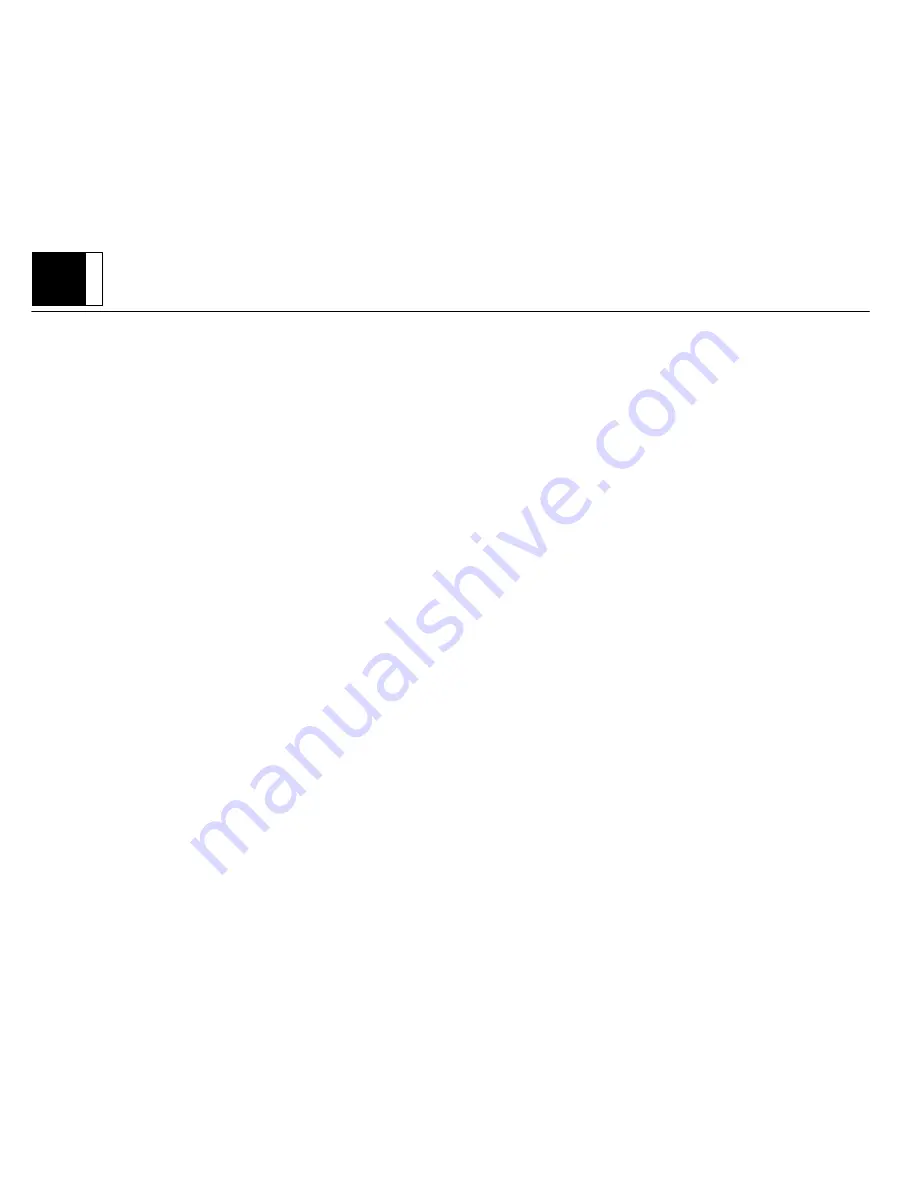
PA
G
E
12
P32/42 C
HASSIS
P32/42 Rev. 12/98
a minimum of 15 mm from terminal posts to avoid possible ground paths. If a top
hold-down is used, a non-corrosive, non-conductive coating is desirable.
Location:
The battery should be located in a well ventilated area where a temperature
build-up does not occur. The location should also provide protection to the battery
to prevent damage from foreign objects. The ends of the battery in the area of
the vent ports should be free of obstructions so that the gasses generated during
charging can be freely dissipated into the atmosphere.
D
Accessibility:
The hold-down should be convenient for tools and hands so that personal injury
does not occur. There should be clearance at the insulated and grounded
terminals so that wrenches can be used so that accidental grounds or shorts will
not occur. Terminal polarity markings, warning labels and test hydrometer should
be visible. The battery “ground” connection must be readily accessible for
disconnection, as required for vehicle electrical service requirements.
D
Tilt Angles:
For normal vehicle operation (at GVW), the battery should not be tilted (0
_
). For
installation or removal, it should not be necessary to tip or tilt the battery in excess
of 40
_
. This is to prevent acid spillage. For short duration vehicle shipment, do
not tilt the battery more than 19
_
from the horizontal.
D
Temperature:
The temperature of the electrolyte should not exceed 52
_
C. Infrequent peak
temperatures to 75
_
C can be tolerated in soak situations only. Shielding may be
required to protect the battery from a source of excessive heat.
D
Battery Trays:
Battery trays are supplied with the chassis. In the case of motor homes and diesel
school busses, the trays are secured to the frame rail (for shipping only).
The trays shipped on the rails may be relocated to other areas on the vehicle,
keeping in mind the recommendations noted above.
D
Battery Storage:
Today’s vehicles have several electronic devices which result in very small but
continuous current drains on their batteries, commonly referred to as “parasitic”
loads. Vehicles that are not used for an extended period of time may develop
extremely discharged and/or permanently damaged batteries resulting from
these parasitic loads. Discharged batteries can freeze at temperatures as high
as 20
_
F causing permanent damage.
To alleviate this condition, check to make sure green dot is visible, recharge as
necessary, then disconnect the negative battery cable on vehicles which are not
going to be in service within a 30 day period. If this is not possible, batteries should
be recharged periodically (every 30-60 days) until the green dot is visible.
NOTE:
The ignition switch must be off when connecting or disconnecting battery
cables or hangers (jumper cables). Failure to do so may overstress or damage
the ECM/PCM/TCM, VCM, ABS or other electronic components.
Modifications/add-on wiring must be carefully reviewed to ensure compatibility with the
base vehicle wiring by reviewing the vehicle electrical system mechanization prints, de-
tailed harness prints and Delphi–Packard electric division connection system design
quality guidelines. Due to the wide range of modifications that may be required for voca-
tional needs, it is not feasible for the O.E.M. to take into account all potential revisions.
For this reason, any person modifying existing vehicle wiring must assume responsibility
that the revisions have not degraded the electrical system performance. Any add-on wir-
ing must be properly fused and routed to prevent cut, pinch, and chafe problems, as well
as avoid exposure to excessive heat. Care must be exercised that existing vehicle inter-
faces do not have their current load capabilities exceeded, and that the respective con-
trol devices are not overloaded. Added wire size should be at least as large as the the
wire to which it is attaching in order for fuse protection to be maintained.
A Packard electric wiring repair kit is available through Kent–Moore (GM P/N 12085264,
Kent–Moore P/N J38125-4). This kit contains instructions, tools and components for
making repairs to wiring harness components. This kit would also greatly assist in ac-
complishing necessary add-on wiring such as body marker lamps, so that system reli-
ability/durability is maintained.
Electrical wiring components can be obtained through your authorized GM dealer. Many
Packard Electric components are also available through Pioneer Standard Company
(1-800-PACKARD). Pioneer may also be able to assist in making necessary wiring addi-
tions by providing custom wiring stubs or jumpers to your specifications.
Fusible Link Repair Procedure:
1. Cut damaged fusible link from wiring harness assembly splice.
2. Strip insulation from harness wire as required to splice on new fusible link.
3. Fabricate a new fusible link wire approximately 6 to 8 in. long from the same
wire size as the original link. (Acceptable fusible link material will be imprinted
with the wire size and the wording to identify it as fusible link. Fusible link
cable is not the same as normal vehicle wiring.)
4. Terminate fusible link harness wire with a suitable compression splice clip, and
solder with an electrical grade rosin core solder. Wrap splice area with tape to
provide electrical insulation, as well as mechanical strain relief at the splice.
5. Strip, terminate, solder, and insulate remaining end of fusible link with ap-
propriate termination to be compatible with the rest of the electrical system.
6. For further information, refer to the instruction manual in the wiring repair kit
referenced elsewhere in this section.
Содержание P32
Страница 14: ...PAGE 14 P32 42 CHASSIS P32 42 Rev 12 98 P 30032 General Arrangement Diesel Engine Option L65 6 5L Turbo HO...
Страница 15: ...PAGE 15 P32 42 CHASSIS P32 42 Rev 12 98 P 30032 General Arrangement Diesel Engine Option L65 6 5L Turbo HO...
Страница 32: ...PAGE 32 P32 42 CHASSIS P32 42 Rev 12 98 P 30032 Auto Apply Park Brake Harness Ground...
Страница 33: ...PAGE 33 P32 42 CHASSIS P32 42 Rev 12 98 P 30000 Instrument Cluster Location...
Страница 35: ...PAGE 35 P32 42 CHASSIS P32 42 Rev 12 98 P 30000 Chassis Data...
Страница 36: ...PAGE 36 P32 42 CHASSIS P32 42 Rev 12 98 P 30032 Taperleaf Suspension...
Страница 37: ...PAGE 37 P32 42 CHASSIS P32 42 Rev 12 98 P 30042 Gas Engine 5 7L V8 Option L31...
Страница 38: ...PAGE 38 P32 42 CHASSIS P32 42 Rev 12 98 P 30042 Gas Engine 4 3L V6 Option L35...
Страница 39: ...PAGE 39 P32 42 CHASSIS P32 42 Rev 12 98 P 30032 Gas Engine 7 4L V8 Option L29...
Страница 40: ...PAGE 40 P32 42 CHASSIS P32 42 Rev 12 98 P 30032 Diesel Engine 6 5L Turbo Ho Option L65...
Страница 41: ...PAGE 41 P32 42 CHASSIS P32 42 Rev 12 98 P 30042 Diesel Engine 6 5L HO Option L57...
Страница 43: ...PAGE 43 P32 42 CHASSIS P32 42 Rev 12 98 P 30042 Air Conditioning Fittings...
Страница 44: ...PAGE 44 P32 42 CHASSIS P32 42 Rev 12 98 P 30042 Air Conditioning Compressor Locations...
Страница 45: ...PAGE 45 P32 42 CHASSIS P32 42 Rev 12 98 P 300 32 42 Fuel Filler Neck...
Страница 46: ...PAGE 46 P32 42 CHASSIS P32 42 Rev 12 98 P 30000 Fuel Tank Arrangement...
Страница 47: ...PAGE 47 P32 42 CHASSIS P32 42 Rev 12 98 P 30000 Temporary Fuel Tank Arrangement...
Страница 48: ...PAGE 48 P32 42 CHASSIS P32 42 Rev 12 98 P 30000 Center High Mounted Stop Lamp CHMSL...
Страница 49: ...PAGE 49 P32 42 CHASSIS P32 42 Rev 12 98 P 300 32 42 Lamp Mounting P 30032 P 30042...
Страница 50: ...PAGE 50 P32 42 CHASSIS P32 42 Rev 12 98 P 300 32 42 Instrument Panel Cut Out...