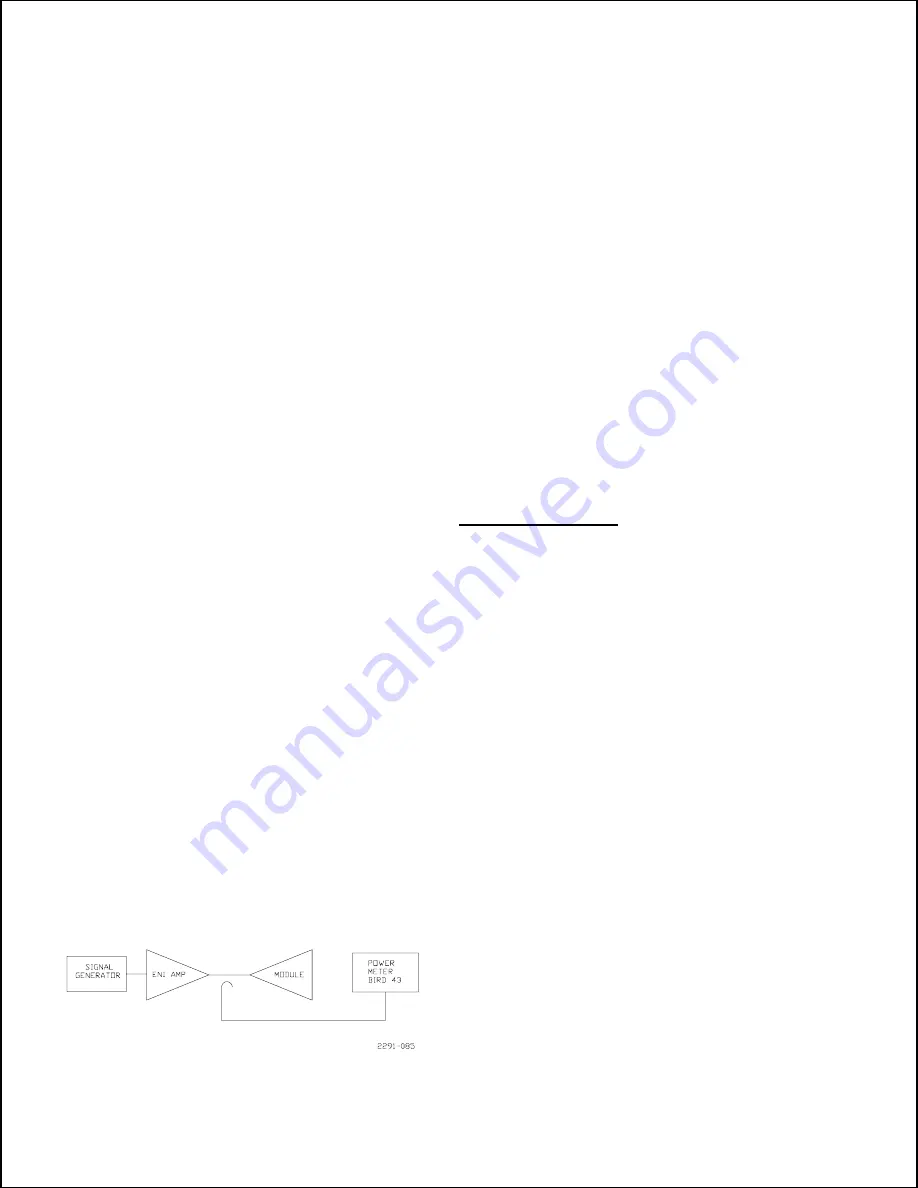
High band driver gain is measured at 150 Watts average black power.
Black picture (sync and blanking only) is the best approximation
for this test. If possible set power out to 625 Watts average with a
black picture. Turn off transmitter and move the wattmeter to the
input. Turn on transmitter and using an element of appropriate range
measure the input power.
Calculate gain in dB using 10 log(P out/P in).
Since the driver input power is in mW, it will be necessary to use
a power meter with an appropriate range to measure input power.
Results should be as shown in Table A-1.
A.5.2.2.1
Alternate method for measurement under program conditions
To measure gain insert a directional coupler of sufficient power
capacity in the output coax. Note the sample level on a spectrum
analyzer or field strength meter. Move the directional coupler to
the input access loop and note the drive level.
On field strength meters peak sync levels may be used as the
reference with program present but the gain figure may vary
slightly from the standard test method. Blanking level can usu-
ally be clearly seen on the spectrum display and would be the
preferred reference.
NOTE
The remaining tests of this procedure are performed in an Aural slot.
INPUT/POWER DIVIDER PWA.
In Driver modules the pad is constructed using three resistors.
The resistors are selected using Table A-2, (817-2100-639) Input
Attenuators/Driver.
A.5.2.3
ISO Volts Check
Adjust PA power to 1050 Watts at aural frequency. For a high
band driver use 500 Watts aural and for a low band driver use 200
Watts.
If necessary manually disable some of the other aural modules
to bring the drive level up as required.
Measure the voltage at P1-2 on any one of the four quarter
modules. (They are wired in parallel.)
Verify the value to be 0.3 Volts DC or less.
To test the fault threshold, remove the RF Drive.
Using an isolated DC supply (possibly a 9 Volt battery and a
variable resistance), inject voltage at P1-2 of any quarter module
and slowly increase voltage until the module faults.
The module should trip off between 1.7 and 2.1 Volts.
A.5.2.4
Overdrive Check
Perform this check only after verifying that the module gain
adjustment is correct. See paragraph on Gain Check located
elsewhere in this section.
Pre-set the Overdrive Pot R101 fully clockwise
Set the input drive on the aural frequency per the following:
MODULE TYPE
DRIVE LEVEL
TRIP
TOLERANCE
High Band
PA
120 Watts
2 Watts
Low Band PA
35 Watts
1 Watt
Low and High Band Drivers
370 milliwatts
10 milliwatts
To set the trip point adjust R101 CCW until the module faults
and gives a blink code 2 on the red LED.
The red LED display has a few seconds time delay before
indicating. It may be helpful to observe the power meter or
quarter module current which will react instantaneously, while
setting the overdrive trip point.
Check the setting by reducing the power, enable the module, and
increase power. The drive power level must trip within the
allowed tolerance. If not readjust R101 as required.
A.5.2.5
VSWR Check
VSWR Protection Check
Precise Method:
a. Connect a 50 ohm termination to the module RF input.
Connect a signal generator, test amplifier, and power meter
to the module output per Figure A-7.
b. Apply 50 V DC and enable the module.
c. Set the signal generator to the Aural carrier frequency and
apply 94.5 Watts CW into the PA module RF output.
d. Slowly adjust R8 CCW until the module disables and gives
a blink code of one on the red LED.
e. Reduce the signal generator level and enable the module.
Slowly raise the signal generator level while monitoring
the power applied to the module. The module should
disable between 90 and 100 Watts. If not, readjust R8 as
required.
f. Turn off the 50 V DC and restore the test setup to normal
configuration.
Alternate Procedure for approximated adjustment
PAs are set using 1050 Watts aural output as the forward reference.
For low band driver use 200 Watts and for high band driver 500
Watts.
R8 provides a DC offset to allow turn on in a complete transmitter
where some crosstalk may exist.
Apply DC (No RF) to module. Adjust R8 for proper voltage
at U6-pin 4.
Figure A-7. VSWR Protection Test Setup
Platinum™ Series
A-16
888-2457-001
WARNING: Disconnect primary power prior to servcing.
Содержание Platinum HT EL 2000LS
Страница 4: ...This page left blank intentionally...
Страница 6: ......
Страница 8: ...ii...
Страница 12: ...This page left blank intentionally...
Страница 26: ...Figure 2 3 Platinum Series 2 8 888 2457 001 WARNING Disconnect primary power prior to servicing...
Страница 27: ...Figure 2 4 Section II Installation 888 2457 001 2 9 WARNING Disconnect primary power prior to servicing...
Страница 28: ...Figure 2 5 Platinum Series 2 10 888 2457 001 WARNING Disconnect primary power prior to servicing...
Страница 29: ...Figure 2 6 Section II Installation 888 2457 001 2 11 WARNING Disconnect primary power prior to servicing...
Страница 30: ...Figure 2 7 Platinum Series 2 12 888 2457 001 WARNING Disconnect primary power prior to servicing...
Страница 31: ...Figure 2 8 Section II Installation 888 2457 001 2 13 WARNING Disconnect primary power prior to servicing...
Страница 32: ...Figure 2 9 Platinum Series 2 14 888 2457 001 WARNING Disconnect primary power prior to servicing...
Страница 33: ...Figure 2 10 Section II Installation 888 2457 001 2 15 WARNING Disconnect primary power prior to servicing...
Страница 34: ...Figure 2 11 Platinum Series 2 16 888 2457 001 WARNING Disconnect primary power prior to servicing...
Страница 38: ...This page left blank intentionally...
Страница 46: ...This page left blank intentionally...
Страница 54: ...This page left blank intentionally...
Страница 88: ...This page left blank intentionally...