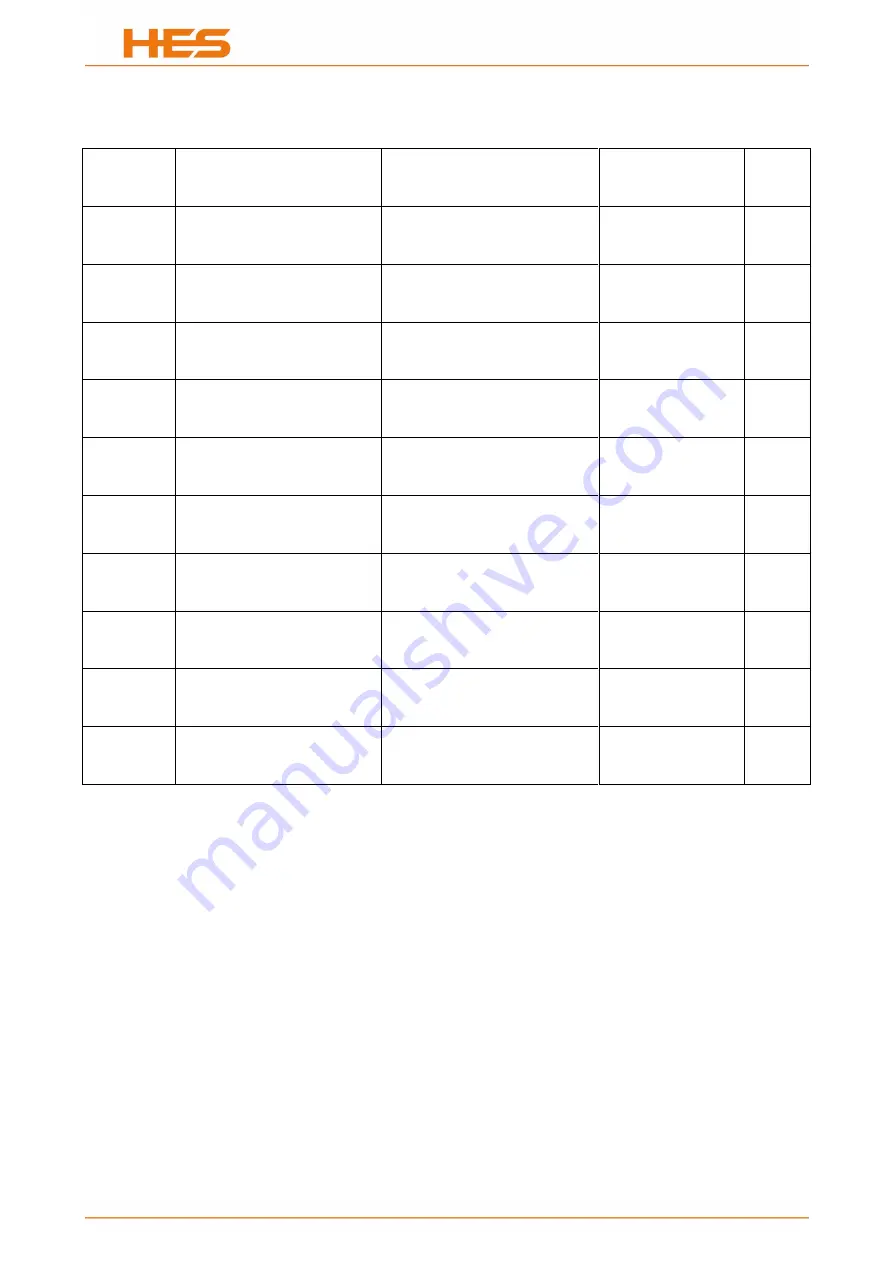
49
Hwang Sun Enterprise Co., Ltd.
49 Edition 2012/02
MODULE NO. 350E00 MANIFOLD ASSEMBLY
ITEM
SERIAL NO.
DESCRIPTION
MATERIAL
Q’TY
1
350T05-2
MANIFOLD
A6061
1
2
350EA00-1
NOZZLE
1
3
350C00
BY-PASS VALVE
1
4
350F00
FILTER ASSEMBLY
1
5
1500D01
BUSHING
A6061
1
6
OG35V
O-RING
1
7
OP16V
O-RING
1
8
ST 3/8 83B
PLUG SCREW
3
9
ST 1/8 83B
PLUG SCREW
1
10
TD0303AO
CONNECTOR
1
Содержание HS2510-N
Страница 1: ...Hwang Sun Enterprise Co Ltd 0 Edition 2012 02 00 ...
Страница 19: ...17 Hwang Sun Enterprise Co Ltd 17 Edition 2012 02 3 2 INSTRUCTIONS OF OPERATION PANEL ...
Страница 50: ...48 Hwang Sun Enterprise Co Ltd 48 Edition 2012 02 FIGURE 6 1 5 MANIFOLD ASSEMBLY ...
Страница 52: ...50 Hwang Sun Enterprise Co Ltd 50 Edition 2012 02 FIGURE 6 1 6 BY PASS VLAVE ...
Страница 54: ...52 Hwang Sun Enterprise Co Ltd 52 Edition 2012 02 FIGURE 6 1 7 FILTER ASSEMBLY ...
Страница 56: ...54 Hwang Sun Enterprise Co Ltd 54 Edition 2012 02 FIGURE 6 1 8 WIRING DIAGRAM ...
Страница 57: ...55 Hwang Sun Enterprise Co Ltd 55 Edition 2012 02 FIGURE 6 1 9 WIRING DIAGRAM ...
Страница 58: ...56 Hwang Sun Enterprise Co Ltd 56 Edition 2012 02 FIGURE 6 1 10 WIRING DIAGRAM ...
Страница 59: ...57 Hwang Sun Enterprise Co Ltd 57 Edition 2012 02 FIGURE 6 1 11 COMPONENTS WIRING CONFIGURATION ...
Страница 60: ...58 Hwang Sun Enterprise Co Ltd 58 Edition 2012 02 FIGURE 6 1 12 COMPONENTS WIRING CONFIGURATION ...
Страница 61: ...59 Hwang Sun Enterprise Co Ltd 59 Edition 2012 02 FIGURE 6 1 13 PANEL EXTERNAL WIRING CONFIGURATION ...
Страница 62: ...60 Hwang Sun Enterprise Co Ltd 60 Edition 2012 02 FIGURE 6 1 14 PARAMETER SETTING OF INVERTER ...