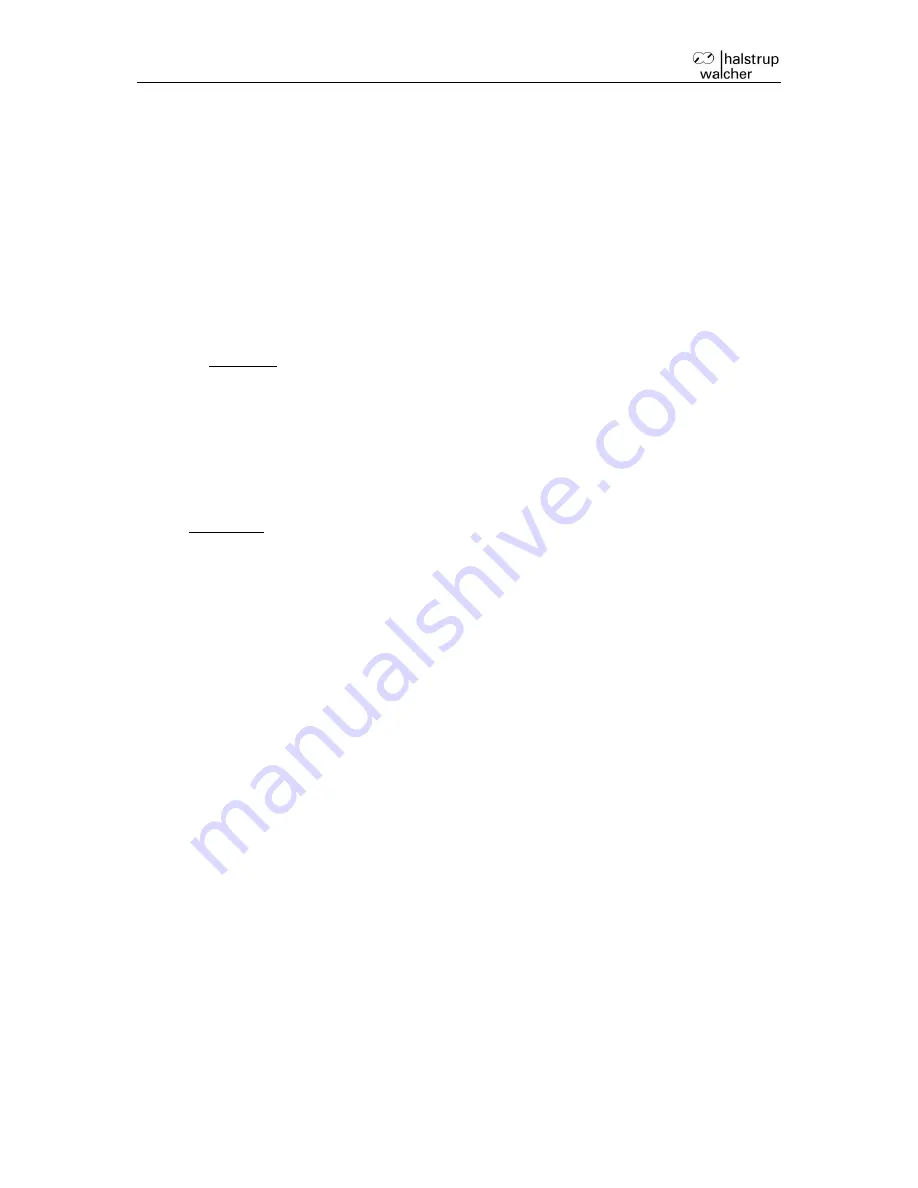
PSx3xxIO Instruction Manual
30
(b) Move the axle completely to the left (resp. bottom), then move the drive at no-
load (with opened collar) without loop to the lowest position (position 1200),
then close the collar. The drive is now capable of moving 250 rotations
(±100000 increments by default) to the right (resp. top).
(c) Move the axle completely to the right (resp. top), then move the drive at no-
load (with opened collar) to the highest position (position 101200), then close
the collar. The drive is now capable of moving 250 rotations (±100000
increments by default) to the left (resp. bottom).
2) Mount the drive in any position on the axle, close the collar, then adjust the
positioning range with the help of ISDU 128. ISDU 128 specifies the upper end of
the positioning range. By default, the upper end position is at +256 revolutions
(Position 102400). If the positioning range does not match the position currently
displayed after the installation of the drive, this can be freely selected between -
256 and 512 rotations.
Examples:
(a) After assembly, the displayed position is 51200 (which corresponds to the
delivery state). The positioning range should show solely to the right (or above)
Set
ISDU 128 to 152400.
(b) After assembly, the displayed position is 100000. The positioning range should
show solely to the right (or above)
Set
ISDU 128 to 201200.
(c) After assembly, the displayed position is 2000. The positioning range should
show solely to the left (or down)
Set
ISDU 128 to 3200.
Comments:
1) For the calculation of the upper mapping end (ISDU 128) (as in the above
examples) a safety margin of 3 turns (default 1200 steps) must be complied with,
because the maximum possible position value is 3 rotations underneath the top
end mapping. The smallest possible position value is 253 rpm below the upper end
mapping.
2) The specified step numbers or position values refer to the following settings, which
correspond to the delivery condition:
(a) reference value (ISDU 127) = 0
(b) actual value assessment, numerator (ISDU 124) = 400
(b) actual value assessment, denominator (ISDU 125) = 400
These 3 ISDUs influence the above step numbers or position values: With the
reference value, an offset can be achieved, with the numerator/denominator
assessment, a stretch or elongation (see below).
3) In the event of a change of the direction of rotation (ISDU 123), the referencing
value (ISDU 127), the upper mapping end (ISDU 128) and the upper and lower
limit (ISDU 129 and 130) are set to delivery state.
4) In the event of a change of the upper mapping end (ISDU 128) the upper and
lower limit (ISDU 129 and 130) are set to delivery state.
5) When changing the actual value assessment numerator or denominator (ISDU 124
or ISDU 125), the target value, the actual value, the reference value, the upper
mapping end, the upper and lower limit, the positioning window and the loop length
are re-calculated.
6) In the event of a change in the referencing value (ISDU 127), the target position,
the actual value, the upper mapping end as well as the upper and lower limits are
re-calculated.
7) If the user wishes to avoid any automatic adjustment of values in the
parameterisation of the drive, the optimal sequence when sending the parameters
is the following:
(a) direction of rotation (ISDU 123),
actual value assessment, numerator (ISDU 124),
actual value assessment, denominator (ISDU 125)
(b) referencing value (ISDU 127)
Содержание PS*3**IO series
Страница 37: ...Instruction Manual PSx3xxIO 37...