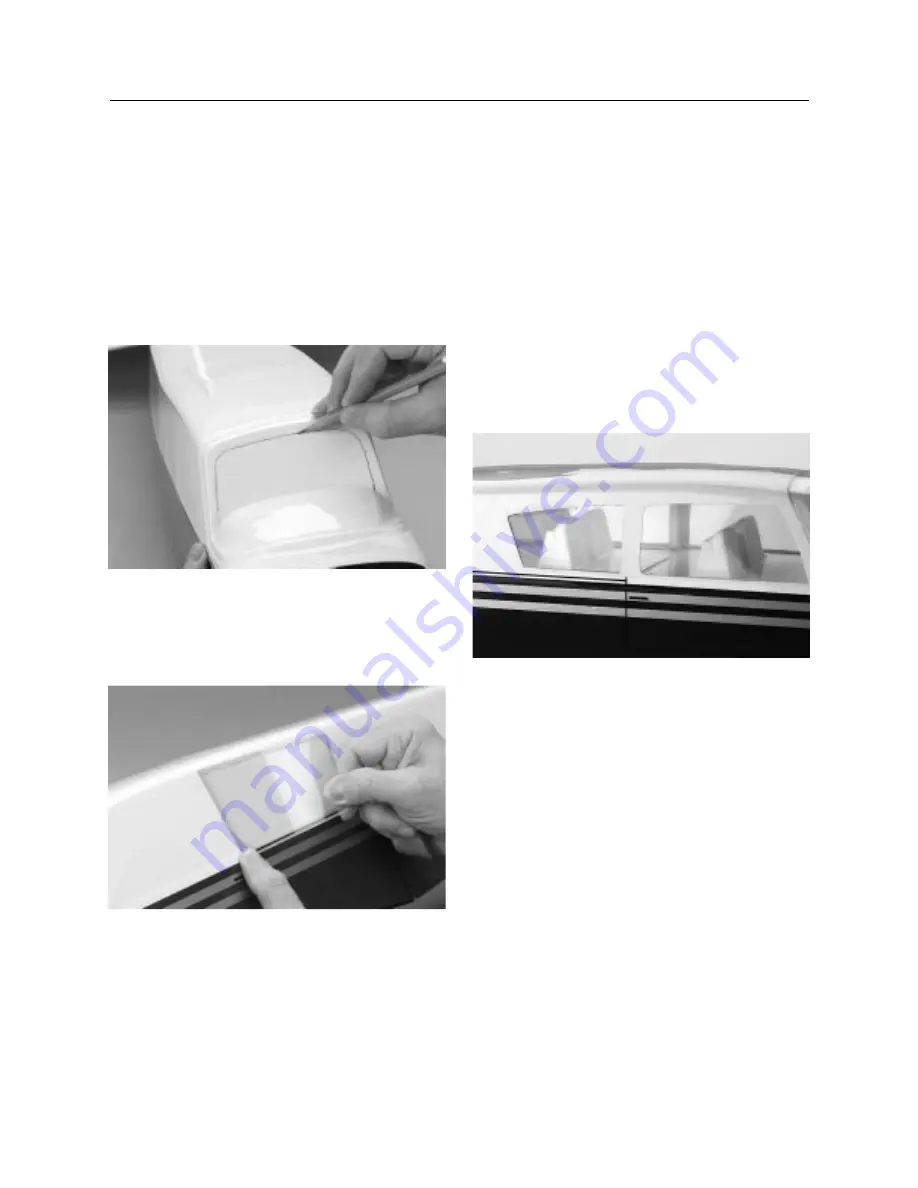
21
Step 3.
Trim out the opening of the front windshield. It helps to
use a felt tipped marking pen to outline the opening before
cutting.
Note:
There are no scribe marks, so it’s important you mark
the opening before beginning. Again, use caution
when cutting the opening with your hobby knife. We
suggest the final trimming be done with a sanding
stick (medium/fine).
Step 4.
Using the side window openings as a guide, cut the
clear plastic sheet to make the side windows. Trial fit each
window to be sure they fit and can be installed from inside the
fuselage.
Step 5.
Apply canopy glue to the clear windows and carefully
install each into the interior of the fuselage. Masking tape can be
used to hold the side windows in place while the glue dries. Let
the glue dry completely before proceeding to the next step.
Note:
You may wish to only mount the windows on one
side, leaving one side open to give you access for
mounting the seats. Once the seats are installed, you
can then mount the remaining windows and front
windshield.
Step 6.
Remove any masking tape from the windows before
installing the seats. Trial fit the front and back seats in the
fuselage. The front seat backs should be approximately 2
′′
in
front of the back door trim of the fuselage. The rear seats will be
positioned behind the fuselage former and behind the front door
trim, close to where the front seats are located. There are two
balsa rails that can be used to help form a lip on which the rear
seat rests. Trimming of the plastic will be required to obtain the
proper fit. Once you are satisfied with the fit and location of each
seat, proceed to mix approximately 1/4 ounce of 12-minute
epoxy. Apply the epoxy to the rear seat rails first and mount the
rails.
Once the rails are dry, proceed to mount the rear seat.
Step 7.
Install the front seat next. It will be mounted on the
fuselage plywood doublers and some trimming may be required
to obtain a good fit. Once you are satisfied with fit and location,
proceed to epoxying the fuselage.
CONTINUED
Section 5: Assembling the Fuselage