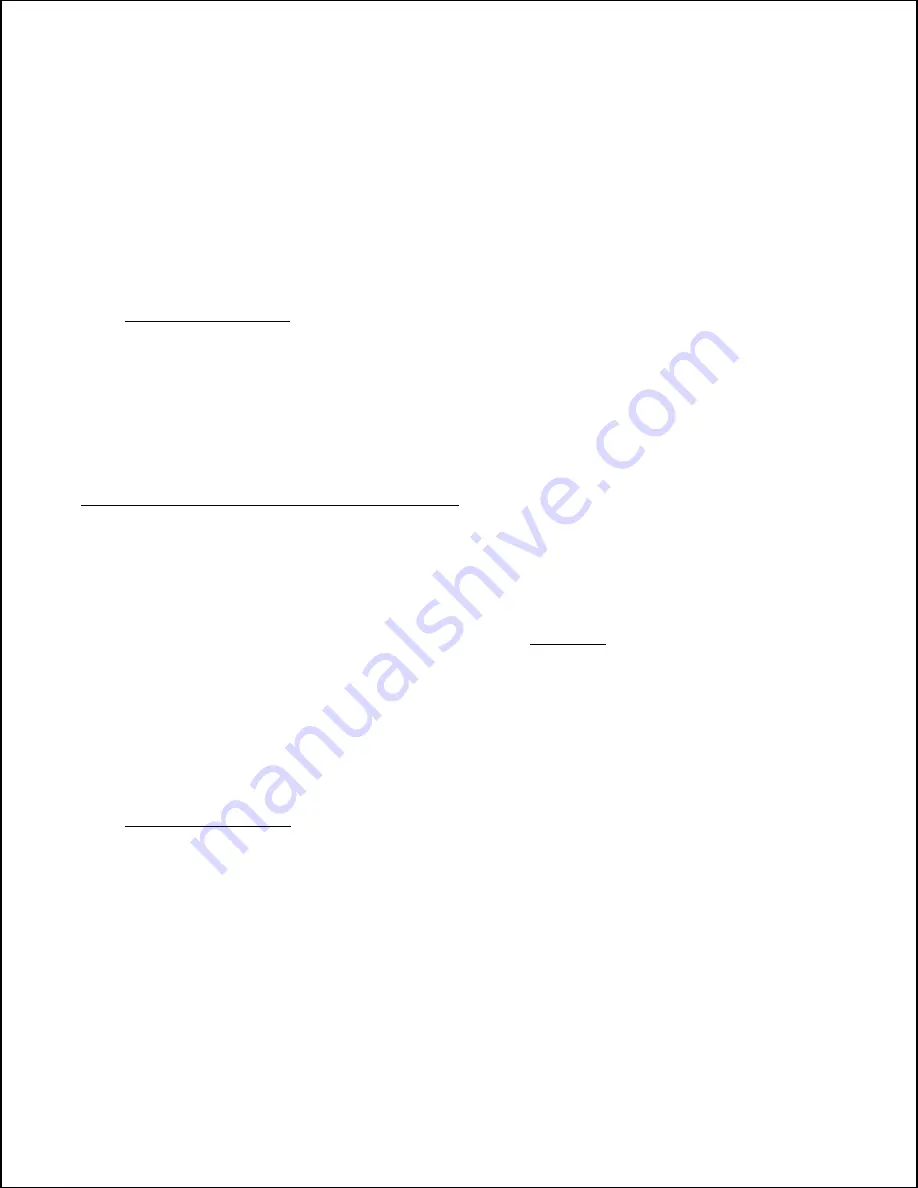
When pass FETs are replaced, change Q1 and R72 on the Module
Control Board, and change the 5.6 ohm resistors and the zener
diode on the pass FET buss bar assembly. These parts are
typically stressed in the event of pass FET failure and replacing
them will promote long term reliability.
Use the same ESD procedures outlined in the section on RF FET
replacement. The FET drains are insulated from the chassis with
“SIL-PADS”, silicon insulating pads that need no heat sink
compound.
Before enabling the module, check to see that the drains are not
shorted to the chassis using an ohmmeter.
A.4.6
Chip Cap Replacement
It is a common technique to use two irons with small tips (one
on each side) when removing or installing chip caps. Both sides
of the chip cap should be heated simultaneously to avoid residual
stresses which might later cause a failure.
Note that the capacitor values listed in the Parts List are typical
values. Check the value of the capacitor to be replaced before
ordering a replacement part.
A.5
Test Procedure Solid State TV Modules
Install transmitter section of module test fixture into transmitter.
Attach RF output cable to module test fixture through access slot in
the fixture, and connect to wattmeter and 50 ohm load (1kW).
Install input wattmeter. Use RF input access cable on side of test
fixture.
Attach extension section and install module onto fixture. (Do not
install module protective cover at this time.)
Perform a complete visual inspection of the module to be repaired.
Remove red wire from TB1 and install a current meter in line.
The current meter needs to be capable of measuring 400 mA steps
accurately, and up to 10 Amps total. A clamp-on probe, if
available, makes the task easier. Use an ammeter that is resistant
to RFI.
A.5.1
Pre-operational Checks
A.5.1.1
Initial Power Up
Close CB2, this breaker is only to protect the wiring between
transmitter and test fixture.
Apply 50 Volts DC only to module by turning on circuit breaker
CB1. (Red LED on module front panel will be on.)
The +5 and +15 Volt PCM supplies can be checked when 50 Volts
is applied.
A.5.1.2
Idle Current Check
The module cover section of the extender assembly should be
removed so that no RF drive can be applied.
Enable module with “MODULE ENABLE” switch on test fixture.
Red LED will extinguish. On PA modules one half of green LED
will illuminate. On driver modules both halves of green LED will
be on.
Note the current reading of the quarter module. Compare this
reading to the values found in the Table A-1 located at the end of
this section. Check all four quarter modules.
If quarter module currents are all OK, the module is ready for RF
testing. If the current is incorrect, refer to Idle Current Test
procedures.
A.5.1.3
Over/Under Voltage Check
Since there are no adjustments this is an operational check only.
Measure the voltages at U7:
Pin 4 = 10.3V +/- 0.2V
50 Volt supply sample
approximately 1/5th ratio
Pin 5 = 11.1V +/- 0.2V
Over threshold
Pin 6 = 8.9V +/- 0.2V
Under threshold
To simulate over voltage fault, connect an isolated supply at the
junction of R47 and R48. Monitor U7 pin 7 voltage to note trip
point.
Inject increasing DC voltage until the circuit trips.
To simulate under voltage fault connect a 100k ohm variable
resistor across R47.
Monitor U7 pin 7 and decrease the value of resistance until the
circuit trips.
If an external 50 Volt source is available to operate the entire
module you may check the trip points for operation at 44 Volts
and 53.5 Volts.
A.5.2
RF Testing
CAUTION
IF THE UNIT BEING TESTED IS A DRIVER BE SURE IT IS IN A
DRIVER POSITION IN THE TRANSMITTER. EXCESSIVE DRIVE
WILL DESTROY THE INPUT ATTENUATOR IF A DRIVER IS OPER-
ATED IN A PA SLOT.
Testing of drivers may be done in a PA slot if the drive cable
access loop on the extender is removed and a external source of
RF is applied (i.e. the standby exciter in dual configurations).
Note
IF YOU ATTEMPT TO OPERATE A PA IN A DRIVER SLOT,
THE DRIVE LEVEL WILL BE INSUFFICIENT TO COMPLETE
THE TESTS.
A.5.2.1
Application of Drive
To test a driver module it is recommended to adjust exciter power
to minimum before applying RF in the configurations with only
one driver in the path.
Install protective cover on the module and note the power output
on the wattmeter. PA module output should be in proportion to
the others in the system.
A.5.2.2
Gain Check
PA gain is measured in factory test at visual frequency with
carrier only operating at 625 Watts.
Low band driver gain is measured at 30 Watts average black power.
Appendix A - RF Amplifier Modules
888-2457-001
A-15
WARNING: Disconnect primary power prior to servcing.
Содержание Platinum HT EL 2000LS
Страница 4: ...This page left blank intentionally...
Страница 6: ......
Страница 8: ...ii...
Страница 12: ...This page left blank intentionally...
Страница 26: ...Figure 2 3 Platinum Series 2 8 888 2457 001 WARNING Disconnect primary power prior to servicing...
Страница 27: ...Figure 2 4 Section II Installation 888 2457 001 2 9 WARNING Disconnect primary power prior to servicing...
Страница 28: ...Figure 2 5 Platinum Series 2 10 888 2457 001 WARNING Disconnect primary power prior to servicing...
Страница 29: ...Figure 2 6 Section II Installation 888 2457 001 2 11 WARNING Disconnect primary power prior to servicing...
Страница 30: ...Figure 2 7 Platinum Series 2 12 888 2457 001 WARNING Disconnect primary power prior to servicing...
Страница 31: ...Figure 2 8 Section II Installation 888 2457 001 2 13 WARNING Disconnect primary power prior to servicing...
Страница 32: ...Figure 2 9 Platinum Series 2 14 888 2457 001 WARNING Disconnect primary power prior to servicing...
Страница 33: ...Figure 2 10 Section II Installation 888 2457 001 2 15 WARNING Disconnect primary power prior to servicing...
Страница 34: ...Figure 2 11 Platinum Series 2 16 888 2457 001 WARNING Disconnect primary power prior to servicing...
Страница 38: ...This page left blank intentionally...
Страница 46: ...This page left blank intentionally...
Страница 54: ...This page left blank intentionally...
Страница 88: ...This page left blank intentionally...