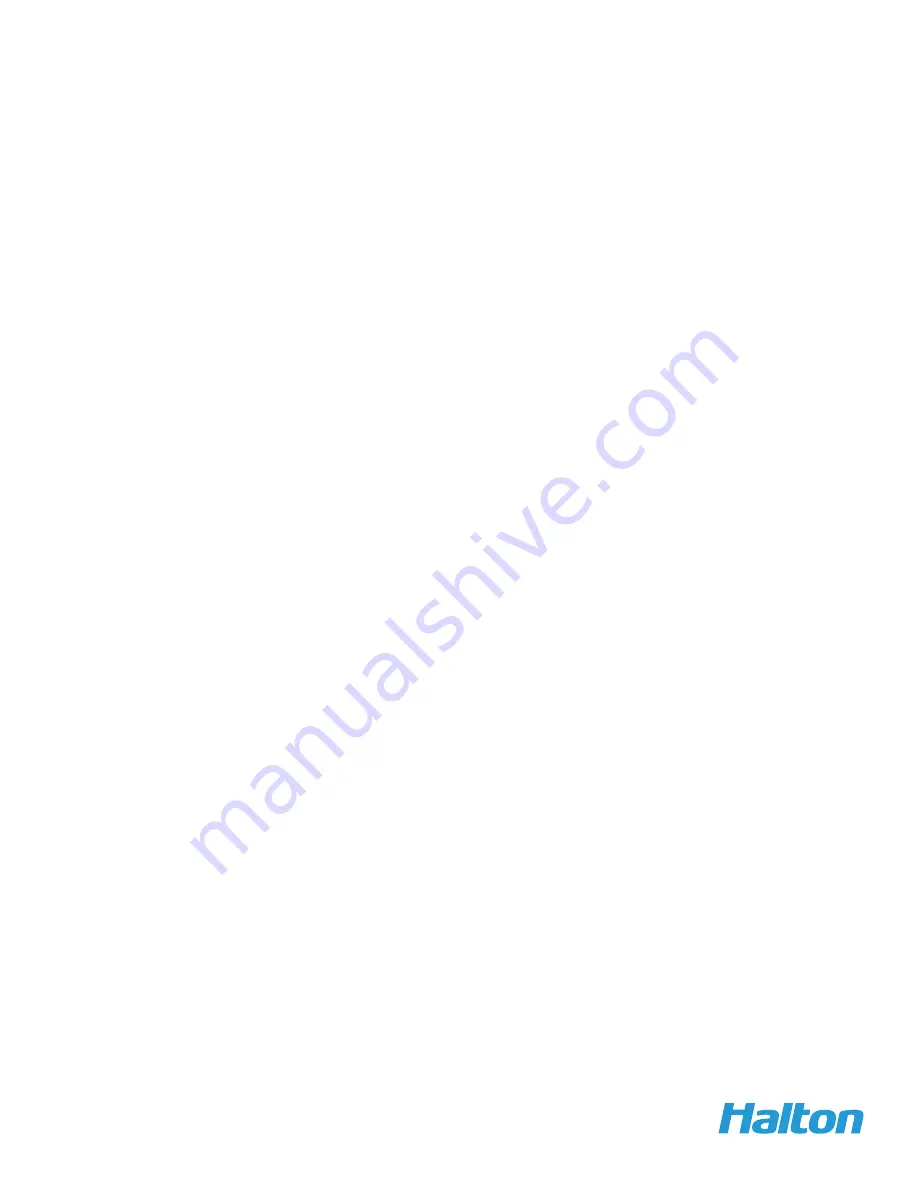
4
Capture Jet
®
with Water Wash Operation & Maintenance Manual
OM-0
06/1
120
16/re
v2/EN
A 120 volt circuit from the control panel to the make up air fan starter coil or relay.
There is a 2 wire circuit to the fire suppression micro switch for a dry contact closure to let the control panel know of
a fire condition under the hood.
There may be additional wiring circuits for fire alarm notification to a building BMS. This is optional.
Note:
The selector switch on the control panel controls the exhaust fan operation.
Please see job specific wiring connection information in the job submittal drawings and an additional wiring diagram is
included in the electrical control box shipped with the job. Additional copies may be obtained from the factory if this
wiring diagram is missing or lost. Please be prepared to provide the job order number (found on the sales invoice),
job name and address or submittal drawing series number when contacting the factory for this or other job specific
documents.
7. Plumbing service requirements:
1. Hot water supply to the control panel must be sized to accept appropriate volume of water measured in U.S.
gallons per minute at 40 psig/min. at a constant flow pressure of 25 psig at the hot water nozzles in the hood. Supply
the recommended hot water temperature of 120˚F (50˚C) to 140˚F (60˚C). Calculate water requirements by using
the longest water wash hood served by the control panel and multiplying the length of this hood, in feet, by 1.2. The
result will be the figure used for gallons per minute. Example: The longest hood connected to the control panel is
168” long. 168/12 = 14 feet, 14 X 1.2 = 16.8 gallons per minute.
2. Supply and connect 1” ips for hot water to control panel, provide and connect 1” lines to ventilator sections.
Supply and connect drains as specified from ventilator section(s) to floor drain as required by local codes. Waste
drain is 2” pipe. Do not use 90˚ elbows in drain line. If 90˚ bend is required use two 45˚ fittings. If traps are required
in drain line install it in the vertical section of the line. Supply and install grease traps as required by local codes,
sized to handle maximum volume as calculated above. Supply and install back flow preventers, anti-syphon valves or
vacuum breakers as required by local codes. Di-electric connections, where required by code on water supply feed
to panel, are to be supplied by mechanical trade. Internal piping in control panel is brass. Hot water lines should be
thoroughly flushed prior to connecting lines to control panel. Remove one of the spray nozzles farthest from water
intake to flush lines, replace nozzle when flushing is completed. Inlet and drain line attachment points at the hood
are illustrated on pg. 5.
8. Halton hoods come standard with high output, long lasting LED light fixtures. Optionally incandescent or recessed
fluorescent fixtures may be ordered. Please note only install 100 watt maximum light bulbs in incandescent light
fixtures. Fluorescent bulbs should be type T8, 36” or 48” long in fluorescent fixtures. **Note: Halton does not
provide bulbs for incandescent or fluorescent lights.
9. For multiple hoods end to end, or back to back see pg. 9 for Installation of Splice Strips and U-Channels.
10. If Closure Panels are supplied by Halton see pgs. 10 - 12 for details on the installation.
11. Protect the hood from damage under normal job site conditions, until all work is complete and system is ready to be
put into operation.
Содержание Capture Jet KVE-WW
Страница 10: ...10 Capture Jet with Water Wash Operation Maintenance Manual OM 006 112016 rev2 EN CLOSURE PANEL ASSEMBLY...
Страница 11: ...11 Capture Jet with Water Wash Operation Maintenance Manual OM 006 112016 rev2 EN...
Страница 12: ...12 Capture Jet with Water Wash Operation Maintenance Manual OM 006 112016 rev2 EN...
Страница 19: ...19 Capture Jet with Water Wash Operation Maintenance Manual OM 006 112016 rev2 EN...
Страница 26: ...26 Capture Jet with Water Wash Operation Maintenance Manual OM 006 112016 rev2 EN...
Страница 28: ...28 Capture Jet with Water Wash Operation Maintenance Manual OM 006 112016 rev2 EN FIELD WIRING DIAGRAM...