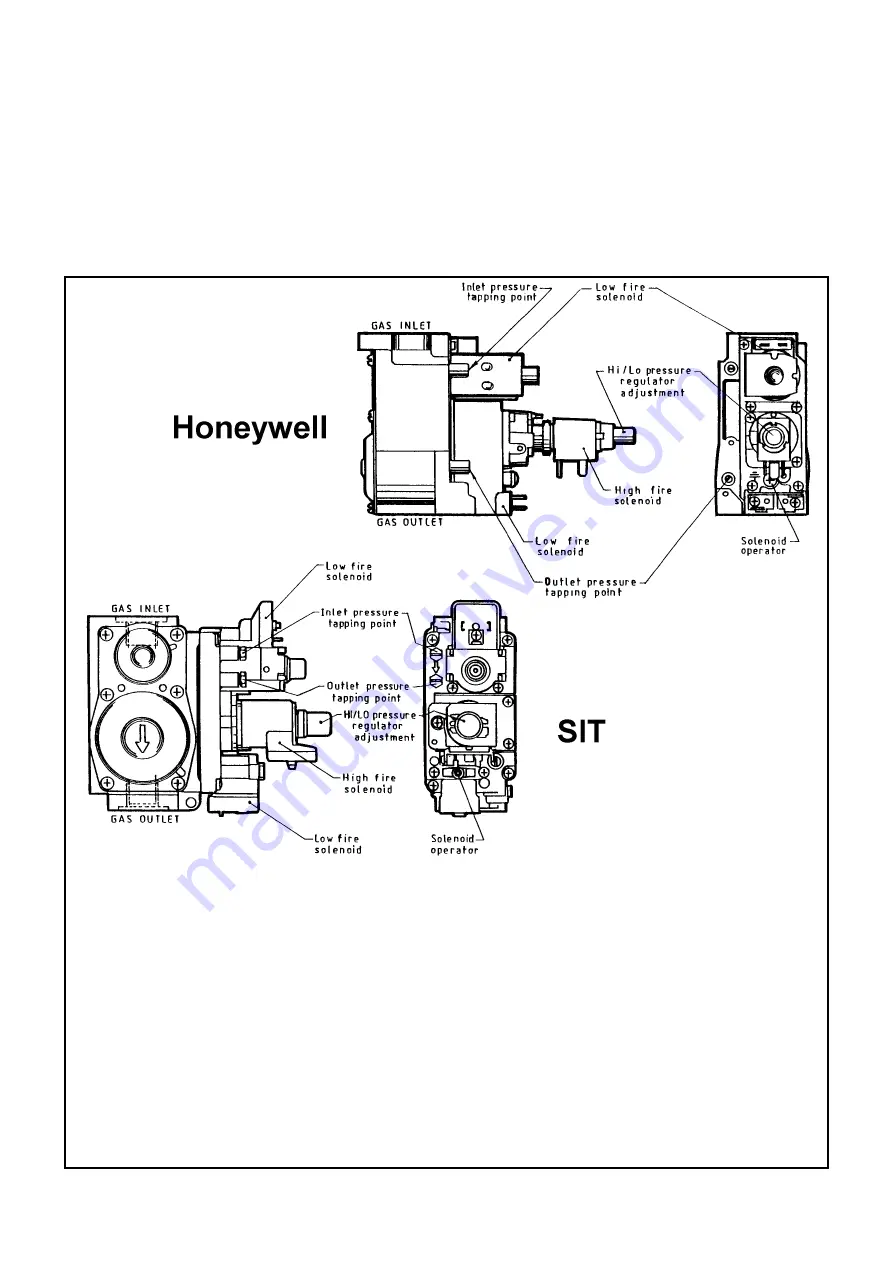
HAMWORTHY HEATING LTD
18
WESSEX 100 M
500001080/F
11.7 User’s Instructions
When the above is complete, the boiler owner or
their representative should be made aware of the
lighting and operating instructions fitted onto the top
face of the control panel. A practical demonstration
should be given describing each functional step.
This Installer's Guide and User’s Instructions should
then be handed over and be kept in a safe place for
easy reference.
11.6 Installation Noise
In order to avoid the possibility of noise from the
installation, care should be taken to follow the
manufacturer’s instructions. Particular attention
should be paid to minimum water flow rates. If
acoustic insulation is added to the boiler, care
must be taken not to impede combustion or
ventilation air flow. If in doubt contact the
manufacturer.
Figure 11.4.3 Diagram of Automatic Gas Valves
To adjust the low fire gas pressure, remove link G3 -
G4 on PCB. Nominally set the low fire gas pressure
by rotating the inner crosshead screw, c/w to increase
pressure, anti c/w to decrease pressure, whilst
keeping the outer nut from rotating. Turn the boiler off
then on again and fine trim the gas pressure.
Insert the high fire link G3 - G4 on the PCB; the
boiler should drive to high fire. Replace the
protective cap on the Hi/Lo pressure regulator.
Note! The low fire setting must always be set
last of all. The valves operation may be incorrect
if this is omitted.
Note!
It is also advisable to carry out this procedure
with all boilers firing.
ADJUSTMENT PROCEDURE.
Refer to Figure 2.2 to determine the low fire and
high fire gas pressures for the boiler being fired.
Information relating to propane firing can be found in
Appendix ‘A’.
Attach a manometer (suitable for 30mbar) onto the
gas valve outlet pressure test point.
Light up the boiler. Then remove the protective
cover from the Hi/Lo pressure regulator.
To adjust the high fire gas pressure, turn the outer
nut on the hi/lo pressure regulator, c/w to increase
pressure, anti c/w to decrease pressure.
Содержание Wessex 100 M100
Страница 39: ...Notes ...