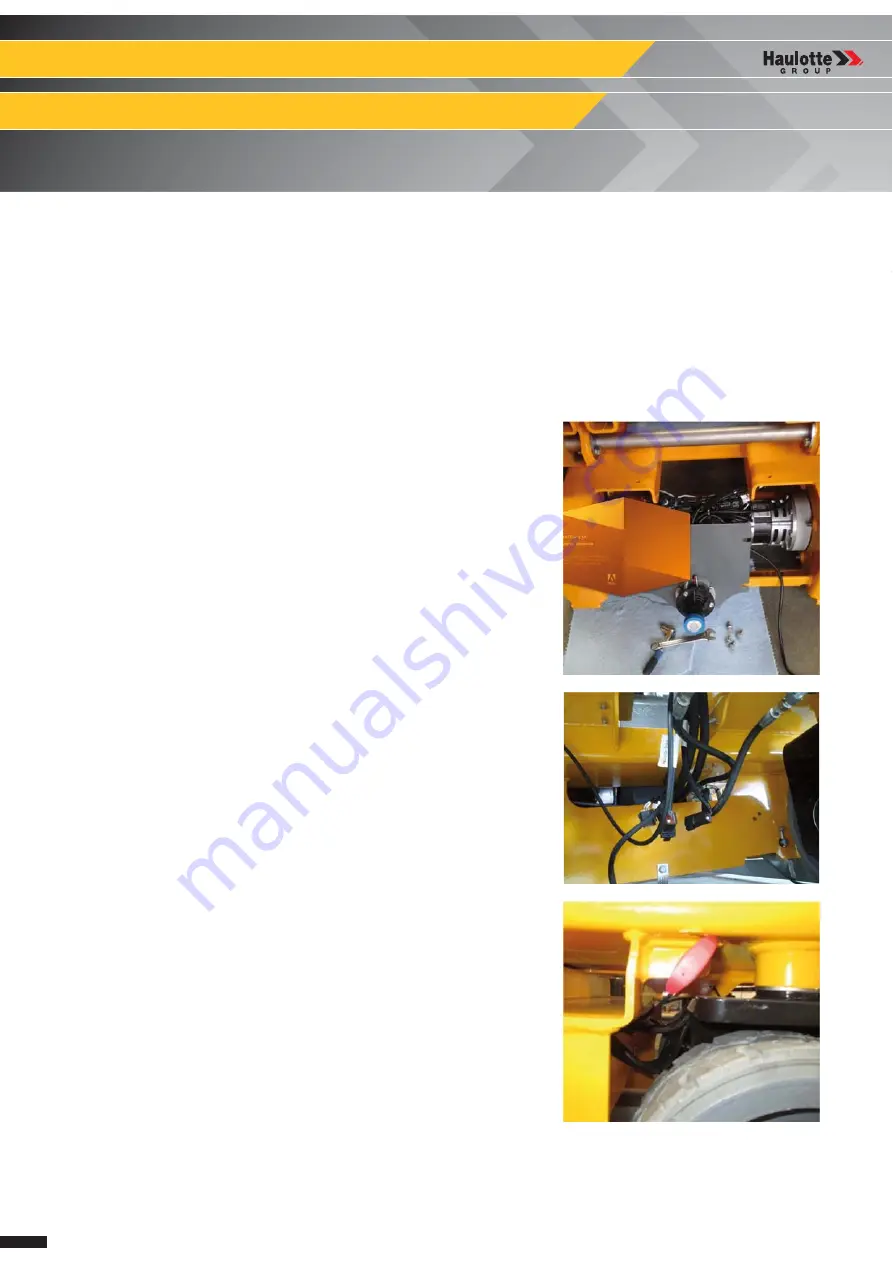
90
4000429690
E 11.15
US / GB
Scissors
Removal / replacement of Scissor pack
MS0096
3 - Removal
N.B.-:-T
HIS
PROCEDURE
IS
EXPLAINED
WITHOUT
REMOVING
OF
THE
REAR
COUNTERWEIGHT
(
AS
PERHAPS
PERFORMED
IN
THE
FIELD
). B
UT
REMOVAL
OF
THE
REAR
STEP
COUNTERWEIGHT
MAKES
THE
ACCESS
MUCH
BETTER
AND
IS
RECOMMENDED
WHEN
POSSIBLE
. I
F
THE
COUNTERWEIGHT
IS
REMOVED
,
THERE
IS
NO
NEED
TO
RAISE
THE
SCISSOR
FRAME
AND
PLACE
ON
THE
SAFETY
SUPPORT
,
ALL
WORK
CAN
BE
DONE
WITH
THE
PLATFORM
IN
STOWED
POSITION
.
N.B.-:-T
HIS
PROCEDURE
WAS
COMPLETED
USING
AN
OVERHEAD
CRANE
BUT
COULD
EQUALLY
BE
PERFORMED
USING
A
FORKLIFT
.
• After removing the counterweight, remove the plate supporting the
slope sensor (the scissor assembly will need to extracted towards
the rear later on).
• At the front of the machine, between the steering wheels you will find
connections for the platform wiring loom, the wiring to the lift cylinder
and the connections for the 2 angle sensors.
• Disconnect all these cables.
• Loosen the emergency cable from its fixation on the chassis and pull
the cable into the middle of the chassis where the connectors above
are located. The cable can rest in place when the scissor frame is
removed.
Содержание OPTIMUM 1931 E
Страница 2: ...2 4000429690 E 11 15 US GB OPTIMUM 8 OPTIMUM 1931 E...
Страница 10: ...10 4000429690 E 11 15 US GB OPTIMUM 8 OPTIMUM 1931 E A Preface Foreword Notes...
Страница 19: ...19 4000429690 E 11 15 US GB OPTIMUM 8 OPTIMUM 1931 E C Familiarization Familiarization Notes...
Страница 50: ...50 4000429690 E 11 15 US GB OPTIMUM 8 OPTIMUM 1931 E D Inspection and maintenance schedule Notes...
Страница 54: ...54 4000429690 E 11 15 US GB General data Structural part inspection MS0001 Notes...
Страница 64: ...64 4000429690 E 11 15 US GB General data Breaking test procedure MS0004 Notes...
Страница 72: ...72 4000429690 E 11 15 US GB Electric Electrical wiring MS0025 Notes...
Страница 76: ...76 4000429690 E 11 15 US GB Scissor arm Scissor arms screw Periodical checks MS0073 Notes...
Страница 88: ...88 4000429690 E 11 15 US GB Platform Removal replacement of platform assembly MS0095 Notes...
Страница 98: ...98 4000429690 E 11 15 US GB Scissors Removal replacement of Scissor pack MS0096 Notes...
Страница 102: ...102 4000429690 E 11 15 US GB Chassis Calibration steering MS0097 Notes...
Страница 116: ...116 4000429690 E 11 15 US GB Ground control box HAULOTTE Activ Screen MS0106 Notes...
Страница 134: ...134 4000429690 E 11 15 US GB OPTIMUM 8 OPTIMUM 1931 E E Trouble shooting and diagram 3 Electric diagram...
Страница 135: ...135 4000429690 E 11 15 US GB OPTIMUM 8 OPTIMUM 1931 E E Trouble shooting and diagram...
Страница 136: ...136 4000429690 E 11 15 US GB OPTIMUM 8 OPTIMUM 1931 E E Trouble shooting and diagram...
Страница 137: ...137 4000429690 E 11 15 US GB OPTIMUM 8 OPTIMUM 1931 E E Trouble shooting and diagram 4 Hydraulic diagram...
Страница 138: ...138 4000429690 E 11 15 US GB OPTIMUM 8 OPTIMUM 1931 E E Trouble shooting and diagram Notes...
Страница 148: ...148 4000429690 E 11 15 US GB OPTIMUM 8 OPTIMUM 1931 E F Records...