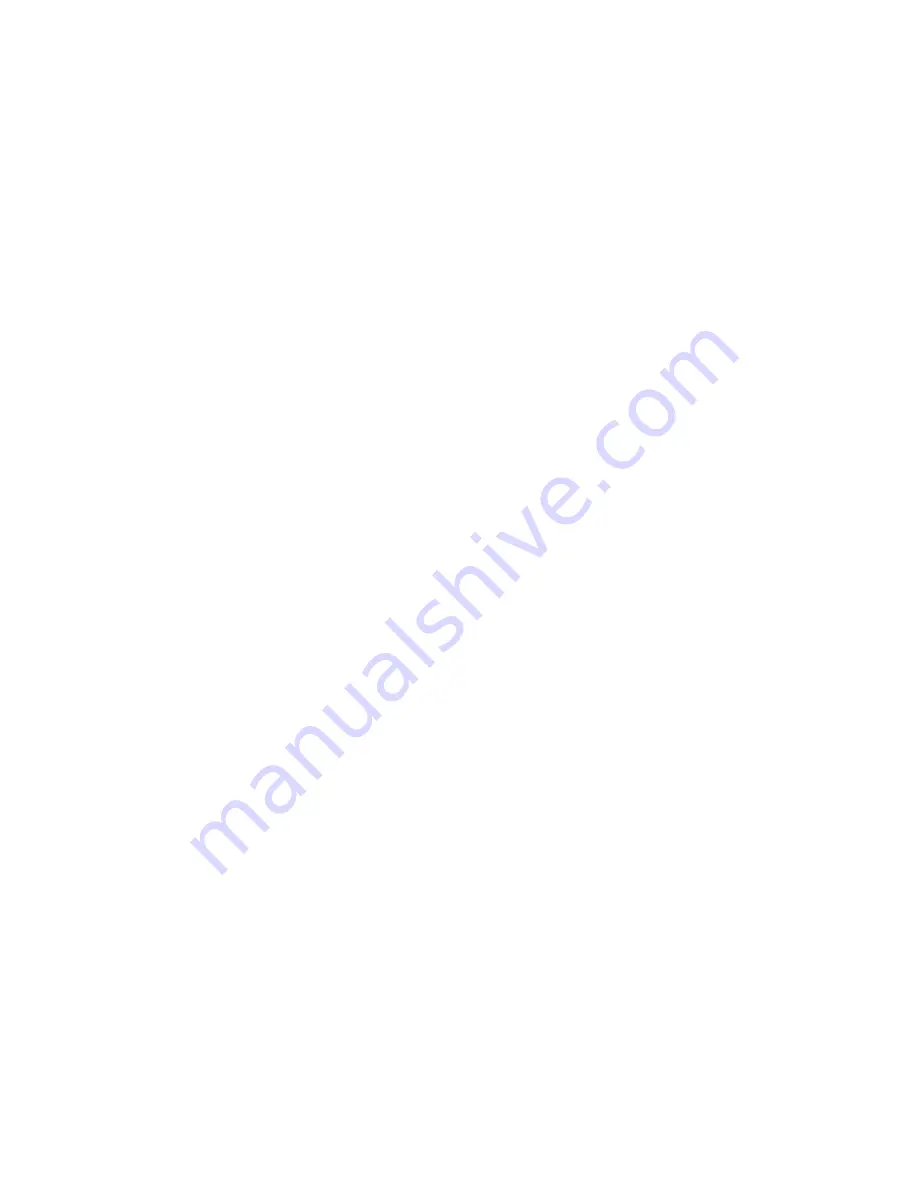
5
APP-001b
APR 2007
WATER BUBBLER DRAIN LINE
A 1” (25 mm) PVC socket/1” FPT water drain connection
is located at the bottom of the bubbler. The water bubbler
drain line should flow to a suitable drain or container. See
Figure 4. If the drain line is run overhead, the fitting on the
top of the water bubbler must be sealed, including the ¼”
NPT vent connection in the fitting, and a protective mesh
installed around the clear tube. Do not run the line more
than 10’ (3 m) above the height of the bubbler because the
pressure on the water bubbler could be excessive. Support
the drain line to prevent undue stress on the water bubbler.
Also, do not install a shutoff valve in this line.
Initially, fill the water bubbler with water through the 3”
(80 mm) plug located on top of the tube. Keep the plug
lubricated and hand tight. Check for leaks at the hose
fittings.
WATER PURGE LINE
Water removed from the refrigeration system by the
AUTO-PURGER Plus flows out the water purge line. This
line should be directed to a customer supplied container,
such as a 55 gallon drum for example. See Figure 4. It is
recommended to use rigid metal tubing or to secure the
line. Commonly, when draining water initially all the water
is released, then any oil is released, and then a small
quantity of ammonia vapor may be released. A loose hose
may whip around when the last of the liquid slugs come
out of the hose and is therefore not recommended. The
customer supplied container may be par tially filled with
water, and the end of the water purge line submerged in
this water so that any small amount of ammonia vapor
that may be released is dissolved in this water.
OIL DRAINS
Excess oil can reduce the purger capacity by lowering
the evaporating or condensing rate. Oil is not typically a
problem. Oil in the evaporator chamber is typically released
with the water that is released out the water purge line.
However, any oil that may collect in the purger can be
drained off through the two capped ¼” valves on the purger.
See Figure 1. Before draining oil, close the foul gas and
low-pressure pumped-liquid valves. Allow the purger to
pump out, then close the low-pressure liquid return and
suction line valves. Use normal oil draining precautions
to prevent injur y or proper ty damage.
ELECTRICAL CONNECTIONS
The standard AUTO-PURGER Plus requires a 115V 50/60Hz
17 amp electrical supply on a 20 amp circuit breaker;
models for 220V 50/60Hz, 11 amps electrical supply on
a 15 amp circuit breaker are available. All models have a
½” (13 mm) knockout on the side of the control cabinet to
access the power connection terminal strip. Any unused
knockout holes must be sealed to prevent splashing water,
dust, and debris from entering the control cabinet. After
completing all electrical connections inside the cabinet,
connect the cable from the PLC Control Console to the
PLC. Connect the cable plug to the socket and tighten the
hand screws. Refer to the wiring tag inside unit.
AUTO-PURGER Plus models APP08, APP16, and APP24
have an additional ¾” (20 mm) knockout for individual
purge point solenoid valves. Wires from each purge point
solenoid valve should be brought to the purger control
cabinet. Any additional access holes should be made on
the side of the control cabinet. All access holes into the
control cabinet must be sealed to prevent moisture, dust,
and debris entering the cabinet.
From each purge point solenoid, one wire is connected
to the corresponding screw terminal for the purge point
inside the control cabinet on the terminal strip. For 115VAC
models, the other wire from the purge point solenoid is
connected together for all the purge points and tied to the
available neutral position on the top terminal strip. For
the 220VAC models, the other wire from the purge point
solenoid is connected together for all the purge points
and tied to the top terminal strip labeled PP_COM.
Models APP08, APP16, and APP24 supply 115VAC to the
purge points regardless of whether 115VAC or 220VAC is
supplied to the control cabinet.
All APP models have a relay available which energizes
whenever action is required by plant personnel. The
normally open contacts will close when action is required.
If desired, the contacts may be connected to a light, an
audible alarm, or to a plant computer, to notify plant
personnel to attend to the purger. The contacts are rated
for 10 amps. Connection to the relay is made at the top
terminal strip labeled REMOTE REL AY.
LEAK TEST
Use standard refrigeration procedures to check the
AUTO-PURGER Plus for leaks before placing it in service.
To confirm a leak-free AUTO-PURGER Plus, manually
open one remote purge point solenoid valve, if there is
one. Manually open the foul gas shut-off valve and allow
pressure inside the purger to build to condensing pressure,
as shown on the high side pressure gauge. Then, manually
open the high side to low side bypass valve to pressurize
the evaporator section of the purger, as shown on the low
side pressure gauge. See Figure 4. Check for leaks. Close
the high side to low side bypass valve.