.06
9
7
Description of the device
Fig. 3: Description
1. Track adjustment screw
2. Sanding belt board
3. Tensioning lever
4. Worktable - retaining hole
5. Mounting hole
6. Sanding unit - locking screw
7. Clamping screw - table swiveling
8. Machine foot
9. Safety stop
10. Grinding belt
11. Mounting hole
12. ON / OFF switch
13. Sanding plate protection
14. Worktable
15. Grinding wheel
16. Sanding pad
8
Assembly
Remove the machine from its packaging and remove all
protective films. Make sure that the machine is not set up
or put into operation in a damp or wet environment. The
humidity should not exceed 60% and the measured
room temperature should be between 0 ° C and 40 ° C.
For a safe footing, the machine should be mounted on a
stable base (such as a workbench) using the holes provi-
ded in the machine base.
8.1 Safety stop
Take the safety stop as shown in Fig. 4 and fix it with the
hexagon screw M6 x 1.0-14 and the toothed disc. When
tightening the screw, make sure that you fasten the
safety stop approx. 3 mm above the sanding belt. Do not
overtighten the screw, otherwise it may over-tighten.
Fig. 4: Assembly the safety stop
Screw
Safety
Stop
Lock washer
straddle
wrench
Содержание 5904150
Страница 1: ...BTS 150 Operating Instruction Belt and Disc sander BTS 150 BTS 250 ...
Страница 21: ...Notes BTS Series Version 3 06 21 18 Notes ...
Страница 22: ...www holzstar de ...