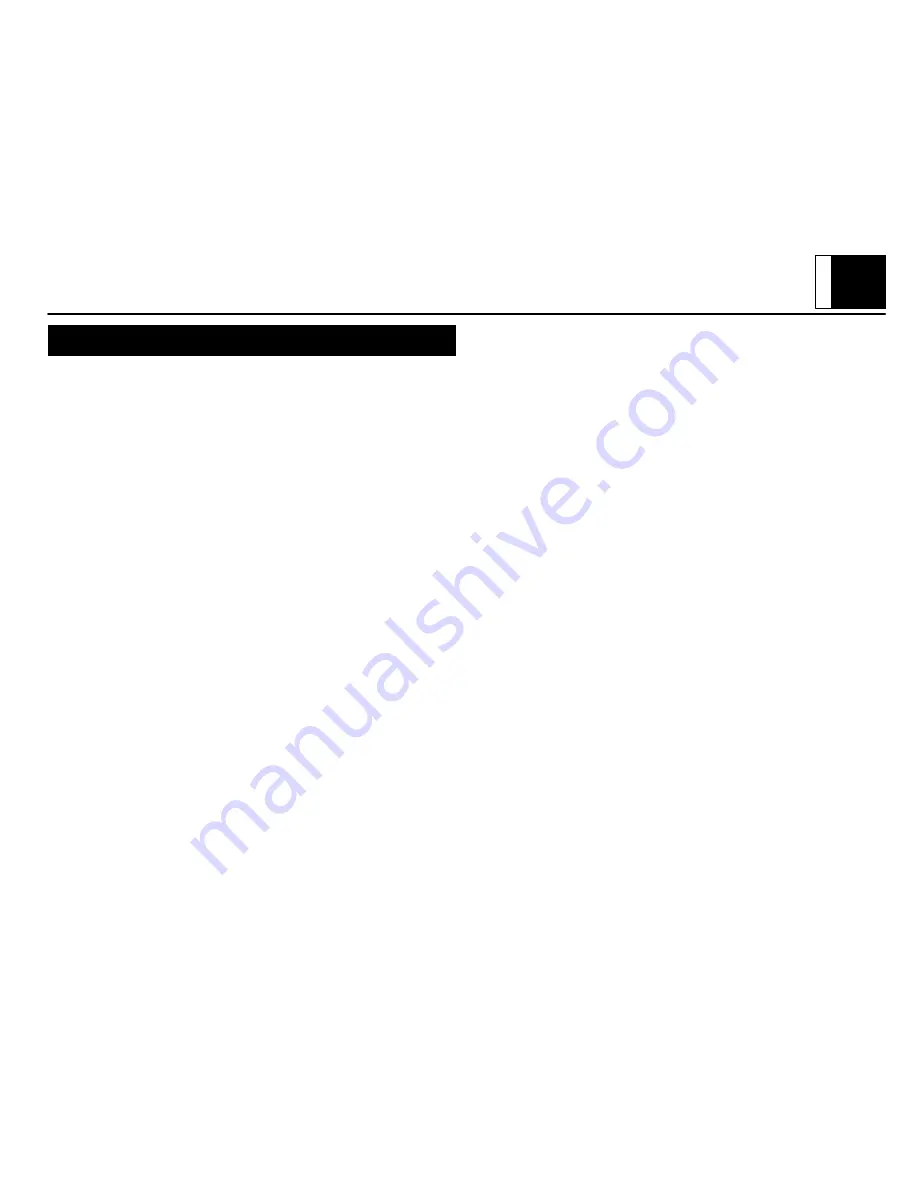
PA
G
E
3
P32/42 C
HASSIS
P32/42 Rev. 12/98
Section 2 – Frame
Hole drilling, welding, modifications, or alterations to the frame assembly are the respon-
sibility of persons performing these operations. These same individuals assume com-
plete responsibility for frame assembly reliability, performance after alterations and com-
pliance to applicable FMVSS requirements.
The following procedures and specific precautionary instructions are recommended for
proper installation of special bodies and/or equipment on GM frames. Failure to follow
these recommendations could result in serious damage to the basic vehicle.
Flanges
Do not drill holes in frame flanges:
D
Within 20 mm (0.75 in.) of radius tangent and 25 mm (1.0 in.) of raw edge.
D
Larger than 12 mm (0.50 in.).
D
Closer to each other than twice the hole diameter.
Holes
Holes to mount brackets, supports, and out-riggers must be drilled in the vertical side
rail web with the following restrictions:
D
Material between edge of hole and inside of upper or lower flange must not be less
than 37 mm (1.50 in.) for low carbon steel (36,000 PSI yield).
D
The minimum edge distance between any two (2) holes must be larger than twice
the diameter of the larger hole.
D
No holes should exceed 20 mm (0.75 in.) in diameter.
D
All holes should be drilled in the frame using appropriate drilling practice and
safety precautions.
Welding
CAUTION:
Fuel tank and fuel lines must be drained and all vapors purged to ensure
non-combustible mixture before any welding, brazing or soldering.
When welding low carbon steel side rails, crossmembers and brackets (32,000 or
36,000 PSI yield strength), emphasis is placed upon weld application techniques to
avoid stress risers that may adversely affect frame operating stresses.
When welding is performed anywhere on the vehicle, precautionary measures should
be taken to prevent damage to electrical system wiring, front suspension air cylinders
or components. Prior to any welding, parts or components which could be damaged by
excessive temperatures must be removed or adequately shielded; the battery cables
should be disconnected at the battery. Also prior to welding, the area to be welded and
surrounding area must be cleaned of all frame protective coating. After welding, when
parts are cool, carefully inspect wiring and electrical components for shorts or other dam-
age which could draw excessive currents and possibly cause an electrical system short
when the battery is reconnected. Apply protective coating to areas where coating was
removed.
Alterations
If the wheelbase is modified the alterer must take responsibility for compliance with af-
fected motor vehicle safety standards and for warranty on items such as driveshafts, uni-
versal joints, center bearings and rear transmission tailshaft, transmission case frac-
tures, output shaft bushings, bearings, brakes, fuel systems and any other related
component failures. Wheel base modifications can affect the operation of the ABS sys-
tem and may alter vehicle braking stability and or compliance with FMVSS 105. Addition-
ally, the customer must be alerted in the modifier’s owners manual that parts for the re-
worked area are not available through the General Motors service parts system.
Shear Plate Attachments
Attachments of shear plates should be accomplished by using existing manufacturing
holes already available in the frame side rails. Manufacturing holes, normally 16 mm in
diameter, are consistently placed along the frame side member in the center of the web
on each frame.
When additional holes are required for shear plate attachment, they should be no larger
than 20 mm (0.75 in.) in diameter. Holes are to be drilled no closer than 63.5 mm (2.5
in.) apart. For holes drilled forward of the rear axle, centers are to be no closer than 63.5
mm (2.5 in.) from the top or bottom flanges and no closer than 89 mm (3.5 in.) from any
suspension attachments. For frame holes drilled rearward of the rear axle, hole centers
are to be no closer than 51 mm (2.0 in.) from the top or bottom flange and no closer than
89 mm (3.5 in.) from suspension attachments.
No additional holes or notching of either top or bottom frame flanges is allowed.
Содержание P32
Страница 14: ...PAGE 14 P32 42 CHASSIS P32 42 Rev 12 98 P 30032 General Arrangement Diesel Engine Option L65 6 5L Turbo HO...
Страница 15: ...PAGE 15 P32 42 CHASSIS P32 42 Rev 12 98 P 30032 General Arrangement Diesel Engine Option L65 6 5L Turbo HO...
Страница 32: ...PAGE 32 P32 42 CHASSIS P32 42 Rev 12 98 P 30032 Auto Apply Park Brake Harness Ground...
Страница 33: ...PAGE 33 P32 42 CHASSIS P32 42 Rev 12 98 P 30000 Instrument Cluster Location...
Страница 35: ...PAGE 35 P32 42 CHASSIS P32 42 Rev 12 98 P 30000 Chassis Data...
Страница 36: ...PAGE 36 P32 42 CHASSIS P32 42 Rev 12 98 P 30032 Taperleaf Suspension...
Страница 37: ...PAGE 37 P32 42 CHASSIS P32 42 Rev 12 98 P 30042 Gas Engine 5 7L V8 Option L31...
Страница 38: ...PAGE 38 P32 42 CHASSIS P32 42 Rev 12 98 P 30042 Gas Engine 4 3L V6 Option L35...
Страница 39: ...PAGE 39 P32 42 CHASSIS P32 42 Rev 12 98 P 30032 Gas Engine 7 4L V8 Option L29...
Страница 40: ...PAGE 40 P32 42 CHASSIS P32 42 Rev 12 98 P 30032 Diesel Engine 6 5L Turbo Ho Option L65...
Страница 41: ...PAGE 41 P32 42 CHASSIS P32 42 Rev 12 98 P 30042 Diesel Engine 6 5L HO Option L57...
Страница 43: ...PAGE 43 P32 42 CHASSIS P32 42 Rev 12 98 P 30042 Air Conditioning Fittings...
Страница 44: ...PAGE 44 P32 42 CHASSIS P32 42 Rev 12 98 P 30042 Air Conditioning Compressor Locations...
Страница 45: ...PAGE 45 P32 42 CHASSIS P32 42 Rev 12 98 P 300 32 42 Fuel Filler Neck...
Страница 46: ...PAGE 46 P32 42 CHASSIS P32 42 Rev 12 98 P 30000 Fuel Tank Arrangement...
Страница 47: ...PAGE 47 P32 42 CHASSIS P32 42 Rev 12 98 P 30000 Temporary Fuel Tank Arrangement...
Страница 48: ...PAGE 48 P32 42 CHASSIS P32 42 Rev 12 98 P 30000 Center High Mounted Stop Lamp CHMSL...
Страница 49: ...PAGE 49 P32 42 CHASSIS P32 42 Rev 12 98 P 300 32 42 Lamp Mounting P 30032 P 30042...
Страница 50: ...PAGE 50 P32 42 CHASSIS P32 42 Rev 12 98 P 300 32 42 Instrument Panel Cut Out...